Following depressed conditions in 2020, domestic sales and export volume of plastic products are projected to rise by an average of 2.0-3.0% per year over 2021-2023. This will be helped by the anticipated recovery in the Thai and global economies, especially downstream industries, including packaging, electrical appliances, construction, auto parts, and medical devices which collectively account for almost 80% of domestic consumption of plastic products. However, there are lingering challenges for the industry over the next 3 years. These include uncertainty over the direction of crude oil prices (a primary input in the production of plastic resins), rising labor costs, and concerns over the environmental impacts of plastics at home and abroad that are discouraging the consumption of single-use plastic items.
Overview
Plastics are produced from hydrocarbons, most commonly from chemicals originating from crude oil distillation or natural gas separation processes. These initial processes yield products that are then separated into their component chemicals, including ethylene, propylene, styrene, phenol and acrylonitrile, which comprise the major inputs in the production of a range of plastic resins. There are different types of plastic resins, distinguished by properties such as ductility and heat-tolerance. And depending on demand from downstream industries, these resins may be molded and shaped into finished goods for use in a large range of applications (Figure 1 and Box 1). Recently, there has been growing interest to manufacture plastics from renewable resources, including from polylactic acid (PLA) derived from corn, sugarcane or cassava. While plastics produced from PLA are biodegradable, it is possible to use them in many applications that are identical to those of traditional oil-based plastics.
In 2019, the plastics industry accounted for 6.1% of Thai GDP, playing an important role in linking between the petrochemicals sector which supplies upstream inputs, with end-user industries (especially packaging, construction, auto assembly, electronics and electrical appliances, and medical equipment), and for which the plastics industry provides finished and semi-finished products.
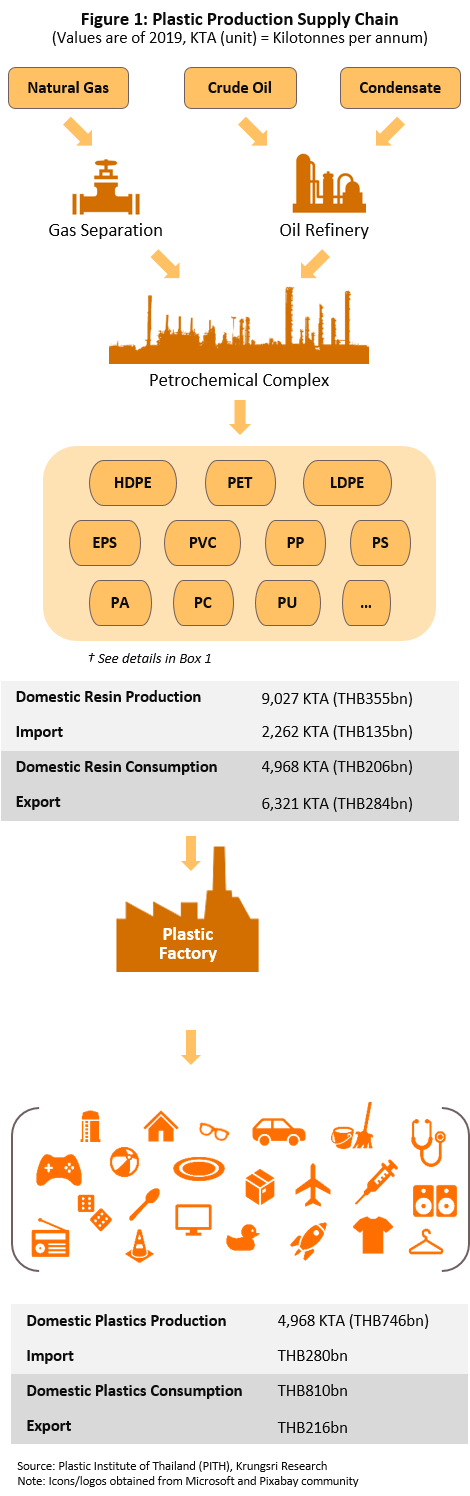
Box 1: The major plastics
Plastics can be categorized into 4 groups according to their properties.
Manufacturing plastic products involves melting and molding plastic resins, cooling the molded plastic, and final processing to produce the desired finished goods. Dyes and plasticizers may be added to change the color and characteristics of the goods and to make them more suitable for their intended use, for example by raising pH tolerance values to make them more resistant to fire or ultra-violet radiation, or by increasing their flexibility. There are many different ways to mold plastics but deciding on which technique to use depends on the final application. The main methods are: blow molding, which is suitable to produce bottles to package water, oil and shampoo; injection molding, which is normally used to produce kitchenware, toys and electronic parts, auto parts, and electrical appliances; compression molding, which is generally used to produce plates, bowls, cups and kitchenware made from melamine; and extrusion molding, which is used to manufacture plastic bags and sacks, and PVC water pipes. A survey by the Plastics Institute of Thailand in 2019 reveals 35-40% of Thai plastics producers use injection molding, followed films and blow molding[1]. Given the range of physical and mechanical properties displayed by different plastics (e.g., weight, moldability, flexibility, and gas- and water-permeability), these have assumed an extremely important role as upstream inputs into a large number of industries, with special plastics solving the problems unique to those downstream industries. For example, auto parts manufacturers use plastics to reduce the weight of components and so, increase fuel efficiency, producers of construction materials use plastic products that are durable and resistant to chemicals, and the medical equipment industry uses plastics to add value to products (Figure 2).

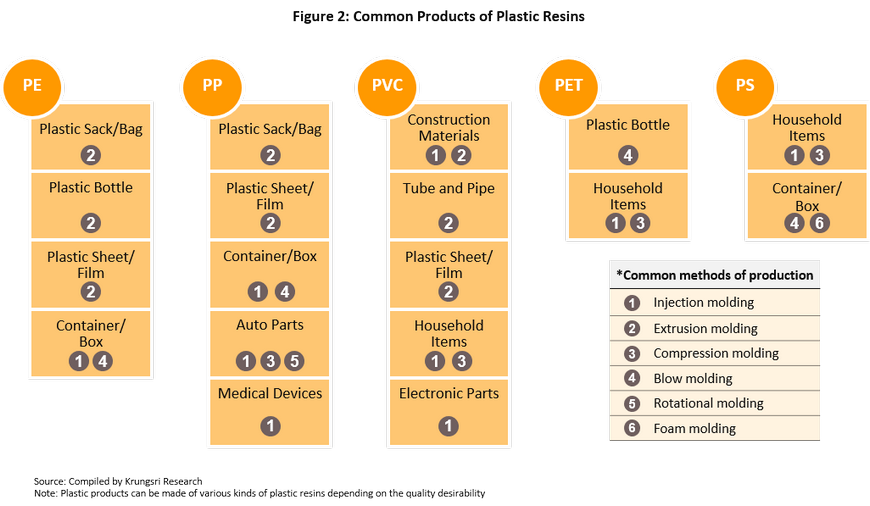
In 2019, 368 million tonnes of plastic were produced globally, a 2.5% increase from 2018[2]. Asia is the principal producing-area, accounting for 51% of the world total (Figure 3), with regional production led by China which produces 31% of all plastics manufactured globally. China is the world’s biggest importer of resins and the 3rd biggest importer of plastic products. After Asia, come North America (NAFTA region, led by the United States) which produces 19% of the global total, and Europe with 16%, led by Germany. In the downstream industries, the packaging industry is the biggest plastics consumer at 36% of global output, followed by construction (16%) and textiles (14%) (Figure 4).
Thailand occupies an important place in the global plastics industry. The domestic industry generates around THB 1.0 trillion annually. The industry benefits from a domestic petrochemicals industry that is both sizeable and highly-efficient compared to its competitors in the ASEAN zone. And because plastic resins sit downstream from the petrochemicals industry, this helps to increase the competitiveness of Thai manufacturers. Major Thai players are also skilled in the research & development of new products to accommodate constantly shifting market demands. In addition, by producing a wide range of resins (in both quality and price), Thai companies can support the activities of a large number of different industries. In 2019, Thai manufacturers produced 9.0 million tonnes of plastics, while the country imported just 2.2 million tonnes. 56% of output is consumed by export markets (Thailand is the world’s 11th biggest exporter of plastics and the 2nd biggest in the ASEAN zone after Singapore), with the remaining 44% used to manufacture products for domestic industries, most notably for players in auto assembly, electronics and electrical appliances, and construction. Therefore, Thai plastics converters are embedded in comprehensive supply chains that stretch from upstream raw materials (i.e., domestic producers of natural gas products), through intermediate goods (i.e., petrochemical players manufacturing plastic resins), to a large number of downstream industries.
There are currently more than 2,800 plastics converters active in Thailand, comprising 87% SMEs and 13% large players. The large number of SMEs is because of low entry barriers to the market given relatively small up-front investment costs. In addition, production utilizes only low to mid-level technology, and because of this, most of the output is commodity-grade products. As a result, competition is fairly stiff and margins are narrow. Most players that are active domestically are Thai companies (83.5%), 7.5% is controlled by Japanese, and 1.2% by the Chinese. In terms of geographical distribution, the majority of operations (81.5%) are clustered in the central region, especially in the Bangkok Metropolitan Region, Samut Prakan and Samut Sakhon, followed by the east (11.4%) and the northeast (3.1%) (Figure 5).

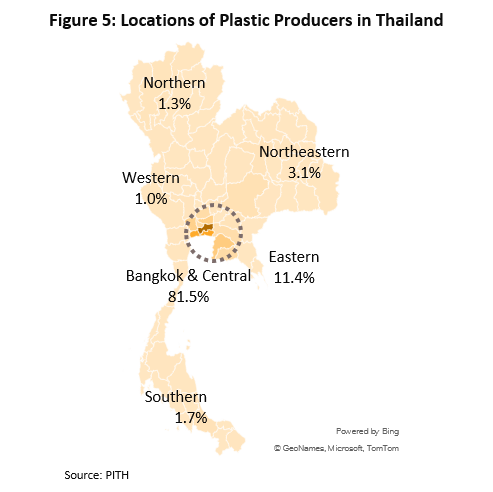
The domestic market consumes 80% of the output of Thai plastics converters. This is split into two primary segments: (i) end-consumer market, which meets consumer demand directly through the production of goods such as kitchenware, bags and straws; and (ii) suppliers to the end-user industries which comprise the five major markets – packaging, electronics & electrical appliances, construction, auto parts, and medical devices & supplies. The remaining 20% is exported, but much of this is low-value commodity-grade products including packaging (most important export segment) and cellular and non-cellular films. The main export markets in 2019 were the ASEAN zone (30.7% of all exports by value), Japan (19.2%) and the US (12.5%). Imports include plastic packaging (16% of all imports), non-cellular films (14.4%) and self-adhesive films (10.3%). The major sources of imports in 2019 were China (36.3% of all imports by value), Japan (21.6%) and the ASEAN region (14.7%) (Figure 6).
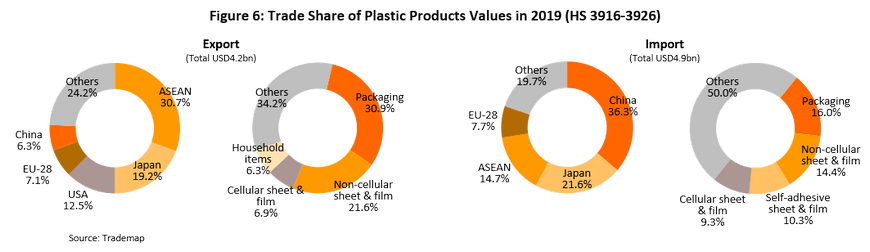

Generally, raw materials (i.e., plastic resins) account for around 70% of production costs, with another 10-15% coming from labor, 8% from energy and 7-12% attributable to other costs. In plastic packaging, (most important product category) the primary expense is for resins (50-80% of production costs). Total energy and labor costs will depend on the type of inputs used and the products manufactured; for plastic packaging that requires the utilization of more advanced production technology and more expensive machinery, depreciation and interest costs will be relatively high (Figure 7). Overall, the industry’s cost structure implies fluctuating crude oil and natural gas prices can have substantial influence on manufacturers’ costs and competitiveness.

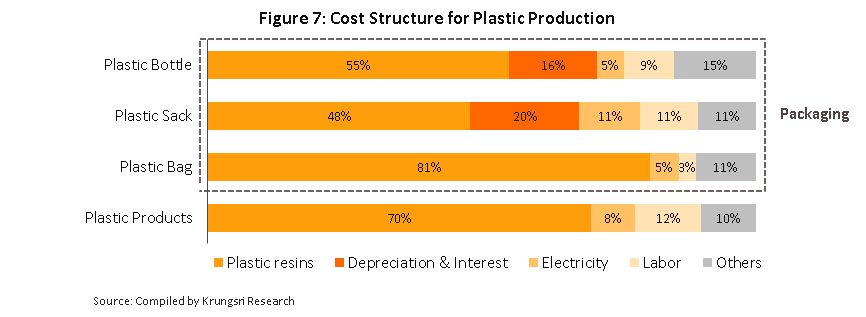
Situation
In 2019, a slowdown in both the global and domestic economies reduced demand for Thai plastics. The situation for the year is summarized below.
- Output of plastic resins rose by just 0.2% to 9.0 million tonnes in 2019. Imports slid 7.8% to 2.3 million tonnes. Resin prices also weakened with lower cost of raw materials (crude prices fell 8.8% and natural gas prices fell 17.9%) (Figure 8) and softer demand in the Chinese market.
- The value of converted plastics reached THB750bn (4.4% of Thai GDP) in 2019, down 4.0% from 2018 value. Plastic packaging was the most valuable product group with 24.1% share, followed by electronics & electrical appliances (23.0%), construction materials (11.4%), auto parts (11.1%) and medical supplies (7.3%) (Figure 9). By product type, packaging (e.g., plastic bags) was the largest by domestic sales volume, followed by pipes & connectors, and plastic films (Figure 10).
- In 2019, a total of 0.65 million tonnes of plastic products were distributed to the domestic market, down 0.8% (Figure 11). The drop was replicated across most product groups, including plastic films, plastic sacks, and houseware. However, some types of bottles, boxes and bags, as well as pipes & connectors used by the construction sector, moved against the headline figure and sales of these increased.
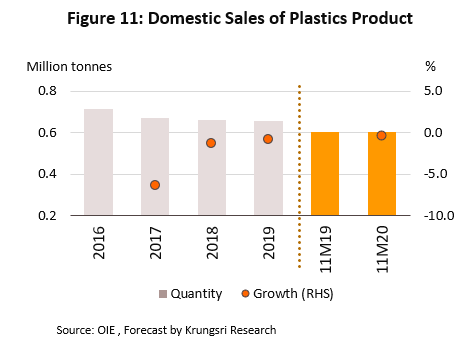
Ranked by unit value, the 3 top products are medical supplies, shoes and safety equipment, which combined account for 18.6% of total market value. However, despite having 25% share by volume, plastic packaging had the smallest unit value (Table 1).
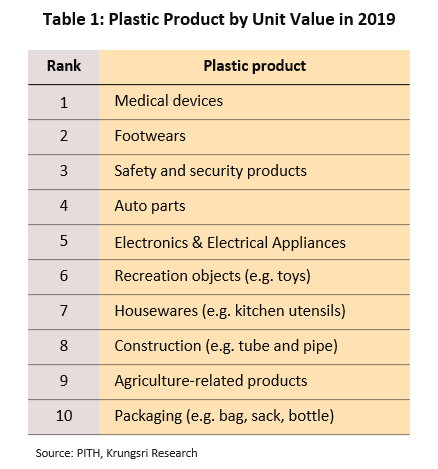
The 2019 international market[3] for Thai plastics is summarized below (Figure 12).
- Exports of plastic resins reached 7.1 billion tonnes in 2019, up 5.0% from 2018 data, export value fell 10.9% to USD9.1bn. The value of exports to many of the main export markets fell, including Japan (-18.0%), Vietnam (-16.9%) and Indonesia (-14.4%). On a flipside, shipments to China (Thailand’s biggest export market with 35% market share) rose 3.0%, but this was a sharp slowdown from +23.3% in 2018. Meanwhile, imports of plastic resins inched up 0.6% to 2.2 million tonnes valued at USD4.3bn (-8.8%).
- By volume, exports of plastic products soared 2.0% to 1.2 billion tonnes but by value, they slipped 2.9% to USD4.2bn. Major export markets include Japan (Thailand’s biggest market with 19.2% share) and China, but shipments to these two fell 3.5% and 3.1%, respectively. By product group, the worst performers included non-cellular films (-4.2%) and ‘other’ plastic goods (-9.8%). Meanwhile, imports of plastic products surged 6.9% to 0.9 million tonnes valued at USD4.8bn, largely unchanged from 2018.
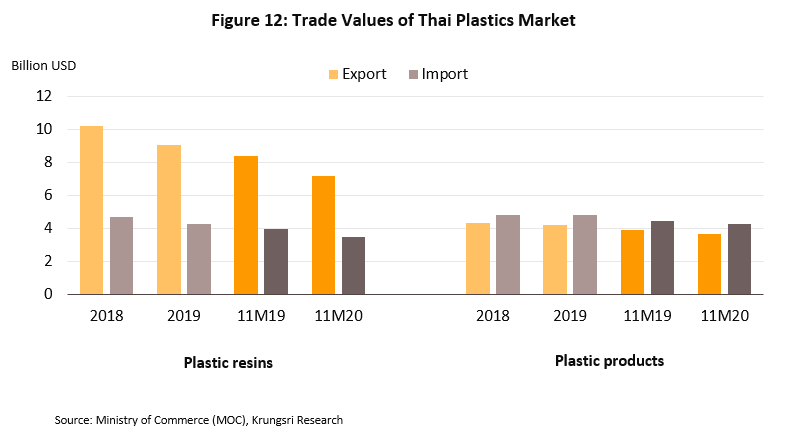
In 2020, global prices of plastic resins had tumbled along with oil prices. Simultaneously, many major industrial consumers of plastics (e.g., auto assembly, electronics & electrical appliances, and construction) were badly hurt by the COVID-19 impact on the global economy, and subsequent crash in manufacturing and trade, especially in the first half of 2020. Overall demand for plastic products contracted, but this was not the case for single-use items, especially medical devices, PPE, and food packaging; the pandemic had fueled a strong increase in demand for medical equipment and, with restaurants forced to shutter in many countries, there was a surge in demand for food delivery services. The 2020 business environment is described below.
- Output of plastic resins shrank, as reflected in the 2.8% YoY decline in the resin (TSIC 2013) manufacturing production index (MPI) for the first 11 months of the year. This drop was the result of moves by operators to run down existing stocks and, naturally, the global slump in demand for plastics following the COVID-19 pandemic.
- This decline in output of plastic products in 11M20 was seen across most product groups, including plastic packaging (-1.6% YoY) and ‘other’ plastic goods (-16.5% YoY). However, finished and semi-finished goods saw a slight increase (+0.9% YoY) (Figure 13). Overall, there was a sharp contraction in the market in the first half of the year, but in the latter half of 2020, as the government relaxed lockdown measures and implemented measures to encourage consumer spending, the economy began to rebound and life returned to downstream industries. Thus, the MPI for plastic auto parts (TSIC 29), electronic equipment (TSIC 26) and medical devices (TSIC 3250) returned to near pre-pandemic levels (Figure 14). Krungsri Research now forecasts 2020 output of plastic packaging and ‘other’ plastic goods to drop by 1.0% and 18.0%, respectively. But output of finished and semi-finished plastic goods is expected to rise by 1.0%.
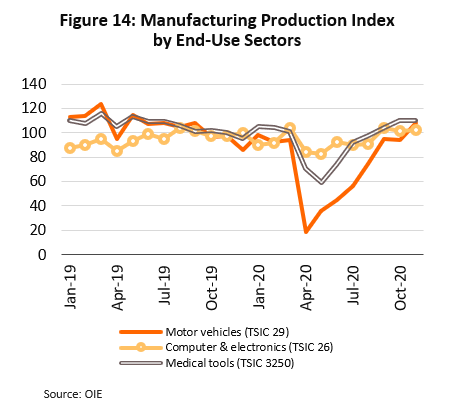
- In 11M20, domestic sales volume of plastic products[4] slipped 0.3% to 0.6 million tonnes. Again, declines were widespread, and included plastic containers (e.g., bottles, boxes and crates, -7.0% YoY) and plastic sacks (-11.6% YoY). On the bright side, government expenditure on construction projects helped to lift sales of plastic pipes and connectors by 15.1% YoY, while strong growth in food delivery services helped to boost demand for plastic bags by 3.3% YoY. For 2020, total demand for plastic products is forecast to grow by 1.5-2.0%.
- Through the first 11 months of 2020, exports of plastic resins dropped 7.3% YoY to 6.1 billion tonnes, but the drop in export value worsened to -14.5% YoY, with receipts totaling USD7.1bn. 11M20 exports of plastic products reached 1.1 billion tonnes, a rise of 0.5% YoY, but the receipts fell by 5.9% YoY to USD3.6bn. Product groups which saw a drop in export value included non-cellular films (-3.2% YoY), ‘other’ plastic films (-6.1% YoY) and tableware (-20.0% YoY). However, export value of plastic packaging rose 1.4% YoY. For the year as a whole, total export value plastic products is expected to rise by 1.0-2.0%.
Outlook
Krungsri Research forecasts that throughout 2021 to 2023, demand for plastic products will rise by an annual average of 2.0-3.0%, in line with the steady recovery of the global economy, which the IMF sees hitting 5.2%, 4.2% and 3.8% in each of those years. The IEA forecasts prices for Brent crude would remain below USD50/bbl during this period, and because crude oil prices have a strong influence on prices of plastic resins, the latter are likely to remain low for the next few years (Figure 15). Domestically, the Thai economy is expected to record average annual growth of 2.5-4.0% through to 2023. This would help to lift demand for plastic products in downstream industries, which should grow at a similar pace. Such downstream industries, especially packaging, electrical appliances, construction, auto parts and medical supplies, together account for 80% of the domestic market (by value) for plastic products. Krungsri Research projects both the domestic and export markets for plastic goods would grow by 2.0-3.0% per year from through to 2023 (Figure 16). Growth would be supported by the downstream industries as outlined below.
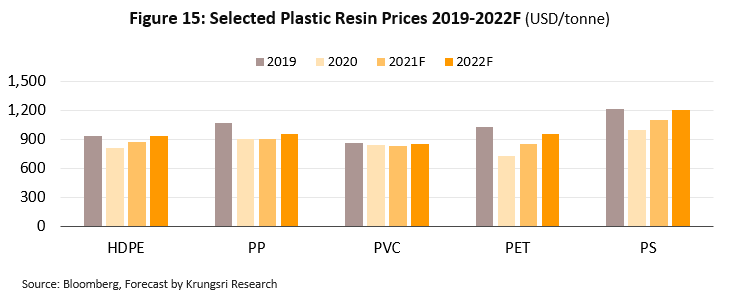
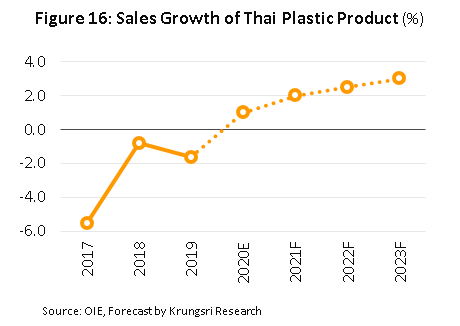
- Packaging: A survey by Smithers Pira indicates that during 2020-2024, the global market for plastic packaging should grow by an average of 2.8% per year, rising from USD0.9trn in 2019 to USD1.1trn in 2024. Likewise, the research organization Markets and Markets expects that by 2022, the market for flexible plastic packaging used in consumer goods will increase to USD130bn from USD97bn in 2016. In the Thai market, following a decline of 1.0-2.0% in 2020, Krungsri Research expects the output of plastic packaging to expand by 0.0-1.0% annually these few years (Figure 17). The stable or growing market will be supported by the move by many domestic industries to extend their use of plastic packaging, including manufacturers of food and beverage (e.g., frozen and processed food), pharmaceuticals and cosmetics, and the retail sector and e-commerce. At the same time, the COVID-19 pandemic has stoked greater demand for wrapped products, in hopes that would reduce risk of infection. This is a positive impact on producers of flexible plastic packaging (e.g., plastic bags, sacks, sheets and films). But recently, there has been a rising tendency to reduce consumption of single-use, non-biodegradable plastics made from fossil hydrocarbons, and this has been accelerated by the introduction of government policy that is pushing those trends further in this direction. This, coupled with the development of more environmentally-friendly bioplastics, could act as a counterweight, pulling demand for basic plastic packaging in the opposite direction.
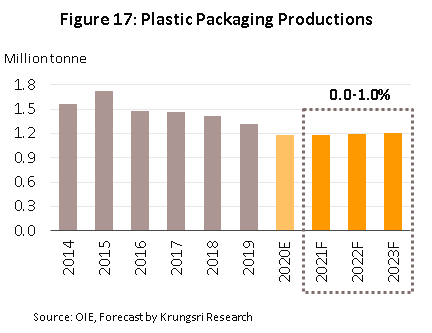
- Electronics and Electrical Appliances: Krungsri Research expects that through 2021-2023, production of electronic parts will expand slightly on stronger demand in export markets. Output of hard disk drives (HDDs) are forecast to rise by 2.0-3.0% on greater demand for high-capacity units for use in cloud computing and data center applications, while output of integrated circuits (ICs) will grow at a slightly higher rate of 3.0-4.0% driven by rising demand for semi-conductors and lighter smartphones and tablets. Production of electrical appliances will strengthen led by rising sales in both the domestic and export markets. In the domestic market, growth is forecast to average 3.0-4.0% annually, buoyed by an improving real estate market (Figure 18). Meanwhile, export growth would average 2.0-3.0% per year (Figure 19), supported by the Asian market which is expected to register strong growth for the next few years. It should also be possible for Thai manufacturers of some white goods, including air conditioners, refrigerators, cookers and microwaves, to replace China shipments to US buyers, which have fallen victim to the US-China trade war. These factors will translate into greater demand for plastic parts and related products.
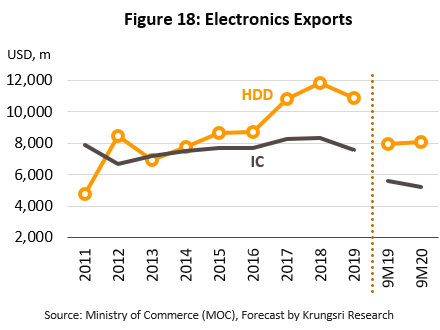
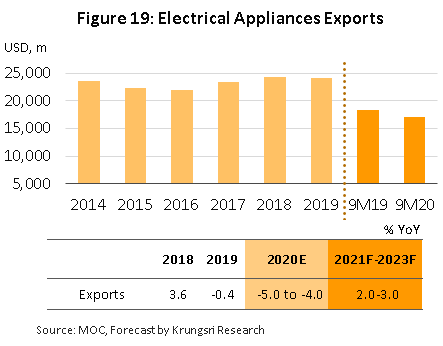
- Auto parts: After tumbling by 32.0-33.0% in 2020 (Figure 20), the domestic market will benefit from an anticipated 3.0-4.0% annual increase in vehicle assembly, which would lift annual output to 1.39-1.42 million vehicles. On average, modern vehicles have up to 50% plastic content but these components account for just 10% of the vehicle’s weight (source: Plastics Institute of Thailand). Output in the auto sector will be boosted by easier conditions to qualify for investment support from the Board of Investment, which will help to accelerate output of eco-cars and electric vehicles. Beyond this, demand for spare and replacement parts from the replacement equipment manufacturer (REM) market would rise among with more vehicles on the road that are over 5 years old (forecast to rise by 6.0% per year). Growing global output of autos will also help to push up auto parts exports in the coming period. Another positive factor could be trade diversion helping Thai suppliers to step into supply chains that are disrupted by ongoing uncertainty triggered by the extended US-China trade conflict. Euromonitor forecasts that after shrinking 13.0% in 2020, the value of exports of auto parts from Thailand will grow by 9.2%, 5.4% and 1.8% in 2021, 2022 and 2023, respectively, which will lead to greater demand for products supplied by the plastics industry.
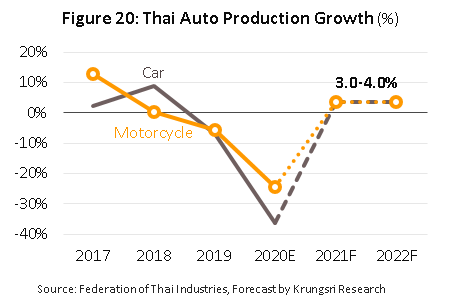
- Construction: Construction spending is projected to rise steadily thanks to the government’s plans to step up spending on infrastructure megaprojects, especially those connected to the development of the Eastern Economic Corridor (EEC). Construction work on many projects here is scheduled to start in 2021 (e.g., Phase 1 of high-speed rail link to connect 3 airports - Suvarnabhumi, Don Muang and U-Taphao, and Phase 3 of Map Ta Phut and Laem Chabang ports). Krungsri Research estimates that in 2021-2023, government spending on construction will rise by 6.0-7.0% annually, compared to +5.0% in 2020. And through the crowding-in effect, this expenditure will help to attract greater private-sector investment in industrial, commercial and residential construction. Given this, after falling 3.0% in 2020, private-sector investment is predicted to increase by 1.0-2.0% per year over the next 3 years. This will help to support stronger demand for plastic-based construction materials, such as sheeting, pipes and connectors (Figure 21).
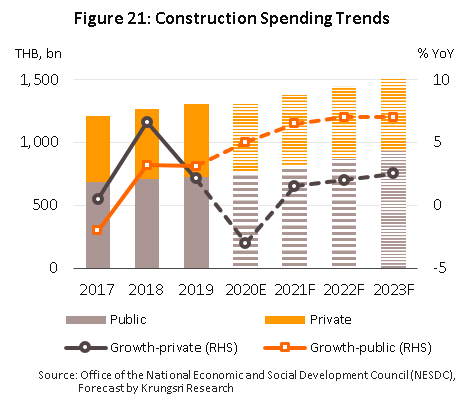
- Medical supplies: Following 3.0% growth in 2020, the value of medical supplies distributed to the domestic market is forecast to rise by an average of 7.5% per year over the next 3 years. At the same time, export value is expected to increase by 4.2% annually, having jumped 35.0-40.0% in 2020 (Figure 22). Growth in the domestic and international markets will be supported by the following: (i) Globally, societies are aging and this will naturally push up cases of chronic and severe non-communicable diseases (NCDs), which would in turn stoke greater demand for modern, high-tech medical equipment. (ii) There is a rising number of cases involving communicable diseases and NCDs, including hypertension, diabetes, chronic obstructive pulmonary disorder (COPD) and cardiovascular disease. (iii) Private-sector hospitals are investing in building new facilities and expanding the range of services that they provide. For example, some are building specialist centers to offer more complex treatments. (iv) In Thailand, the government is providing targeted support for the healthcare sector by offering investment support to those investing in the production of medical devices or parts. In addition, the COVID-19 pandemic has increased awareness of personal well-being in Thailand, which would boost demand for medical equipment related to personal and public health. As such, consumption of plastic parts, films, sheets, tubing, and other goods by the medical devices sector is expected to rise.
Opportunities and challenges faced by the Plastics industry
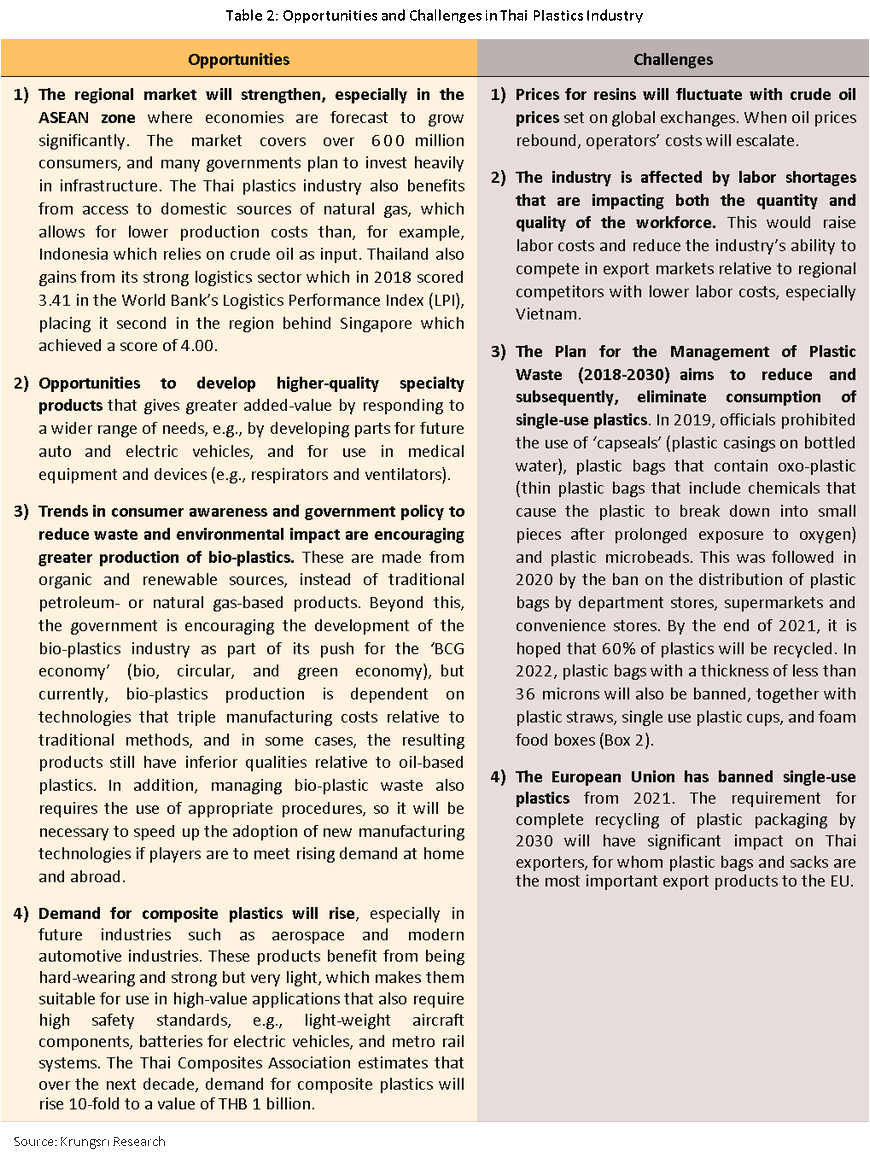
Krungsri Research view:
Over 3 years from 2021 to 2023, the plastics industry should see decent growth. The industry will gain from better market conditions for downstream industries, most importantly packaging, auto assembly and auto parts, electronics & electrical appliances, and construction. In addition, government measures to boost investment especially in the ‘new S-curve’ industries will also benefit plastics producers that are part of these supply chains. However, there are lingering challenges and players will face stiff competition and the growing movement to reduce and eliminate the production and consumption of single-use plastics. This would cap profit growth, although operators that control comprehensive and extensive supply chains from upstream raw materials through to downstream finished goods, and which are able to successfully manage stocks, sales and distribution, will be well-placed to maintain their profitability.
- Plastic packaging: In this segment, strong competition on price and rising environmental awareness that is reducing demand for core products (e.g., plastic bags) will cap growth. However, producers of flexible and semi-flexible goods will see better growth thanks to stronger demand from buyers in the food & beverage industry and in the retail and e-commerce sectors. Players that employ advanced production technologies and produce a wide range of high-quality finished goods should be able to maintain their growth trajectories.
- Plastic films, pipes, straws and flexible tubing: Earnings growth should be stable for manufacturers of these goods thanks to an expansion in downstream industries, including food processing and sales, construction and agriculture. However, this will not hold for producers of drinking straws, which could experience slower earnings growth. Players will would also experience strong price competition due to the large number of companies active in this segment.
- House- and tableware: Earnings will rise but only slowly as competition worsens. There will be increasing pressure from overseas producers (especially China) which have lower production costs. This increases the risk of profit margins being steadily eroded.
- Other plastic parts and products: Earnings should strengthen in line with improving market conditions in downstream industries that are buyers of plastic products, e.g., auto parts and assembly, electronics & electrical appliances, and medical supplies. However, producers would face stiffening competition, especially from foreign-controlled operations in both Thailand and overseas (notably in China) which have lower production costs. Some players are also excessively reliant on sales to a few major buyers.
Over the mid- to long-term, players will need to overhaul their business models if they wish to maintain their growth rates. This will likely include overhauling production lines to emphasize the manufacture of high-value plastics that meet the needs of more specialist, niche markets, and the growth of Thailand’s future industries – medical devices, electric vehicles, robotics, and aeronautics. In the face of growing global concerns over the environmental impact of plastics, players will also need to consider producing environmentally-friendly bio-plastics made from agricultural inputs such as cassava, palm and sugarcane. This would benefit from government efforts to attract investment, and which the government hopes to establish as one of Thailand’s rising industrial stars.
[1] This involved a survey of 2,825 manufacturers, or around 70% of the companies active in the industry. It should be noted that manufacturers may use more than one molding method.
[2] Source: PlasticsEurope
[3] Source: Ministry of Commerce
[4] Source: OIE. Plastic products include bags, sacks, containers (e.g., bottles, boxes and crates), sheets and films, pipes and connectors, and tableware.