Outlook
For full year 2020, auto parts output is projected to contract significantly relative to 2019. The global pandemic had forced auto assembly lines worldwide to halt production temporarily in the first half of the year and slashed consumer purchasing power. This had badly affected demand for OEM parts. However, the resilient REM market will help to offset some of the impact. Industry revenues in 2021 and 2022 would also be supported by a recovering economy, which will lift demand for auto parts.
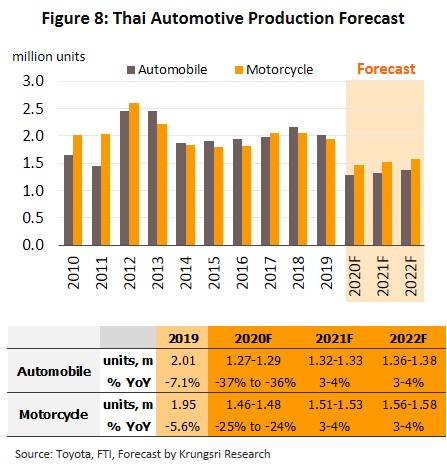
Domestic market: Thailand’s auto parts output is projected to tumble this year but would recover in 2021 and 2022, when the OEM market start to benefit from the recover in the auto sector (Figure 8). Krungsri Research forecasts that for 2020, a 5% fall in global GDP and domestic recession would cause Thai GDP to shrink by 10.3%. Coupled with tighter restrictions for auto loans, these would reduce auto output by 36-37%, the worst in 21 years. For motorcycles, the contraction would be smaller at 24-25% but that would still be a new low. The situation should improve again in 2021 and 2022, and annual output of autos and motorcycles is expected to rise by 3-4%. This would be driven by stronger economic fundamentals and pent-up demand, especially replacement demand for vehicles bought under the First-Car Buyer scheme which would be 8-9 years old. Additionally, several manufacturers which had received investment support for eco-cars and EVs will need to step up production. Against this, the REM market should see steady growth given the 6% average annual growth in the number of vehicles over 5 years old on Thai roads. In this segment, vehicles bought under the First-Car Buyer scheme will be an important market because they would start to need new parts. However, the falling number of cars below-5 years old suggests the accessories market will experience slow growth (Figure 9).
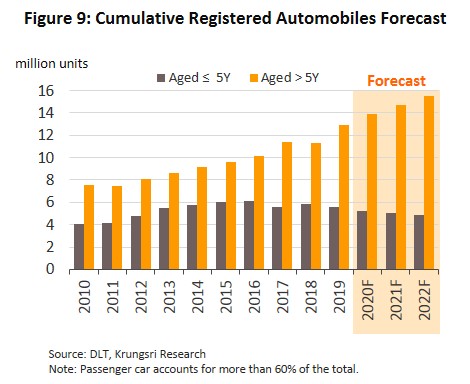
Exports: Export value will fall in 2020 in line with weaker global auto output. But in 2021 and 2022, the direction will reverse. The recovery in the global auto sector will be sustainable and lift auto parts output. The lingering uncertainty over US-China trade relations could also benefit Thailand if trade diversion brings larger orders for Thai manufacturers. Beyond this, manufacturers may respond to this year’s supply chain disruption through improving their resilience to weather future crises by diversifying geographical locations and moving some production capacity to Thailand. If this happens, it would mean the Covid-19 pandemic would effectively strengthen Thailand’s auto parts industry by creating opportunities for manufacturers to improve the quality of their operations and master manufacturing technology, and place them in a better position to expand their export markets.
However, despite the potentially optimistic factors, there are still challenges for the industry. (i) The United States-Mexico-Canada Agreement (USMCA) took effect on July 1, 2020. This means imports of autos between the signatories are now zero-rated when at least 75% of the parts used in these are manufactured in the signatory nations; this could hurt imports of auto parts from Thailand (currently, 21.2% of Thailand’s exports go to these three countries). (ii) The US may implement anti-dumping measures and counter-vailing duties on tires imported from Thailand (current duties are 3.7%). The authorities are considering the situation and would make a decision between November 2020 and May 2021. If the decision is unfavorable for Thailand, Thai exports to the US will suffer and manufacturers based in Thailand may decide to move their operations to another country. (iii) Manufacturers for the REM market (over 1,100 Thai operations, mostly tier-2 and tier-3 manufacturers) could face stronger competition from overseas players which move production to Thailand and tier-1 manufacturers (most of which currently produce goods for the OEM market), to hedge against risk by penetrating the more stable REM market.
Over the long-term, Thai auto parts manufacturers may be hurt by government policies to encourage investment in the production of hybrid and battery electric vehicles. The government is targeting 1.2 million electric vehicles on the road by 2036. However, the domestic market for electric vehicles will grow slowly initially because it will continue to be dominated by hybrid electric vehicles (HEVs) and plug-in hybrid electric vehicles (PHEVs). But because these vehicles use standard parts for internal combustion engines (ICEs) alongside their battery-powered components, OEM auto parts manufacturers will not be strongly affected by these developments in 2020-2022. IN the subsequent 4-6 years, the BEVs segment is projected to surge and market share will grow with positive developments in lithium-ion batteries and prices drop12/. In 2010, lithium-ion batteries cost USD 1,200/kWh, by 2020, this would drop to USD 156/kWh. Bloomberg sees the price of BEVs moving close to prices for ICE-powered vehicles by 202213/ (for similar types of vehicles). These growth trends in the BEVs market will be a major turning point for Thai auto parts manufacturers, which will need to adjust to a rapidly-changing industrial landscape. The industry had been focusing strongly on developing the supply chain for internal combustion engines, but as BEVs become more popular, the number of parts by required auto manufacturers will shrink. The typical BEV drivetrain has about 20 parts compared to over 2,000 in an ICE vehicle. In BEVs, the battery - rather than the engine - will be the major component and is expected to consume up to 30% of total production costs for a BEV.
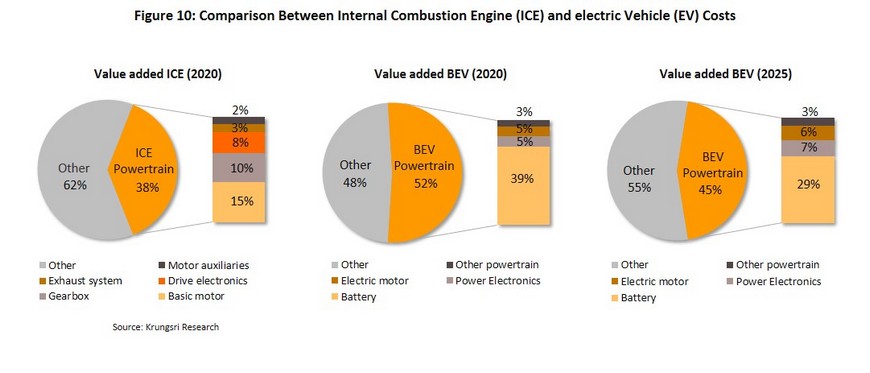
There have been rising investment in Thailand to produce auto parts for EVs, especially batteries. These include the development and production of a nickel-metal hydride battery by Toyota and a lithium-ion battery by BMW. And, as the EV market matures, it will affect demand for a wide range of OEM parts, including engines, radiators, exhaust systems, fuel systems, petrol tanks, ignition systems and gears. But there will still be demand for products such as suspension, body work, lighting systems and interior fittings. Some BEVs also use electronic control systems to reduce wear on parts (e.g. tires and brake pads). Future automated driving systems will also be safer and reduce the number of accidents, which would mean lower demand for REM parts.
In the coming period, EVs will play an increasingly important role in the Thai auto industry. This will reshape the industry’s supply chains which are currently structured in a strictly linear fashion. Orders filter through in a fixed direction through the layers in the auto parts industry (Figure 11). They include: (i) Tier 1 suppliers, which produce goods that meet the quality set by the major auto manufacturers, allowing them to supply to these players directly; (ii) Tier 2 suppliers, which supply parts to Tier 1 producers and may benefit from technology transfer, and (iii) Tier 3 suppliers are small outfits that supply to Tier 1 and Tier 2 players. Navigating the linear supply chain is cumbersome and it can take a long time for an order to percolate through the levels. To respond to just-in-time delivery, it is often necessary for suppliers to maintain high stock levels, making this type of operation suitable only for mass auto production where only economies of scales can justify involvement. However, the manufacture of EVs are more dependent on robotic and automated production lines (to ensure precision) and the use of hi-tech end-user products. They include automatic driver assistance, automated impact detection sensors, automatic speed controllers and on-board systems that connect with online data. They are required to create a smooth travel experience, for example by collecting data on weather, road and traffic conditions, or downloading relevant maps. In future, this will also extend to continually improve automated driving assistance (Figure 12). Because of these differences, the EV supply chain often diverges markedly, taking a circular, networked form rather than a straight line from start to end (Figure 13). The network would comprise auto parts suppliers, device manufacturers, telecom companies, online players and IT suppliers. The participants have a non-hierarchical relationships with each another, which helps to accelerate production and gives greater flexibility. Supplier would not need to maintain excessive stock. As a result, the system is better able to respond to a wider range of needs.
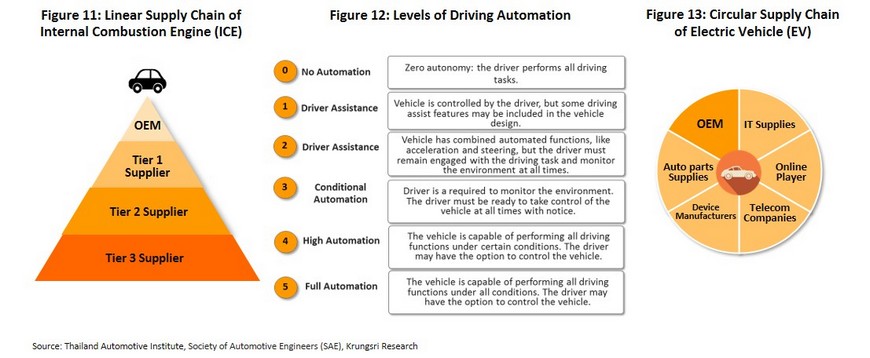
Krungsri Research view:
Alike elsewhere in the economy, the Covid-19 pandemic and resulting drop in spending power in Thailand and worldwide will slash revenue in the auto parts industry in 2020. Demand for OEM parts would drop but that would be partly compensated by resilient growth of the REM market along with a rising number of vehicles on Thai roads. In 2021 and 2022, the situation should start to recover as economic activities return to normal and lift demand for auto parts.
- Manufacturers of parts and spares: Earnings will shrink sharply in 2020 due to the weak global economy. However, there would some recovery in 2021 and 2022. Demand for OEM parts would grow, premised on the projected 3-4% annual growth in domestic auto output. However, the REM market should be less volatile and expand in line with near-normal growth in the number of vehicles registered in the country. Meanwhile, exports would be threatened by the USMCA agreement effective July 1, 2020, which exempts autos from import duties when shipped between the signatory countries, if they are built mainly from parts produced in those countries. This could adversely hurt Thailand’s exports to the US, Canada and Mexico. The extended US-China trade conflict could also weaken the economies of overseas export destinations.
- Tire manufacturers: In 2021, the US may impose anti-dumping measures on Thai tire manufacturers. If they do that, American manufacturers which have production facilities in Thailand (e.g. Goodyear and Dunlop) may not be seriously affected, but those from other countries (including Thai-owned operations) could be effectively locked out of the US market. Meanwhile, the REM market will grow with the national vehicle fleet.