- The Thai auto parts sector is forecast to see continuing growth through the period 2019-2021 on annual increases in domestic demand of 0-5%. This demand will be both for parts used in the assembly of new automobiles and motorcycles (the OEM market) and for spares and replacement parts (the REM market), demand for which will expand in step with the increasing size of the national vehicle fleet.
- Exports of auto parts are also forecast to rise thanks to the increasing number of foreign companies that have set up production facilities in Thailand, and although players will feel the pressures of the US-China trade war, this will also open opportunities to increase exports to the US market.
Overview
The auto parts sector constitutes an important link in the automotive production supply chain and from 1963 onwards, it has benefitted from being the recipient of government support[1], with this being particularly focused on encouraging investment in the production and use of the most important auto parts. This has been achieved through several means, which have included: (i) promoting the domestic use of auto parts by increasing import duties on ‘complete built-up’ (CBUs) and ‘complete knocked-down’ units (CKDs), Currently, free trade agreements with various coustries causing such tax to decrease; (ii) the implementation by the BOI of measures (including tax exemption and the waiving of import duties on machinery) to attract foreign funds for investment in the establishment of auto parts production facilities in Thailand; and (iii) during the first phase of the sector’s history, the issuing of local content requirements, which specified the proportion of locally-produced parts that had to be used in vehicles assembled in Thailand. Although these requirements have now been abolished[2], vehicles assembled in Thailand typically use a high proportion of locally sourced parts. Indeed, the components used in Thai-produced passenger automobiles and pickups, by value, the figures are around 60-80% and 90% respectively, and in the case of eco-cars the figure is also 90%, while motorcycles are almost entirely domestically manufactured.
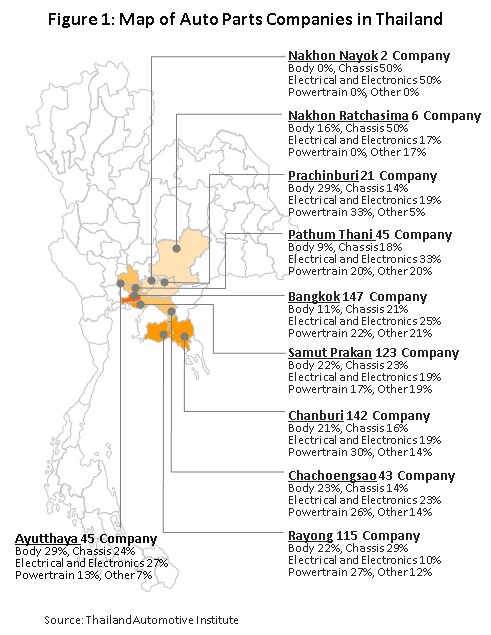
The government’s measures to encourage investment in the auto parts sector described above have had the effect of stimulating growth for both Thai and international players. Major global players which have established factories in Thailand include Robert Bosch, Denso, Magna, Continental, ZF, Aisin Seiki, as well as Japanese auto parts producers that are in the supply chain of the major Japanese automotive manufacturers (Table 1). Examples of major Thai and Thai-joint ventures active in the sector include Thai Summit Autoparts, Sammitr Autopart Company, Somboon Advance Technology and Thai Auto Place Part Company. The majority of these players have benefited from government assistance to the sector, which has helped a variety of different segments, including: (i) Auto parts fabricated from rubber, manufacturers of which benefit from access to Thailand’s abundant supplies of rubber. These products include hosing, belts, window seals and vehicle tires, the latter being products that involve high-tech manufacturing processes. (ii) Engines and powertrains. Producing these parts involves a lengthy supply chain[3] and assembly of engines in internal combustion engine-powered automobiles swallows over a third of all production costs. In fact, when developing engine production capacity in Thailand, Thai’s government made the decision to support the entire supply chain, including production of radiators, exhaust and fuel systems, petrol tanks, ignition systems, gears and so forth. (iii) Parts for use in the assembly of electric vehicles (EVs). These are the latest target of government support, which is taking the form of a package of measures covering vehicle assembly and the production of major parts such as batteries, traction motors, air-conditioning systems and components, battery management systems, control systems, on-board chargers, plug-in chargers, DC/DC converters, inverters, portable electric vehicle chargers, electrical circuit breakers, front and rear axles for electric buses, and EV smart charging systems. The upshot of this has been to encourage a steady increase in applications for investment support by EV and EV parts manufacturers[4], especially for batteries, a particularly important part of EV production (batteries account for approximately 30% of the production costs of EVs). As of May 2019, the government is trying to encourage the speeding up of investment in electric vehicle production, both battery electric vehicle (BEVs) and hybrid electric vehicles (HEVs), by allowing companies that apply for investment support for BEV production to also apply for HEV production (applications for which need to be submitted by December 31, 2019) provided that in addition to producing HEVs, they produce at least one major part for an HEV within 3 years of their application being accepted and in addition, within 3 years of beginning the assembly of HEVs, they must also produce a further 4 important HEV parts. As regards BEVs, manufacturers receiving BOI assistance must begin production of at least one important BEV part and assembly of BEVs within 3 years of commencing production of HEVs. For the purposes of BOI investment support, an ‘important’ auto part is one of the battery, the traction motor, the drive control unit (DCU) or the battery management system (BMS).
In terms of the market for auto parts, the domestic Thai market is the most important, accounting for around 60-65% of the sector’s total income. This includes both parts used in the assembly of new vehicles (the original equipment manufacturer, or OEM, market) and those used as replacements and spares (the replacement equipment manufacturer, or REM, market).
- The OEM market: This segment has grown in step with the growth of the Thai automotive production capacity and by value, it represents 30-40% of the total domestic auto parts market, a situation that is helped by the fact that vehicle manufacturers in Thailand are now using over 80% domestically produced parts. Those remaining parts which are imported tend to be those that are not produced in Thailand, usually because their production is dependent on high technology processes and these are thus imported from the manufacturer’s parent company or a supplier of the parent company. Examples of products in this category include the microcontroller chips (MCUs), which are exported from Japan to Thailand, and some of the parts used in Chinese trucks and buses that, following the establishment in Thailand of production facilities by Chinese manufacturers, are now assembled in the country. Examples of the latter include MG automobiles (SAIC Motor-CP), DFSK trucks (Tong Fong), and Golden Dragon buses (Bestrin Group).
- The REM market: The remaining 60-70% of the market for auto parts is taken by the REM market. Growth in the REM market tracks growth in the total number of vehicles registered in the country, as wear and tear of parts with time and use helps to determine demand for replacements. Parts are typically distributed through dealers’ service centers, wholesale and retail suppliers, and garage. Imports of replacement parts account for 10-20% of total import value of REM market, most coming from Japan (41% of all REM imports by value) and China (17% by value of the market) as they are a growing presence within it.
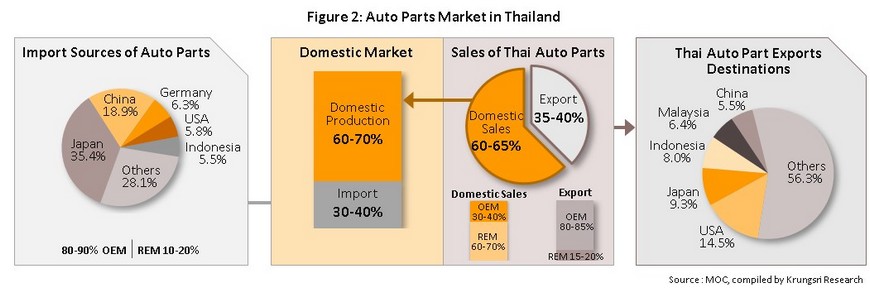
Exports contribute around 35-40% of all income to the Thai auto parts sector, split between OEM and REM markets, with the former being the more significant; for 80-85% of exports, leaving 15-20% for spares and replacements in the REM market. The most important exports are of parts for engines, electrical wiring, bodywork, windows, gears, and tires and other rubber products. These auto parts of Thailand are able to compete successfully in world markets because of the extensive development of the sectoral supply chain, which is extremely comprehensive, and this allows Thai suppliers to exploit economies of scale and to produce parts at a quality that meets requirement of automobile assemblers. Thailand also take advantage of its geographical position, which puts the country at the heart of the ASEAN zone[5] and for these reasons, Thailand is both the center of auto parts manufacturing in the region (Figure 3) and an important player in the global sourcing of auto parts. Indeed, in 2018, Thailand ranked 1st in the ASEAN zone for the export of all types of auto parts and 14th globally. In detail, Thailand’s rankings were 5th for the export of tires, 6th in terms of motorcycle parts (not including engines and tires), 12th for the export of engines, and 14th for automobile parts (excluding engines and tires). By value, 28% of Thai exports go to the ASEAN zone, with the Philippines, Indonesia and Vietnam being especially important. Other export markets include the United States (another 15% of exports) and Japan (9%).
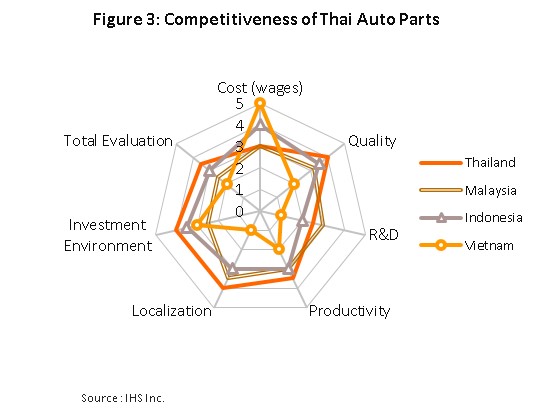
Structure of Thailand auto parts producers
At present, there is a total of 1,800 operators active in the auto parts sector in Thailand (source: Thailand Automotive Institute).
- Tier-1 manufacturers are those which produce high-quality products that meet vehicle manufacturers’ specifications. These parts may be used either in the vehicle assembly process (the OEM market) or as replacement parts (the REM market). Currently, there are 720 tier-1 operators, of which 47% are foreign-owned, 30% are joint ventures, and 23% are Thai-owned. The majority of tier-1 manufacturers (54%) produce parts for automobiles, with 28% making parts for motorcycles, and 18% doing both.
- Tier-2 and tier-3 manufacturers are generally Thai-owned SMEs. These usually have lower levels of investment in research and development and employ lower levels of manufacturing technology than do tier-1 operators and so they are therefore at a disadvantage when competing in the OEM market. As a consequence, players in these tiers tend to occupy a niche as suppliers of raw materials, producers of auto parts and components for tier-1 operators, and/or manufacturers for the REM market. 1,100 tier-2 and tier-3 operators are now active, making parts which may be divided into two groups: (i) ‘genuine’ spare parts, which are produced on order for a vehicle manufacturer and according to their specifications, and (ii) ‘imitated’ spare parts, which are produced outside the standard control of the vehicle manufacturer and which are therefore usually cheaper and of lower quality, meeting demand from the more price-sensitive end of the market.
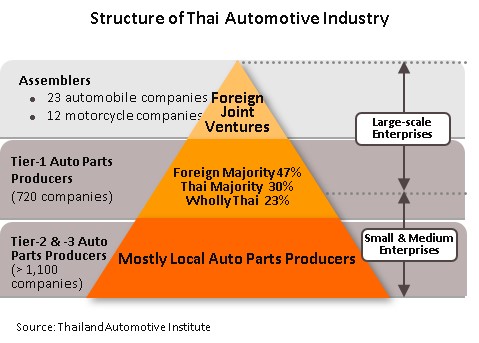
Situation
The auto parts sector typically sees growth in line with that of domestic vehicle production, and in the years 2012 to 2017, the auto parts sector saw varying market conditions as the health of the domestic market (60-65% of sales) went through a period of fluctuating health. However, at the same time, exports have grown steadily as foreign, and especially Japanese, manufacturers invested in or expanded their Thai production facilities, and for many of the major Japanese car companies, Thailand is now the center of production of parts for use in vehicle assembly in other ASEAN countries. Details of recent developments in the sector are given below.
- In 2012 and 2013, the automotive market in Thailand saw very positive conditions and output was raised to high levels as a result of the implementation of the first-car buyer scheme, while motorcycle production also expanded rapidly due to efforts by the government of the time to stimulate the economy in the regions and the subsequent increase in consumer purchasing power. These moves helped to inflate the OEM market, which expanded at historic levels in 2012, pushing growth in the Thai auto parts sector (measured in THB) to 32.0% YoY in 2012 and a further 7.0% YoY in 2013.
- In 2014, measured in THB, income for the auto parts sector shrunk by 11.4% YoY as both the OEM and REM markets weakened. Demand from OEM parts shrank sharply in the year on the ending of the first-car buyer scheme, the impact of the drought on the agricultural sector, the subsequent decline in prices for agricultural products, and the reemergence of domestic political conflicts. These events combined to restrain domestic consumer spending and this then caused sales of automobiles and motorcycles to contract very sharply, falling 33.7% YoY and 15.1% YoY, respectively. At the same time, exports of vehicles saw fluctuating circumstances and overall, economies in export markets remained somewhat soft and this held vehicle exports to only weak levels of growth. The market for replacements and spares (the REM market) also reported only sluggish growth as consumers deferred non-essential spending on vehicles. A further factor working against the market was the youth of the cars bought under the first-car buyer scheme, which had largely not yet clocked up enough mileage to require major spending on parts. Thus, such replacement parts as were required tended to be restricted to more quickly wearing but relatively minor items such as oil and air filters, bulbs, spark plugs, windscreen wipers and brake pads.
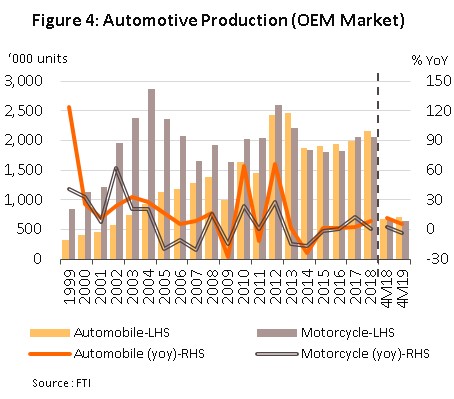
Through 2015 and 2017, domestic demand for auto parts gradually recovered. From 2015, the OEM market began to expand as the total automotive sector returned to growth, while the REM market started to benefit from the steady aging of first-car buyer automobiles; after 3-4 years (though this will depend on use patterns), it usually becomes necessary to start replacing more expensive automobile parts, such as batteries and tires. Income (measured in THB) for the sector thus grew by 4.5% YoY, 7.6% YoY and 3.5% YoY in 2015, 2016, and 2017, respectively (Figure 5).
In 2018, the sector recorded continuing growth and the manufacturing production index (MPI) rose from its 2017 figure of 105.2 to 106.5 (Figure 6).
Domestically, both the OEM and REM markets strengthened on respectively an increase in the number of vehicles assembled in-country and the ever growing size of the national vehicle fleet, while exports also maintained their growth trajectory, helped by the investment in and expansion of plants producing auto parts for export. As such, measured in Thai baht, income for the Thai auto parts sector for 2018 is forecast to have grown by 10-12% YoY, compared to 3.5% YoY growth in 2017. However,
the outlook for 2019 is less positive and in the first part of the year (January to April), the US-China trade war precipitated a slight fall in exports. Details are as follows.
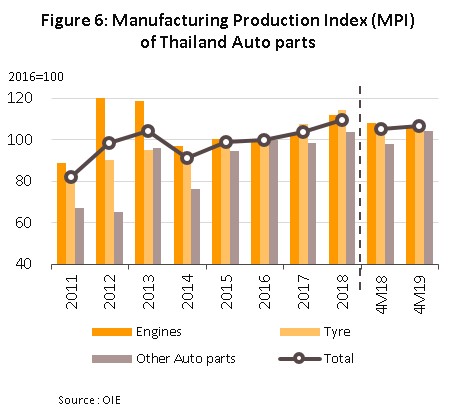
- The domestic market: Demand from the OEM market remained strong through 2018 on the back of rising production by the automotive sector; for the year, auto production rose 9.0% YoY to 2.17 million units, while motorcycle assembly increased by 0.4% YoY to 2.06 million units. However, demand for auto parts is softening in 2019 and for the first four months of the year, growth in production of automobiles and motorcycles slipped to 5.5% YoY (0.71 million units) and -3.6% YoY (0.65 million units), respectively. Meanwhile, the REM market continued to grow thanks to the large and growing number of vehicles registered in Thailand (Table 3), especially the increasing number of those aged 5 years or older. In addition, under the government’s ‘Shop for the Nation’ program[6], it is possible to offset purchases of new tires against personal tax, and this has helped to encourage vehicle owners to change parts. Imports of auto parts to Thailand also rose in 2018 and were up 5.8% YoY to a value of USD 17.51 bn. With a 35% share, Japan was the most important source of imports and these increased in value by 7.1% YoY to USD 6.20 bn. Japan was followed in importance by China[7], which had a 19% share and was the source of imports with a total value of USD 3.32 bn (-4.9% YoY). For the period January to April 2019, imports slowed and rose by just 0.2% YoY to a value of USD 5.67 bn on a softening of growth in the overall production of vehicles.
- Exports: In 2018, exports jumped by 13.7% YoY to a value of USD 21.23 bn but then contracted by 1.7% YoY to USD 6.73 bn in the four-month period January-April 2019 (Table 5). Details are given below
- Engines: In 2018, engine parts jumped in export value by 24.37% YoY to USD 5.37 bn, export of engines continued to increase since 2016, following the expansion of the engine production capacity for the export of car manufacturers in the previous period. Thus, Siam Toyota has expanded the company’s diesel-engine production facilities, Honda’s parts factories manufacture 1.8-liter petrol engines and 1.5-liter VTEC turbo engines, and Mazda Powertrain Manufacturing has invested in increasing its Thailand-based production of 1.3- and 2-liter SkyActiv engines. The majority of this production goes to assembly plants run by parent companies, either in Japan or elsewhere in the ASEAN region, which together account for 43.2% of the value of exports of engines from Thailand, but as with some other product groups, the beginning of 2019 has signaled a worsening of conditions and in January to April, the value of exports of engines shrank by 16.9% YoY to USD 1.56 bn. This was caused by a combination of a general slowing of automobile production worldwide, the fact that the industry is in a period of transition from internal combustion engine-powered to electric-powered vehicles, and comparison with a high baseline in the previous year.
- Tires: Exports of tires rose 11.5% YoY to a value of USD 5.11 bn. This segment benefited from the ongoing investment by Chinese operators in export-oriented tire production facilities in Thailand[8]. Examples of these include Huayi Group (manufacturing tires for trucks and larger buses under the brands ‘Double Coin’ and ‘Strong Man’) and Dadi Group (producing truck, bus and automobile tires under the ‘Shenzhou’ brand), which began manufacturing and exporting tires in 2017 and 2018, respectively, and which are overwhelmingly producing for markets outside Thailand (over 95% of output is bound for export). The main export markets are in fact the United States (42% of all exports of Thai tires by value), the ASEAN region (16%), and the European Union (9%). In January to April 2019, exports continued to rise, increasing 13.1% YoY to a value of USD 1.78 bn, although growth has slowed relative to the same period a year earlier.
- Other auto parts: These can be subdivided into two further groups: (i) In 2018, exports of other parts for automobiles (e.g. complete knocked-down units (CKDs), gearboxes, braking systems, airbags, drive-shafts, chassis, etc.) had a combined value of USD 9.99 bn (10.5% YoY) but in January to April 2019, the value of these exports slipped 0.6% YoY to USD 3.13 bn. (ii) At the same time, exports of other motorcycle parts (e.g. complete knocked-down units (CKDs), wheels, brake systems, saddle, pedals, etc.) rose in value by 4.3% YoY to USD 0.77 bn. In the first four months of 2019, exports rose by another 4.4% YoY to USD 0.26 bn, though this represented a decline in the growth rate relative to the same period in 2018. The ASEAN zone is the main target for exports of other auto parts[9], taking 30% by value of all exports of other auto parts from Thailand, with these going to Vietnam, Malaysia and Indonesia in particular. These exports had a value of USD 3.2 bn in 2018 (6.4% YoY) and USD 1.03 bn in January-April 2019 (-1.3% YoY). Exports to Japan accounted for a further 13% of exports of these parts and in 2018 and the first 4 months of 2019, sales to Japan generated receipts of USD 1.37 bn (21.5% YoY) and USD 0.46 bn (9.4% YoY), respectively.
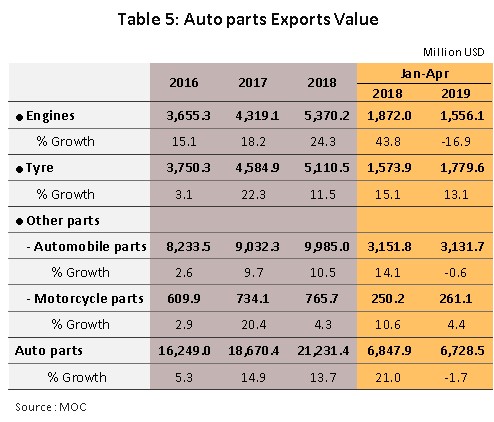
Outlook
Between 2019 and 2021, the auto parts sector is forecast to see growth in income (considered in Thai baht) of 3-5% per year. Demand will be supported by growth in both the OEM (domestic and foreign) and REM markets.
The value of auto parts distributed to the domestic market is expected to grow by 0-3% YoY in 2019 and then by 2-5% in each of 2020 and 2021, which will be in step with growth in the market for parts for use in vehicle assembly, or the OEM market, (Figure 8). Krungsri Research forecasts that growth in production by the auto sector will be flat or decline slightly in 2019, when flat/negative growth of 0% to -2% YoY is expected on the back of a combination of a slowing of the world economy, weaker purchasing power in the agricultural sector as the effects of the drought are felt, and comparison with a high baseline in 2018. For 2020 and 2021, growth is forecast to pick up and will average 0-2% per year on an expected improvement in the domestic economy and, now that they are 6-7 years old, the increasing need to replace vehicles bought under the first-car buyer scheme, while manufacturers that have received investment support from the BOI will also need to push through increased production of eco-cars. Motorcycle assembly is forecast to grow at the slightly higher rates of 2-4% YoY, 0-2% YoY and 0-2% YoY in 2019, 2020 and 2021, respectively. Here, output will be boosted by government help for low-income earners through its welfare schemes, the ‘Rak p’Win’ program (which aims to provide financial assistance to motorcycle taxi drivers[10]) and the increasing output of ‘big bikes’ following the decision by leading global manufacturers to set up export-oriented production facilities in Thailand. The market for spares and replacements (i.e. the REM market) will also continue to grow over the next 3 years as the number of vehicles on Thai roads over 5-years old continues to rise. Demand for replacement parts is largely determined by age and mileage so these older vehicles and especially those bought during the first-car buyer scheme, which are now ageing over 7 years, are a particularly strong contributor to the REM market. As described above, the ‘Shop for the Nation’ scheme has also allowed buyers of new tires to offset the cost of these against their tax payments in the 2018 and 2019 tax years.
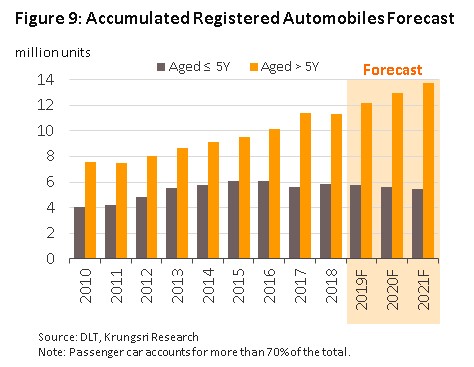
The export market is forecast to see stable growth in line with trading partners’ economic slowdown. The increasing tendency of foreign players to invest in production capacity in Thailand, especially Japanese companies, which have the necessary finances and technology, and which are in addition members of commercial groups that are connected to global automotive production networks will help to raise the quality and level of production technology deployed to international levels, and so it will be possible to progressively increase exports. However, there are 1,100 Thai operators in the sector and the majority of these are tier-2 and tier-3 producers, manufacturing to meet demand from the REM market. These players will face higher levels of risk as foreign-owned manufacturers, especially Japanese SMEs, invest in production capacity in Thailand and so compete with Thai producers in the REM market in larger numbers.
However, some fear that over the long-term, Thai auto parts manufacturers may suffer under the impact of government policies to encourage investment in the production of hybrid and battery electric vehicles. The government has in fact established a target of having 1.2 million electric vehicles on the road by 2036. But Krungsri Research’s evaluation of the situation is that for the early stage of EVs’ development, the domestic market for electric vehicles will grow only slowly and it will remain dominated by hybrid electric vehicles (HEVs) and plug-in hybrid electric vehicles (PHEVs) because these vehicles use the standard parts for internal combustion engines (ICEs) alongside their battery-powered components, for the period 2019-2021 OEM auto parts manufacturers will not be strongly affected by these developments as the market for pure battery electric vehicles (BEVs) will remain a niche market until such time as their price becomes competitive with ICE-powered vehicles and it is expected that it will be 5-7 years until this happens and BEVs become more popular in Thailand; it will not be until then that the development of lithium-ion batteries will be sufficient to make their use attractive[11], although the trend is very much in the right direction and whereas in 2010, lithium-ion batteries cost USD 1,200/kWh but by 2018, this had fallen to USD 175/kWh. Because BEVs use many fewer parts than ICE-powered vehicles (the typical BEV drivetrain uses around 20 parts compared to over 2,000 in that of an ICE vehicle). In the next 5-7 years, it will be a major turning point for Thai auto parts manufacturers, which in the past have focused strongly on developing the supply chain for internal combustion engines. As BEVs come to take on a more important place in the market, the battery itself will become the major component in auto assembly, as opposed to the engine, and this is expected to consume up to 30% of all production costs for BEVs
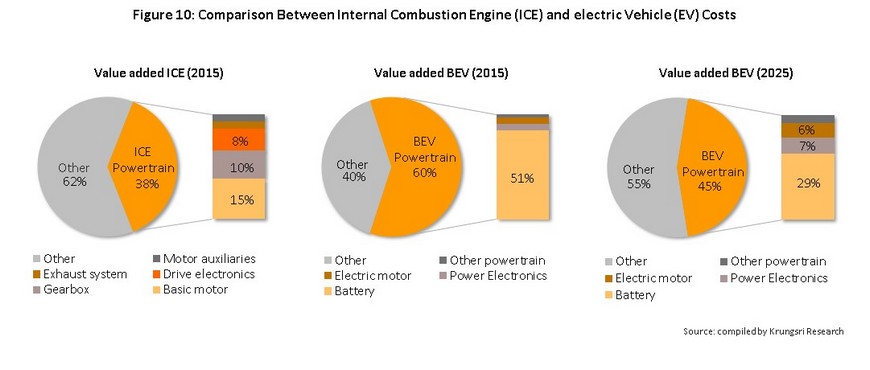
Recently, investment in the manufacturing of parts for electric vehicles has indeed begun to be seen in Thailand, in particular of batteries, examples of which include Toyota’s opening of a nickel metal hydride battery factory and BMW’s plans to invest in developing lithium ion batteries. Beyond this, it is clear that demand from the OEM market for parts such as engines, radiators, exhaust systems, fuel distribution systems, petrol tanks, ignition systems, and gears will see significantly reduced demand if BEVs become popular, although this decline will be offset somewhat by continuing demand for other components, including the suspension, bodywork, lighting, and interior fittings, which will still be needed regardless of the vehicle’s engine. Demand for replacement parts will also decline because in BEVs some systems are controlled by electronic means that extend the age of components and so they will need to be replaced less frequently than are their equivalents in automobiles powered by internal combustion engines. Examples of these include tires and brake pads. In addition, improving safety thanks to computer-assisted driving systems may reduce the accident rate and this too would lower demand for repairs and replacement parts in the REM market.
Krungsri Research view
In the three years from 2019 to 2021, income for manufacturers of auto parts and tires is expected to grow, though not at particularly high rates and it will move in line with growth in the domestic market for OEM and REM parts. At the same time, exports will remain flat or will see only limited increases in sales in line with the economic outlook for trade partners, while distributors of spares and accessories will see their turnover strengthen in step with the increasing number of vehicles registered in Thailand.
- Manufacturers of parts and spares: Operators in this group are forecast to see turnover remain at a good level on the back of growing domestic demand. Demand in the domestic OEM market will strengthen in line with rising automobile production, the REM market will continue to benefit from the constantly growing size of the total national vehicle fleet, and exports will also gain from overseas manufacturers establishing factories in Thailand from which to export parts to the rest of the region, although risks will exist for players in this group from the continuing tensions between the US and China over trade that may have negative impacts on the economies of Thailand’s trade partners.
-
Tire manufacturers: Producers of tires will likewise see turnover remain at a good level thanks to rubber prices that have stabilized at a low level and from growing demand from both the OEM and REM markets. This will be because of growing domestic production of vehicles and for the latter, it will be due to the aging of automobiles bought under the first-car buyer scheme and their increasing need for replacement tires and the effects of the ‘Shop for the Nation’ scheme, which will have helped to boost demand for tires in 2019. Exports are also expected to rise on the move by international tire manufacturers to open export-oriented factories in Thailand, although these operators may also be affected by the US-China trade conflict.
- Distributors of spares and accessories: Income for players in this segment will grow as the OEM and REM markets expand but risks exist from mismanaging stock, while competition in the segment is fairly intense.
- Wholesalers and retailers of new parts and accessories: It is forecast that demand for parts and spares and for decorative accessories which have a short lifespan will strengthen as sales of automobiles rise. Similarly, the growing numbers of vehicles on the road will also help to support increased demand for parts for replacement and repair. However, the large number of players in this segment means that competition on price can be strong and this will put downward pressure on profits.
- Wholesalers and retailers of second-hand parts and accessories: Operators in this group will see growth proceed in line with growth in the size of the vehicle fleet, though particularly of that part of the national fleet aged over five years because these vehicles require more frequent repairs and replacement of parts and some owners of these will use second-hand parts to save on expenses. However, profits may be held back by a business model that requires operators to invest in carrying a wide range of stock, which in turn opens them up to the risk of holding outdated items and attendant problems with stock management.
[1] The first period of the development of the automobile industry in Thailand involved the import of ‘complete knocked-down’ (CKD) units from foreign manufacturers or their subsidiaries. These were then assembled in-country as ‘complete built-up’ (CBU) vehicles.
[2] Under WTO rules, member states (including Thailand) are prohibited from specifying the proportion of locally-sourced materials to be used by manufacturers and so from 1st January 2000, local content requirements have no longer been in effect in Thailand.
[3] Engines production is composed of over 2,000 parts.
[4] The government has specified limits on the periods during which investment support applications may be submitted for the manufacture of EVs and EV parts. Thus, applications for hybrid electric vehicles (HEVs) had to be submitted no later than 31st December 2017 and five companies (Toyota, Honda, Mazda, Nissan and Suzuki) did so. For plug-in hybrid electric vehicles (PHEVs) and battery electric vehicles (BEVs), applications close on 31st December 2018 submissions made for these two categories of vehicles had come from Mercedes-Benz, BMW, MG, FOMM, Mine, Toyota and Audi. In addition, applications for investment privilege for the production of batteries for use in EVs have come from Toyota, Honda, Mercedes-Benz, BMW and Global Power Synergy.
[5] Source: Report of ADB Institute on the topic of “Thailand’s Economic Integration with Neighboring Countries and Possible Connectivity with South Asia”
[6] The cabinet agreed to the ‘Shop for the Nation’ program on December 4, 2018 and under this scheme, individuals are able to set the cost of purchases of tires, books and OTOP products made between December 15, 2018 and January 16, 2019 against their personal tax liabilities. The deductions can be made in two tax years (according to when the purchases were made) but over the two years, purchases cannot have a combined value of more than THB 15,000. Individuals reclaiming this tax need to submit a full tax invoice together with a coupon for the program. Moreover, coupons for tax deduction have also been distributed to tire manufacturers that purchased their raw materials (i.e. their rubber) from the Rubber Authority of Thailand between December 1, 2018 and January 16, 2019.
[7] Thailand’s imports of Chinese-made auto parts increased sharply in the past decade, rising from 5.3% (by value) of imports in 2007 to 18.9% in 2017.
[8] Chinese tire manufacturers that have invested in Thai production include Hang Zhou Zhong Ce Rubber, Shandong Linglong Tire, Sentury Tire and Huayi Group.
[9] Thailand remains a major ASEAN auto parts production center for Japanese car manufacturers, with parts exported to production facilities for use in vehicle assembly in neighboring countries. This is because of the ‘Thailand-Plus-One’ policy operated by large Japanese producers, which has led Japanese companies to expand investment in a wider range of ASEAN countries, in particular countries such as Indonesia (now home to automobile production facilities) and Vietnam (motorcycle manufacturing) that have large domestic markets.
[10] Additional details are available in the Krungsri Research’s 2019- 2021 Industry Outlook for the automobile sector and for motorcycle sector.
[11] With a budget allocation of THB 180 m from funds for promoting energy conservation, the Ministry of Energy and the Vidyasirimedhi Institute of Science and Technology (VISTEC) are jointly developing batteries for use in electric vehicles and looking for ways of storing energy generated from solar power. As part of this work, the partnership has patented a lithium-sulfur battery that has a capacity 3-5 times higher that of lithium-ion batteries but which is also lighter and can propel a car for up to 800 kilometers on a single charge, compared to 400-500 kilometers for a lithium-ion battery. Given that lithium is about 200 times more expensive than sulfur, the VISTEC battery is also cheaper but unfortunately, it has a lifespan of only 2-3 years, compared to an average lifespan of 10 years for a lithium-ion battery. VISTEC hopes to begin commercial production of their new batteries in 2020-2021.