Overview
Steel is a basic metal used as a crucial input into the production process of many consuming goods which are important to the growth and health of the economy, including construction, vehicles, electrical appliances, and packaging sectors. In general terms, the steel sector can be split into three parts.
- Upstream Steel Production
The first stage of steel supply chain involves the production of raw steel. Iron ore is ‘dressed’ to improve its purity by being crushed, processed, smelted. After the processing, ‘pure iron’ is extracted and is used as an input in midstream and downstream steel production. This smelted iron is classified into two types; pig iron is processed in a liquid form, and sponge iron is processed as a solid. Countries which do not have a domestic source of sufficiently high-quality iron ore may instead use scrap as an input in their steel production. In the case of steel-melting mill in Thailand, due to a combination of worries about the potential impacts on the environment and the health of nearby communities, and the high costs of investment which make breaking-even difficult, there is no domestic upstream production of steel. Instead, iron is imported in the form of pig iron or billet for further processing.
- Midstream Steel Production
Midstream production involves melting iron (pig iron, sponge iron, or scrap) at temperatures of around 1,600 °C and mixing this with a variety of other additives such as carbon or chromium. This alters the chemical properties of the final steel and thus makes it suitable for a particular end-use. These additives also help to oxidize impurities, which are then removed from the smelted product as a waste product known as ‘slag’, leaving behind steel. These semi-finished steel products will be in one of the three forms of bloom beam, billet, and slab, which differ in their shape and density. Generally, Thai manufacturers tend to import billet and slab for use in producing a wide range of finished products.
- Downstream Steel Production
Downstream processing involves taking intermediate products and transforming them into finished steel products. This entails the use of processes such as hot rolling, cold rolling, coating, and forming (figure 1), and molding to produce hot and cold rolled sheet steel, coated steel sheets, rods and rebar, and structural steel (such as C-light lip channel [1] and H-beam[2]). Thai manufacturers of finished products mostly use semi-finished steel products which are smelted from scrap as input due to low production cost. These structural steel products are used by related industries in the construction, and general packaging sectors. However, some manufacturers have to import semi-finished steel products made from iron for use in producing high-quality finished products or high-grade steel which will be used in industries complex production structure such as vehicles, electrical appliances and packaging for special purpose (e.g. petrochemical products).
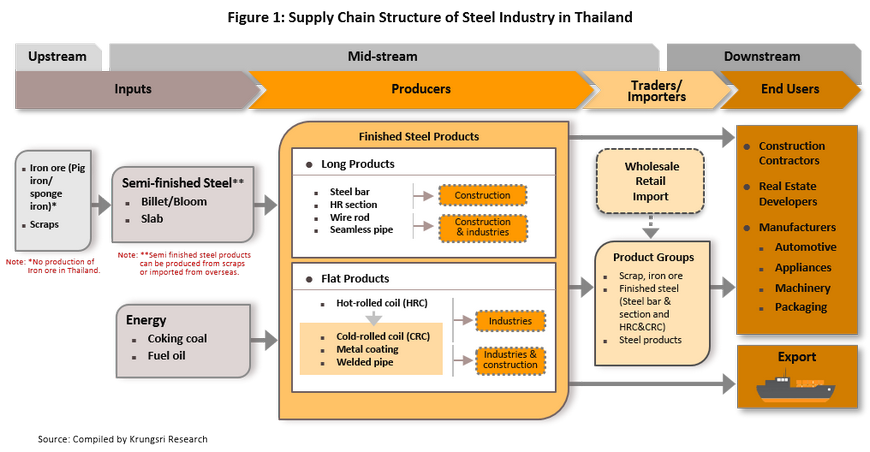
Type of semi-finished steel can be split into two main groups:
- Long products are semi-finished large and long steel such as rebar and wire. Producers of long products may be divided into those which have access to a furnace and those which do not, with the latter group having to face higher costs. This type is generally used in construction industry.
- Flat products are flat shape produced in intermediate stage. These include both hot and cold rolled steel products such as plates and coils. Flat products are used in manufacturing auto parts, electronic appliances and machineries.
In terms of consumption, demand for steel is dominated by the construction sector, which takes 57% of consumption nationwide (and are mostly for rebar, structural steel and nails, screws, and bolts), and it is followed in importance by the manufacture of vehicles (18%), machinery (11%), electrical appliances (9%), packaging (4%), and other uses (1%) (Figure 2). During the period 2013-2018, demand for steel[3] in Thailand averaged 18 million tonnes per year. Meanwhile, steel production averaged only 7 million tonnes per year (midstream and downstream production) (Figure 3). Therefore, great amount of steel imports are needed.
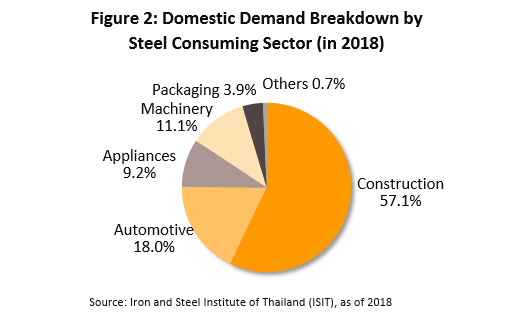
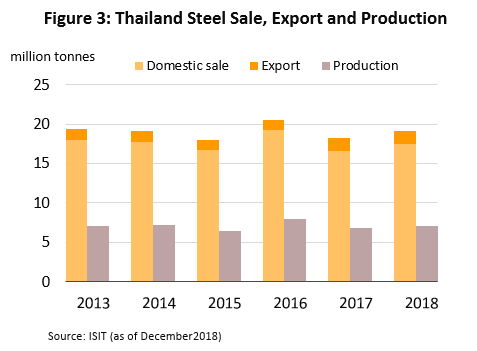

Thai steel products are consumed more domestically than internationally. Domestic market and exports are at a ratio of 91:9 (Figure 3). Currently, Thailand produces more long steel products than flat ones at 60:40. Long products (deformed bar and structural steel) are mainly used in construction business. Flat products, on the other hand, tend to be used in sectors which are dominated by foreign-owned companies that have established production facilities in Thailand. This includes sectors such as motor vehicle and electrical appliance manufacturing. Players in these industries often use high-tech manufacturing processes which require special-grade sheet metal produced from pig iron and so for use in their Thai factories, steel slab and related products (such as hot and cold rolled steel or coated panels) need to be imported.
The cost structure of the sector is such that raw materials (whether this is scrap or steel bar) account for 66% of total costs[4] . Energy and fuel costs take another 13%, wages 7%, and the remaining 14% go to other costs (Figure 5).
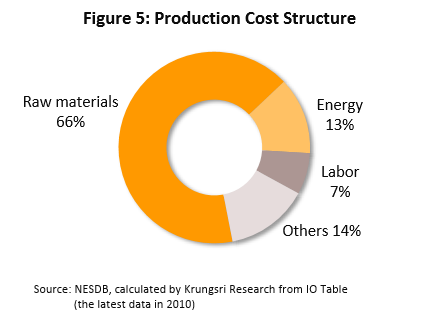
Players in the Thai steel sector are mostly small- and medium-sized enterprises (60% of the total). To reduce risk and to benefit from economies of scale, large producers typically combine steel production and the selling of billet and slab, along with related intermediate products. Operators in the steel sector can be divided into two main groups:
- Steel manufacturers can be divided by group in terms of type of production process: (i) manufacturers of slab or billet, most of which are large-sized operators which will also produce finished goods; (ii) manufacturers of rebar and structural steel; (iii) manufacturers of hot or cold rolled steel; or (iv) manufacturers of steel piping. Overall, though, the output of most Thai producers is of long products. Manufactures which have their own furnace are able to use scrap metal as an input. This helps to reduce expenditure on raw materials, which for those producers equipped with a furnace average 47.1% of all costs. Those who lack a furnace must instead purchase their raw materials and this leads to significantly higher raw material costs (81.3% on average)[5]. More recently, manufacturers have also faced problems with competition from cheap imports and the result of this has been that some domestic businesses have ceased trading.
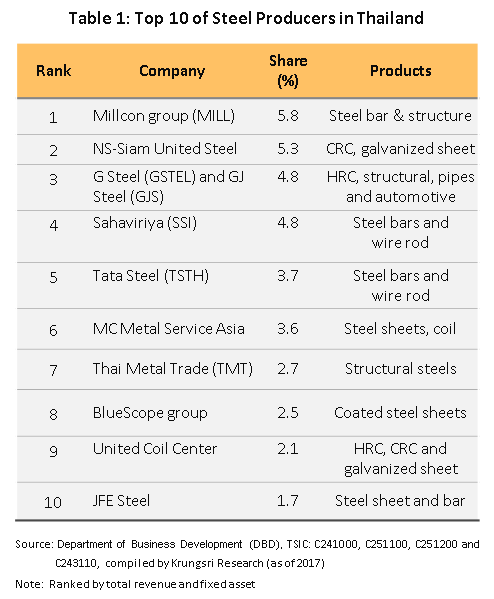
- Steel traders and importers are divided into three subgroups: (i) traders in scrap metal and ore (iron and other metals); (ii) traders in finished steels, such as rebar and hot and cold rolled steel; and (iii) traders in steel products such as construction hardware, the largest of these groups. Thai importers of steel usually source goods in China, particularly for steel products used in construction, which, because of China’s huge output and the consequent economies of scale, are cheaper than Thai goods, though they are also of inferior quality. However, in 2017, those Chinese factories which produce low-quality steel products have been closed by government policy to control pollution problems.
Thailand is a net importer of steel. Imports and exports of steel are described in detail below.
- Of total 12 million tonnes of imported steel, are intermediate products mostly for finished goods processing.
During 2013-2017, Thailand’s imports of long products and flat products averaged 3.0 and 8.9 million tonnes per year, respectively (source: ISIT). The five most important categories of imports are billet and slab, hot and cold rolled steel, coated steel, rebar and structural steel, and scrap. China and Japan are the leading exporters of steel products to Thailand, with Chinese goods usually being long products such as rebar. This is because Chinese imports are cheaper than their Thai competitors. Unlike long products, flat steel products such as hot and cold rolled steel are usually imported from Japan, since consumers of these products (e.g. vehicle and parts manufacturers) are themselves usually owned by Japanese companies who specify that only high-grade steel be used and most Thai manufacturers of flat steel products are unable to meet these standards.
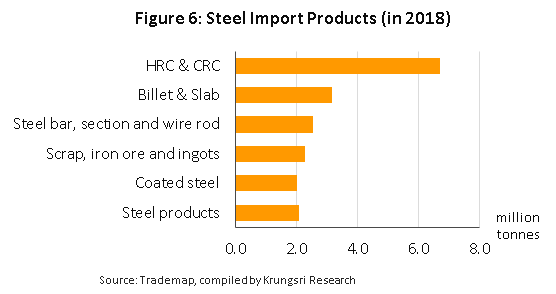
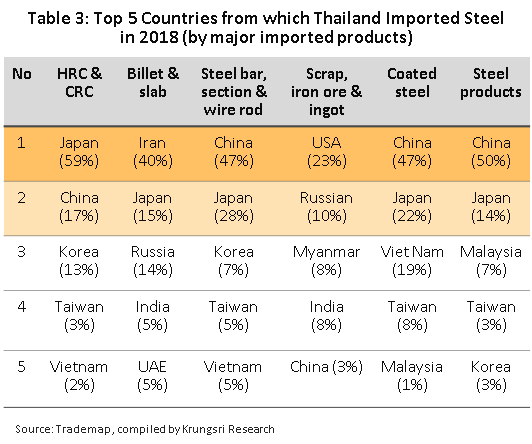
- Exports of steel around 1.5 million tonnes…focus on the neighbor countries as investment in infrastructure picks up.
During 2013—2017, Thailand’s exports of long products and flat products averaged 0.9 and 0.5 million tonnes per year, respectively (source: ISIT). The five most important categories of steel exports are rebar and structural steel, scrap, steel piping, pre-engineered structures and parts, and hot and cold rolled steel. The largest export area is the CLM zone, which consumes Thai rebar and structural steel in its infrastructure and property sectors. In addition, due to the quality of products, both Australia and Japan purchase steel piping and pre-engineered structures (including, for example, buildings and bridges) from Thailand.
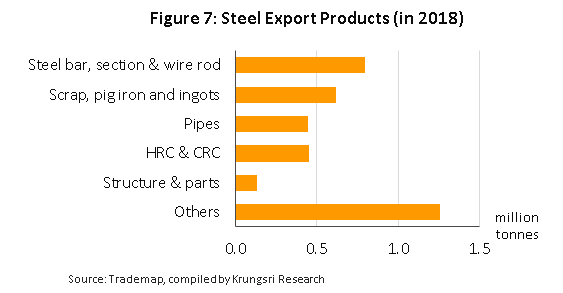
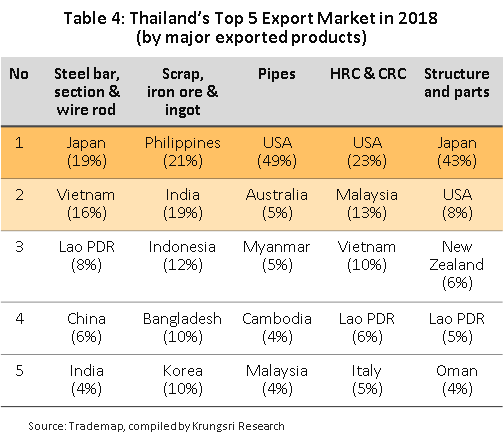
Situation
The global steel industry: In 2018, the effects of US-China trade conflicts tended to cause production and consumption of steel to slow worldwide.
In 2018, global demand for steel6/ rose 3.9% YoY to 1.74 bn tonnes, a decline on the 5.0% YoY growth recorded in 2017. This slowing of the market was driven by the decision by American authorities to raise duties on imports of steel from a large number of countries and, related to this, the emergence of the US-China trade dispute. Despite these headwinds, the market still saw growth, though, and this was thanks to: (i) the roll out of infrastructure construction projects in many countries; (ii) the recovery of real estate markets; and (iii) growth in manufacturing sectors that are downstream consumers of the steel industry (e.g. automotive assembly), which strengthened on better economic conditions and rising confidence among private sector investors. In the year, exports also rose, increasing by 8.7% to a value of USD 720 bn on the improving construction and production in many countries (Figure 10); the three biggest exporters were China, Germany and Japan, which together account for 30% of the value of all steel exports worldwide.
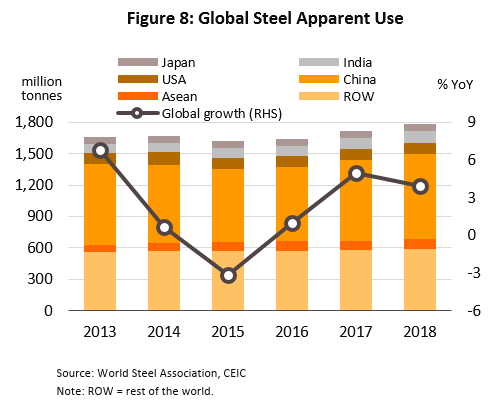
Global steel production totaled 1,809 million tonnes in 2018. This represented a rise of 4.6%, a cooling global economy caused the rate of increase to slip slightly from 2017’s 6.3% growth. However, strengthening demand in individual countries helped to sustain an 8.1% rise in imports worldwide, with the biggest importers being respectively the United States, Germany and China, which combined had a 23% share of world imports by value. (Imports and exports of steel to and from China are of different types, and the majority of imports are of finished downstream products that require the use of high-tech production processes).

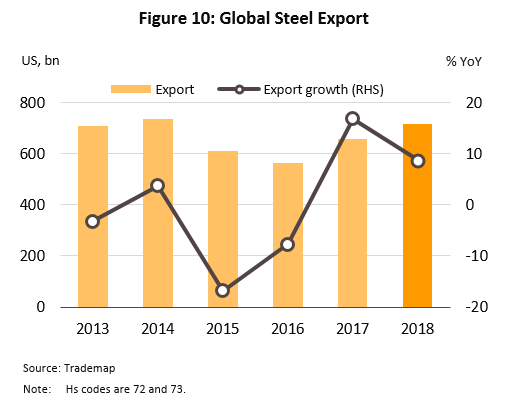
Across 2018 as a whole, the prices of steel products on world markets increased, influenced by a combination of rising demand and higher production costs. Thus, prices for steel bar, hot rolled steel and cold rolled steel increased by 12.7%, 10.8% and 7.2%, respectively (Figure 11) but at the end of 2018, this trend reversed and prices softened on a worsening outlook for the Chinese real estate sector (China is the world’s biggest producer of steel), and this fall in prices is expected to continue through the remainder of 2019.
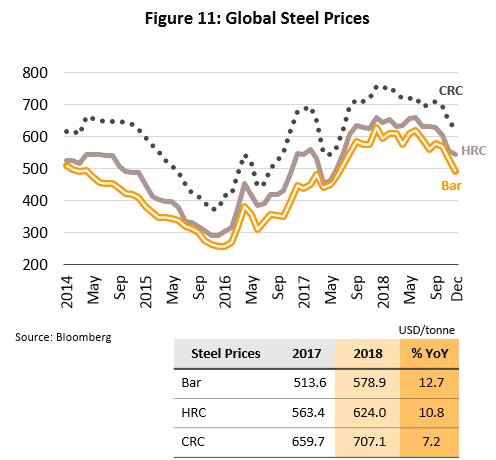
The domestic steel industry: Output strengthened on rising demand from domestic and export markets (Figure 12).
Following a weakening in 2017, domestic consumption of steel returned to growth of 4.8% (or a total of 17.5 million tonnes) in 2018 on greater demand for use in construction of government infrastructure projects and private sector real estate developments, while within the CLMV countries, higher levels of industrial production and government spending on infrastructure boosted exports from Thailand by 10.3% to 1.7 million tonnes. Higher demand from domestic and export markets then lifted 2018 steel production to 7.1 million tonnes (up 3.4%) (Figure 12). Imports of steel and of finished steel goods also strengthened in the year, rising by 6.4%, and imports in fact comprise a full 60% of all steel products consumed on the Thai market.
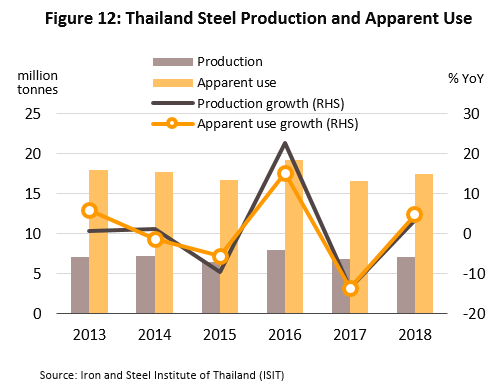
For domestic steel prices, across all product groups, steel prices rose by an average of 7% in 2018. Steel bar prices rose by 8% on an expanding construction sector, while for hot and cold rolled steel, the rises were 7% and 6%, respectively (ISIT, 2018). These latter increases were caused by (i) the higher cost of imported steel and (ii) a 9% increase in output by the auto sector, a major consumer of rolled steel products (source: The Thai Automotive Industry Association, 2018).
.
The situation of the steel sector in 2018, analyzed by product type, is given below.
- Long products: Domestic demand improved in 2018 but production contracted only slightly.
- Demand rose by 2.2% to 5.6 million tonnes in 2018 (Figure 14). 60% of total demand for long steel products was for steel bar and section and demand for these goods rose by 1.9% on the expansion of construction work nationwide, both for the roll out of public sector infrastructure and for use by private sector real estate developers, especially for the construction of residential properties. (For further details please see the report at 2019-2021 Industry Outlook: Construction Contractor). Meanwhile, exports rose at the much higher rate of 13%[7], increasing to 1.1 million tonnes in 2018 (from the 0.97 million tonnes exported the year earlier) due to higher demand in particular within the ASEAN zone which recorded higher rates of infrastructure construction and the subsequent greater need for long steel products.
- However, output moved in the opposite direction and shrank by 1.2% for 2018 as a result of (i) high levels of stock holding and (ii) in the second half of 2018, falling prices for imports of steel that made imports less expensive than domestically-produced goods and this naturally prompted downstream consumers to switch to buying a greater quantity of these cheaper imports.
- Steel imports in 2018 increased by 11.7% to 2.9 million tonnes in response to 1) the increase in import duties by the American authorities that caused overseas producers of steel products, such as those in China and Vietnam to have increasingly attempted to sell into the Thai market 2) increased investment in infrastructure projects that require higher quality construction steel, for example, for use in rails for new twin-track railway lines.
- For a whole 2019, stronger domestic demand lifted prices for steel bar by 8.3% YoY to an average of THB 20,600/tonne, the highest for three years (Figure 19), but at the end of 2018, the falling world steel prices had an effect on domestic prices.
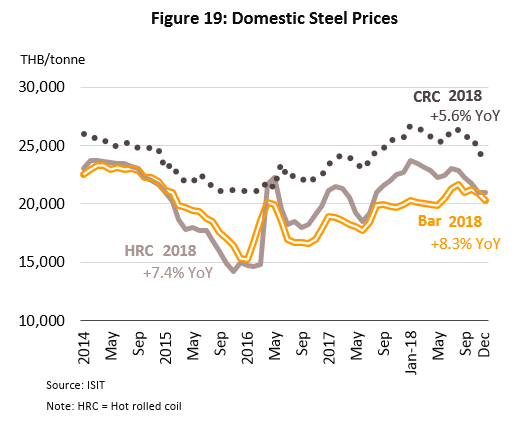
- Flat steel products: Production rose in step with strengthening domestic demand
- Demand rose 6.1% to 11.7 million tonnes in 2018 following a shrinkage of 5.9% in 2017 (Figure 15). Supported by rising demand from automobile and construction sector which strengthened solidly in 2018 (Consumption of flat steel products is split 55:45[8] between industrial users and construction). Export grew by 3.6% (to 660,000 tonnes), lower than 32.9% recorded in 2017 due to the imposition of tariffs by the United States on imports of steel from a number of countries, a move that caused manufacturers in Thai export markets that are downstream consumers of steel goods (e.g. auto assembly) to lose exports to the US market and so they then had to cut back on orders of mid-stream and downstream steel products from Thailand. In addition, Thailand also felt the impacts of US import duties directly and exports to the United States of flat steel products, and especially of hot rolled steel, slid through 2018

In response to the continuing growth of demand on domestic and export markets,
production of flat steel goods rose by 9.5% to 3.2 million tonnes, while imports increased by 4.8% (Figure 16), due mainly to strengthening demand from the automotive sector and the fact that for some product groups, imports undercut Thai goods on price.
Through 2018, prices for hot and cold rolled steel rose by, respectively, 7.4% and 5.6% to THB 22,500/tonne and THB 25,700/tonne (Figure 19) on greater domestic demand but prices softened again at the end of 2018 as global production of flat or rolled steel products increased and prices on world markets slid in consequence.
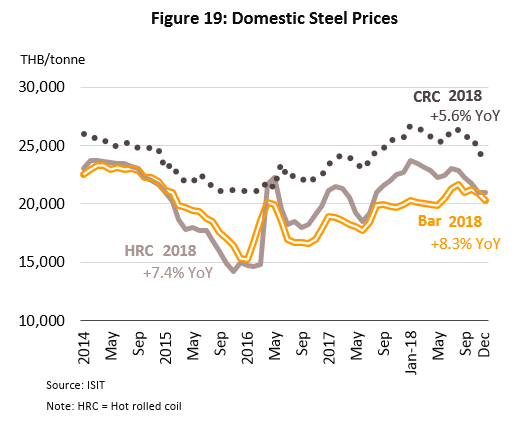
- Production costs (mid-stream and downstream of steel products): Production costs increased in 2018, pushed up by higher costs for scrap metal and inputs of imported raw materials.
-
Raw materials (66% share in total production costs): Most Thai steel producers use scrap metal as their main source of steel but in 2018, higher exports of scrap caused a supply shortage on the domestic market and this pushed up prices by 18.4% to THB 12,204/tonne.
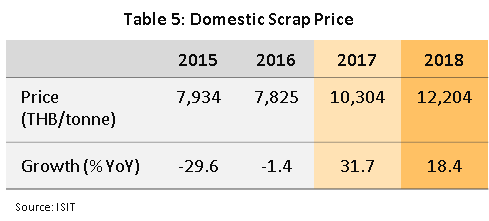
-
- Fuel and energy costs (13% share, with oil and coal contributing 46% in total fuel and energy costs): Oil prices rose by 28% in 2018 to an average price across the year of USD 65/bbl. Prices were lifted by the cut in production by OPEC and non-OPEC members (e.g. Russia), together with fears over the loss of Iranian oil in the wake of the imposition of American sanctions against the country. Coal prices also rose, up 22% to USD 108/tonne (Bloomberg) on cuts in output by China, the world’s biggest producer.
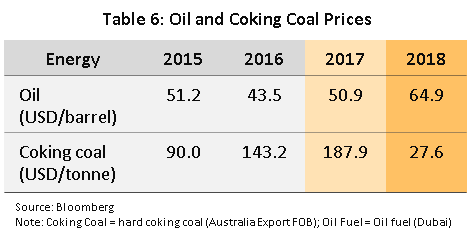
Turnover for steel manufacturers and distributors in 2018 (from an evaluation of the business performances of companies registered on the Thai stock exchange): Steel manufactures saw income rose 20% for manufacturers on increases in both domestic demand and prices but despite this, profit rates declined steadily to 4% (Figure 21) due to: (i) strong competition on price in the second half of 2018 from cheaper imports; and (ii) production costs that rose through 2018 on higher prices for domestically sourced scrap metal and for imports of steel slab and rolled coil. Traders and distributors saw their average earnings fell by 4% due to the rising cost of domestically produced steel, which caused buyers to source lower-priced imports instead. Profit rates then fell to 5%, in line with those of manufactures.
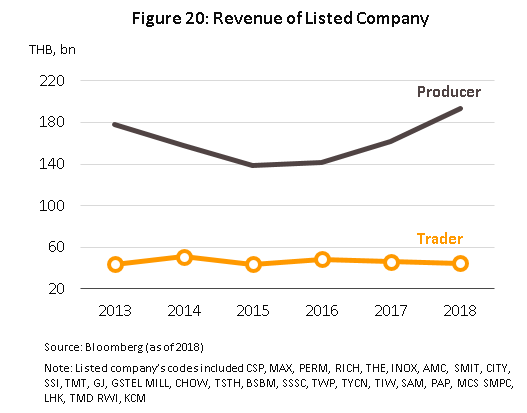
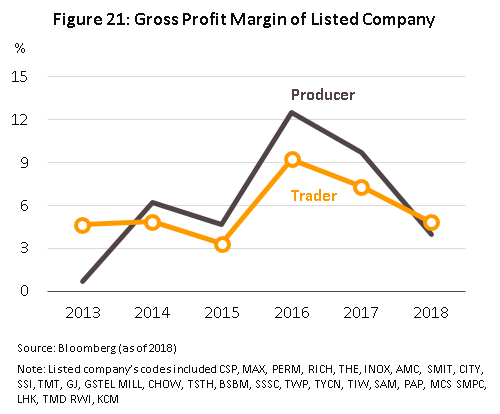
Outlook
The global steel industry: The erection of barriers to trade by the US government and an oversupply of production capacity pose challenges for the sector.
In 2019, demand for steel will tend to remain flat as the world economy slows but in 2020 and 2021, growth in demand should pick up again (Figure 22) to hit around 1,900 million tonnes on an expansion in infrastructure construction and the recovery of real estate and manufacturing worldwide. The biggest consumers of steel will be China, the United States and India, with the last likely to be a source of increasing demand following the government’s moves to make the country a regional center for the assembly of small vehicles.
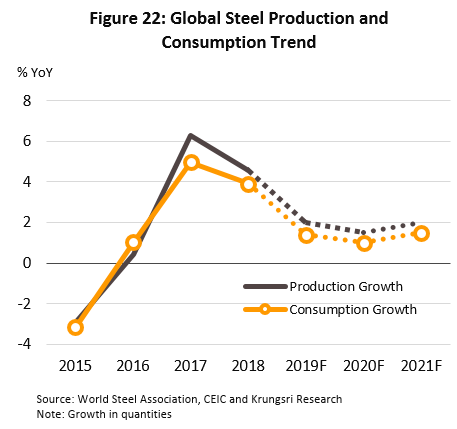
Global steel production in the period 2019 to 2021 is expected to expand in line with demand on world markets and the major steel-producing countries are all planning to expand their production capacity. Thus, China is investing in new steel foundries, both in China itself and in other countries, while India and the United States are planning to increase their output of steel and to use this to support domestic construction and manufacturing production. For its part, Japan, which is currently the world’s third biggest producer of steel after India, (India became the world’s second most important producer of steel in 2018) is likely to see its output stabilize in step with the probable outlook for domestic demand. Krungsri Research therefore expects that problems with the oversupply of steel to world markets will not be resolved in the near future, and although global stockholdings of steel fell by 2.7% in 2018 (Figure 23), within China, the world’s foremost producer of steel, stockholding remains high.
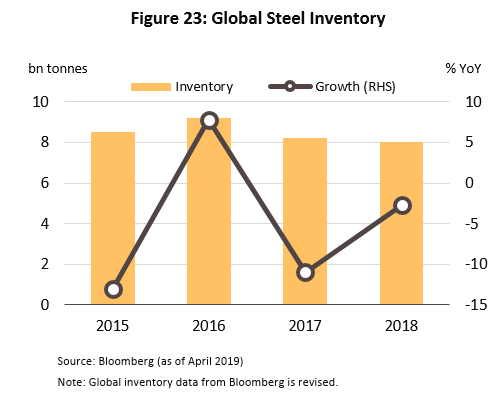
The Thai steel industry: The domestic market for steel will grow in step with growth in related industries and in the construction sector, and this will help to lift output.
Demand for steel across all product groups is expected to stay flat or to increase by only a small amount in 2019. This is because some private sector players postponed investment decisions in the first half of the year, waiting until after the national election and the shape of the future government and its policies became clearer. However, now that the new government is in place, the expectation is that spending on national infrastructure, especially on new large-scale projects, will pick up again in the second half of the year. In 2020 and 2021, domestic demand for steel will strengthen (Figure 24) due to: (i) expected strong growth in the construction sector, driven by the previously mentioned government infrastructure spending and real estate developments in high-potential areas, including the Eastern Economic Corridor and alongside the new mass transit lines in the Bangkok Metropolitan Region; and (ii) expansion in industries downstream from the steel sector (e.g. vehicle assembly and electrical appliances) that will be caused by growing demand in domestic and export markets.
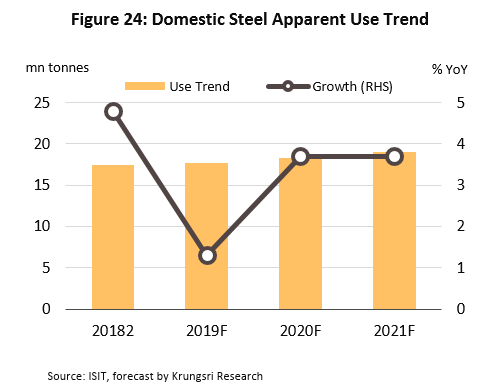
Exports of steel (which take 10% of domestic production) are forecast to fall (Figure 25). American efforts to reduce imports and so protect its own steel industry will lead to a decline in Thai exports to the United States, one of Thailand’s major trade partners[9], while exports to other markets that are similarly affected by the imposition of American tariffs will also slip.
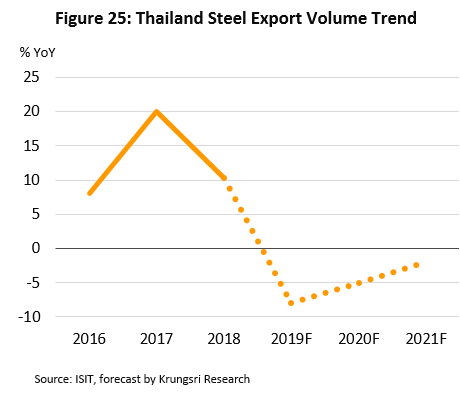
In 2019-2021, rising domestic demand (which absorbs 90% of the output of the Thai steel industry) will help to boost the volume of steel produced in the country. However, despite this positive outlook, Thai operators will be exposed to the risk of increasing imports of steel products that are cheaper than those manufactured domestically, that use high-tech production technologies that are superior to those available in Thailand (such as the materials used in rail tracks) or that are available only in limited quantities on the domestic market.
Trends in the production and consumption of steel in Thailand by product type, 2019-2021
- Long steel products: Demand for long steel products will increase only slightly in 2019, due to the weak growth of the Thai economy and the slow progress of work on government infrastructure projects. However, the outlook should improve in 2020 and 2021 (Figure 27) as the pace of work on large-scale infrastructure projects gathers steam, and because much of the investments that will be made in the near future will be for rail developments (e.g. for twin-track railway, the BMR mass transit system and high-speed rail links) this will necessarily involve greater demand for long steel products, especially for high tensile steel wire, demand for which will increase sharply. This greater domestic demand will then spur increased production of long steel products and output should reach 4-5 million tonnes per year.
Steel bar and section (the most important products in the long steel product group): Demand will tend to see only low levels of growth in 2019 before greater spending by both the public and private sectors pushes growth up to 4-6% in each of 2020 and 2021; most steel bar and section is used during the initial stages of construction, for example when building foundations or the support pillars for the raised tracks of mass transit systems, and so demand will closely follow the release of funds and the start of work.
Output of steel bar and section is forecast to rise over 2019-2021 in line with growth in domestic demand and assistance for the sector coming from the government, which is trying to encourage the use of Thai-produced steel in its infrastructure projects. At the same time, though, Thai producers of steel bar and section are also having to contend with increasing competition on price from imported steel, while Chinese operators are also increasingly setting up their own production facilities in Thailand.
The price of steel bar and section will tend to fall on Thai markets in 2019 and 2020 in step with falling world steel prices, which are being pulled down by the oversupply to global markets, but prices should bounce back slightly in 2021 on rising demand from buyers in construction and the real estate sector, which is expected to invest heavily in a large number of new building projects.
- Flat steel products: For 2019, demand is expected to remain unchanged or to increase only slightly but the outlook will improve in 2020 and 2021, when demand will rise more strongly (Figure 28) as conditions improve for related industrial users, such as manufacturers of machinery and vehicles, while growth in the construction sector and the use of sheet metal in products such as metal roofing and walling will also stimulate demand. Production of flat steel will then increase with demand through 2019-2021 and during these three years, average annual output should run in the range of around 2.5-3.0 million tonnes.
Hot rolled steel (the most important flat steel product): Demand for hot rolled steel is expected to rise in Thailand in 2020 and 2021, and players will benefit from government spending on infrastructure, especially on the new twin-track railway, which will consume increased quantities of metal products, metal tracks and other metal products, as well as from additional demand from the auto sector and manufacturers of electrical appliances, sales of which will rise in step with economic growth. Unfortunately, though, there is only limited room for increases in the production of hot rolled steel in Thailand because the country lacks the ability to manufacture the necessary up-stream steel products. Most companies producing hot rolled steel therefore have to import the slab used as a raw material from overseas, and the result of this is that Thai players find it very difficult to compete on price with suppliers based in other countries.
Over the next three years, the price of hot rolled steel on Thai markets will tend to soften (Figure 26) in step with falls in prices of steel on global exchanges, the latter being in turn caused by the continuing supply glut.
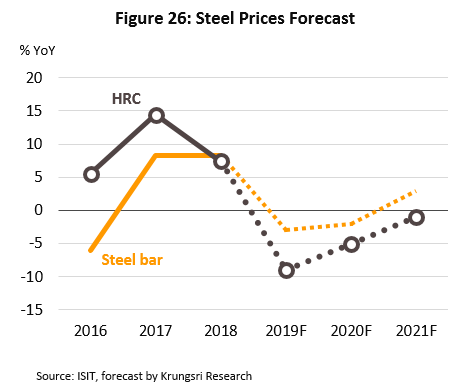
Other factors affecting the industry
- Problems related to cheap imports (especially from China):
- China is still affected by a serious and persistent oversupply of steel, which has continued despite the government having ordered the closure of factories that produce low-quality goods. Some Chinese producers may respond to these moves by increasing their production of higher quality steel and then selling this on export markets, and the expectation is that given the economies of scale that China enjoys, Chinese suppliers will be able to maintain their competitiveness on price. In addition, although to date, investments in the necessary high-tech production facilities have not been made and so most Chinese steel is not of a particularly high quality, China is a source of iron ore, it is possible for the country to produce high quality steel.
- Some Chinese operators have established steel foundries overseas, and as part of this process, Chinese steel producers may open production lines in Thailand and through this, compete directly for market share with Thai operators. The latest data from the Board of Investment shows that in the first quarter of 2019, by value, the largest single share of applications that were approved for investment support came from Chinese operators (with a value worth 26% of all approved applications from foreign investors) and investments in metal production (including steel) were among the top categories of all approved applications coming from the Chinese (again, ranked by value).
- Many countries have introduced measures to counter Chinese stock dumping, including for example, America’s decision to use tariffs as a barrier to trade and India’s moves to reduce imports by building up its own domestic steel industry, but the more countries engage in practices such as this, the greater the incentive for China to sell off its oversupply of cheap steel products on markets in other countries, including Thailand.
Krungsri Research’s view
Output of steel by domestic producers will remain unchanged, or possibly increase slightly, in 2019. This year, production will be held back by a slowing of the economy and the fact that private sector investors have held back on investments while they waited for greater clarity over Thailand’s political direction but in 2020 and 2021, output will rise again as progress is made on government building projects and conditions improve for real estate operators. In addition, the automotive assembly and electrical appliance sectors (downstream consumers of the steel industry) are also forecast to see stronger demand but, at the same time, competition with cheap imported steel will tend to limit increases in operators’ turnover.
- Steel manufacturers: Steel producers: Income will tend to remain flat or rise only slightly due to a combination of weakly growing demand and stiffening competition on price.
- Manufacturers of rebar and structural steel (the most important long steel products): Producers of steel bar and section (the most important products in the long steel product group): Operators’ income will tend to rise in tandem with progress on the government’s build out of new infrastructure, especially work on elevated motorways and mass transit systems, which require construction steel and metal pillars in the reinforced concrete that these structures are built from. The government is also trying to reduce the level of imports by promoting the use of Thai steel but Thai producers may still have to endure rising levels of competition from Chinese investors, who are moving into Thailand and establishing steel production facilities in-country, and this may then limit operators’ profitability.
- Manufacturers of hot and cold rolled steel (the principal flat steel products): Producers of hot and cold rolled steel (the most important flat steel products): In this group of products, the forecast is for turnover to weaken and it will take some time for conditions to recover. This will be because the price of flat steel products will tend to fall with world prices, while stocks of slab (the main raw material from which hot and cold rolled steel is made) were imported at a time when prices were high, and although some producers manufacture flat steel products from scrap, there are only a few of these and in any case, these players now have to absorb higher costs for purchases of scrap metal (caused by a market shortage). Within the flat steel product group, products such as flat steel for forming into train tracks and metal shuttering should see solid rates of growth in demand.
- Steel traders and importers: Traders and importers of steel: Income during the period 2019-2021 is forecast to gradually increase as the outlook improves for related and downstream industries but profit rates will remain flat on an anticipated decline in steel prices.
Traders in midstream and intermediate steel products, such as billet and steel coil, are likely to experience rising income as demand increases from downstream consumers of these goods, including for example, producers of construction materials and auto parts. Income for importers and distributors of scrap metal will improve somewhat on the current demand-driven shortage of supply to the domestic market, while traders in downstream and finished steel goods will also tend to see income rise but falling prices for steel on world markets may cause a decline in their overall profitability.
[1] C-light lip channel: hot-rolled coil formed in C shape, generally used as rood structure, rood purlin , and pipe support.
[2] H-beam steel: hot-rolled coil formed in H shape; used as pole, roof structure similar to that made from C light lip channel but more load bearing structure
[3] This is an estimate of the quantities of intermediate products (both domestically produced and imported) which has been made to avoid double-counting upstream and downstream production. This also includes imports of downstream products which are not produced domestically.
[4] This is because pig iron is not produced in Thailand and although slab and billet can be manufactured in Thailand from scrap, some industries require high-quality steel which is made from pig iron. This steel must therefore be sourced abroad and imported into Thailand.
[5] Department of Trade Negotiations, 2000 quoted from The Iron and Steel Institute of Thailand.6] Global steel demand for use in the construction, machinery and automotive sectors accounts for 53%, 16% and 13% of the total, respectively. (Bloomberg).
[6] Global steel demand for use in the construction, machinery and automotive sectors accounts for 53%, 16% and 13% of the total, respectively. (Bloomberg).
[7] Iron and Steel Institute of Thailand
[8] “Flat demand for next ten years”, Asian steel market outlook (2016) and ISIT.
[9] Steel exports from Thailand to US. respectively account for 14% and 27% in terms of quantity and value of total steel exports of Thailand