Over the three years from 2021 to 2023, manufacturers and distributors of construction materials will see improving business conditions thanks to rising demand on both domestic and export markets. This outlook will be helped by two factors. (i) Overall expenditure on construction within Thailand is expected to grow by an annual average of 4.9-5.2%. This will come from stronger government spending on infrastructure megaprojects, especially in the Eastern Economic Corridor (EEC), and on expansions and upgrades to the national road and rail networks, as well as from a rebound in the economy that will then boost private-sector construction. (ii) As the COVID-19 crisis abates, regional economies (in particular in the CLV countries, the main export target for Thai players) will return to growth and this will then feed into greater activity in construction and real estate markets, while in addition, governments in the region are also spending more heavily on infrastructure.
Revenue for both manufacturers and distributors of construction materials should increase over the coming period, even while competition from both domestic producers and importers is stiff. Against this background, manufacturers will increase the quality of their products by overhauling their production processes and using more advanced manufacturing technology, while distributors will adjust their business models to meet the evolving demands of digital consumers, for example by developing new distribution channels.
Overview
Construction supplies are a crucially important upstream component of the construction and real estate sectors, and because some 60% of all construction costs are for materials (Input-Output Table, 2015), the outlook for the construction supplies industry tends to move with these in a coordinated fashion (Figure 1). The most important product groups can be split into the two groups of building materials (e.g., cement, ready-mixed concrete and construction steel) and home decorations (e.g., ceramic tiles and sanitary wares) and together these account for 64% of sales in the industry (Figure 2).
Industry structure
- Producer: Mid- and large-sized operators enjoy advantages over smaller players in virtue of their stronger financial base, their better management of production processes and their favorable bargaining position relative to suppliers, for example, price and deliveries. This then allows these players to mass produce goods more efficiently, which in turn generates economies of scale for them. In contrast, smaller operators tend to have a weaker financial position and this then forces them to focus on the production of a more restricted and more specific range of goods. The structure of the manufacturing side of the sector is summarized in Table 1.
Trader: At present, Thailand is home to around 8,200[3] distributors of construction materials, split between 163 large players, 723 mid-sized operators, and 7,332 small companies. These can be split into two principal sub-groups, according to the characteristics of the business.
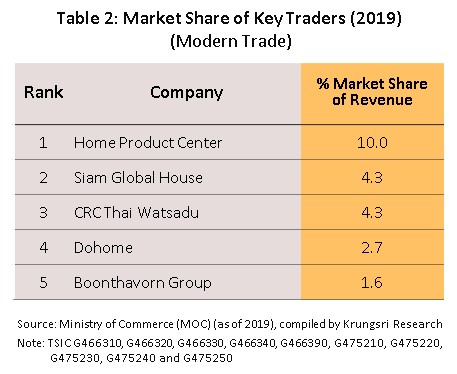
- Modern trader use comprehensive management systems across their business, from the sales floor to the back-office. These operations stock a wide range of construction materials and related goods under a single roof, and these generally cover the complete spread of consumer and trade needs, from basic construction materials through to home repairs, decorations and furniture. Players are generally medium- or large-scale operations that have advantages in terms of their capital base and their lower operating costs, and indeed, many are now in the process of extending their customer bases in the provinces by expanding their branch networks through the regions. One favored strategy for increasing contact points with customers is by offering after-sales services, such as those for home repair and the installation of home appliances. Within Thailand, six large players dominate the market and together these have a 24% share. These are: the HomePro group (HomePro shops themselves are more oriented towards retail, while MegaHome is focused on the wholesale and trade market), Thai Watsadu, Siam Global House, Dohome, and the Boonthavorn Group (Figure 3).
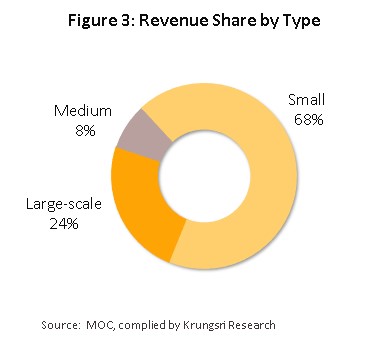
- Traditional trader in the construction sector have more old-fashioned management systems and their operations emphasize the distribution of basic building materials, such as cement, sand and hardware (e.g., locks and nails), together with materials used in home repairs and decoration that meet consumer demand in the local area. However, in the face of rising competition from modern trade outlets, some players are also now beginning to increase their competitiveness by modernizing their operations and offering a more comprehensive set of services. This extends to giving their consumers a wider range of choices that includes not just building materials but also home decorations, renovating their premises, using alternative distribution channels (especially by increasing their online presence), putting in place modern stock control systems, and offering organized delivery services. Nevertheless, traditional players remain at a disadvantage relative to modern trade outlets with regard to their finances, marketing and branding.
Situation
Basic building materials such as cement and construction steel remain important product groups for this market. However, prefabricated building materials (e.g., precast concrete flooring) are increasingly making inroads as operators look to cut construction periods and reduce labor costs, for example, over 2017-2020, sales of these grew at an average rate of 5.1% per year.
The 2020 outbreak of COVID-19 forced the government to institute a nationwide lockdown that brought much of the economy to a temporary halt, and GDP contracted by 6.1% in 2020, after growing by 2.4% in 2019. The construction sector did not escape the year’s economic turbulence and following growth of 2.3% a year earlier, in 2020, total spending on construction rose 1.4%, pulling down the volume of goods distributed to the domestic market[4] by 4.0% (a continuation of 2019’s contraction of 3.4%). However, the two halves of the market have moved in different directions: (i) Investment in construction by the public-sector expanded 4.8% as the government tried to accelerate work on infrastructure projects, but (ii) private-sector spending on construction shrank 2.9% as spending power weakened with the economic recession and real estate developers decided to hold off work on new projects (the number of new houses released to the market crashed 41.6% to 65,065 units in 2020) and instead maintained liquidity and cash flow by selling off unsold stock. Economic troubles across the region also affected exports of construction materials[5] which slumped 17.8% as real estate markets in CLM countries softened.
Overall situation for production and distribution: In 2020, the slowdown in both domestic and export construction sectors meant that the market for construction materials was depressed through the year. Details of this are given below.
- Cement: Output fell 4.1% but domestic sales volume rose 0.9% to 34.8 million tonnes (Figure 4), supported by demand for use in government-backed infrastructure projects. However, demand in the real estate market fell. Exports suffered, slumping 33.7% and generating just THB 6.2 billion, with markets performing especially badly in Cambodia (-57.1%) and Lao PDR (-60.6%) (Figure 5).
- Ready-mixed concrete: This is prepared according to domestic demand so output and sales match each other, both rising 7.8% to 18.2 million cu.m. on stronger demand for use in government infrastructure construction (Figure 6).
- Construction steel (bar and section): Output contracted 13.3% on weaker demand at home and overseas. Having already shrunk by 11.3% in 2019, sales in the domestic market fell by another 15.7% in 2020 thanks to sluggish real estate markets. Exports crashed 32.9%, after shrinking 3.5% in 2019 (Figure 7). Economic weakness and low levels of investment in real estate were also seen across Thailand’s main export markets, and thus sales to Malaysia, Singapore and Lao PDR slumped by respectively 58.4%, 30.6% and 15.2%. Imports moved in step with these declines and fell back 24.4% in the year.
- Ceramic floor and wall tiles: Output declined 8.7% (compared to growth of 2.4% in 2019), while distribution to the domestic market slipped at 3.2%, to 163 million sq.m. (Figure 8) as investment in new residential accommodation dried up; the number of new house builds completed in the year in the Bangkok Metropolitan Region and the four major provinces of Chiang Mai, Chonburi, Khon Kaen and Phuket (together accounting for 78% of all new house construction in Thailand) fell 5.0% (Figure 9). However, exports moved against this trend and rose 9.9% on stronger demand from the US (Thailand’s 3rd biggest market for ceramic tiles, after Myanmar and Lao PDR). Weakness in private construction also drove a 9.3% drop in imports.
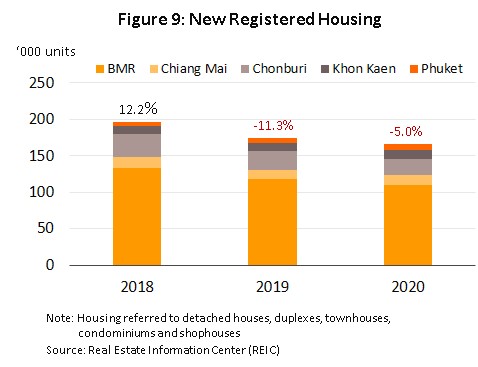
- Ceramic sanitary wares: High levels of stockholding (stocks rose 17.4%) weighed on production, which dropped 14.7% in response. Distribution to the domestic market weakened by 9.9% (Figure 10). The value of exports edged up 1.4% on stronger sales to the US (+32.5%) and Japan (+18.7%). The value of imports also fell 4.0%, with imports from Vietnam and Japan (respectively the second and third most important sources of imports, after China) each down by 50.4% and 51.6%.
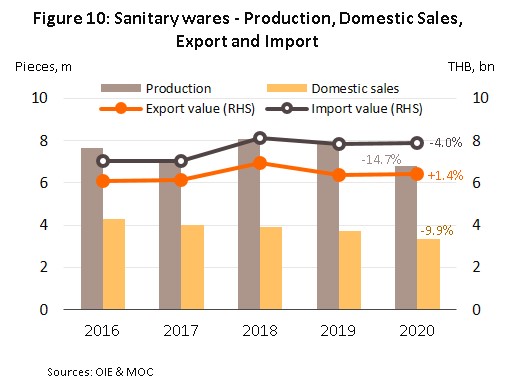
Construction Materials Price Index (CMPI): In 2020, the CMPI slipped 1.8% from its 2019 level due to the weakness in the construction sector, with falls seen in the prices of most product categories (Figure 11). This decline was led by prices for construction steel, which dropped 7.6% in step with lower prices on global markets, though the latter began to turn around at the end of the year as cyclical recovery in the world economy and the relaxation of lockdowns meant that demand returned to the construction sector, helped further by greater investment in infrastructure in many countries. Prices for concrete products slipped 2.0% on a fall in demand for concrete pipes and precast concrete flooring, while those for cement weakened 0.6% as stocks were run down. However, prices for sanitary wares edged up 0.1%, helped by price increases for mirrors, stainless steel handles and water inlet hose. Prices for ceramic tiles also rose 1.7%.
Business performance in 2020
- Producer: Depressed conditions in the real estate sector weighed on manufacturers’ revenue, and this shrank 9.4% to THB 304 billion for the 12 listed companies on the stock exchange that are active in cement, ready-mixed concrete, construction steel, tiles and ceramic sanitary wares (Figure 12). However, despite this, the average net profit margin for these companies increased from 4.2% in 2019 to 4.7% in 2020.
- Cement and ready-mixed concrete: Overall revenue fell 9.9% but a drop in the cost of energy[6], which accounts for around 40% of production costs (Table 1), helped to lift the net profit margin to 5.3% from 4.8% a year earlier.
- Construction steel: Total revenue slumped 23.7% (a continuation of 2019’s fall of 37.1%), though net profits margin improved from -5.1% in 2019 to -3.4% in 2020 thanks to a rise in global steel prices in the last quarter of the year.
- Tiles and ceramic sanitary wares: Revenue contracted 6.6% but the net profit margin held steady at 7.4% on a significant fall in energy costs.
- Trader:In 2020, serious economic weakness and the effects of the lockdown led to a softening of consumer spending power, and as such, revenue for modern trade operations (HomePro, Siam Global House and Thai Watsadu) fell 3.4% from a year earlier (Figure 13). However, net profit margins remained largely unchanged (Figure 14) thanks to much stronger sales of house brands. The latter are cheaper to produce than branded products and the lower retail prices helped to attract much greater consumer interest in a market that was suffering from the recession.
Situation in the first quarter of 2021
In the first quarter of the year, the quantity of construction materials produced and distributed was lifted by a 13.5% YoY rise in investment in construction, driven principally by a 24.0% YoY jump in public-sector spending on building work, most notably on a number of infrastructure projects. This then boosted the domestic distribution of cement and construction steel by respectively 8.2% YoY and 1.6% YoY. At the same time, a recovery in private-sector spending on construction (up 0.4% YoY) and an uptick in work on repairs and renovation underpinned rises of 8.4% YoY and 2.2% YoY in the volume of ceramic tiles and sanitary wares distributed to the domestic market (Table 3).
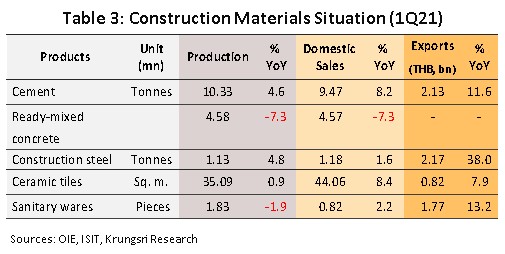
The value of exports also rose in 1Q21, though this was especially strong for sales of construction steel, which jumped 38.0% YoY on a sharp rise in prices and strong growth in the important markets of Indonesia (up 84.1% YoY), Malaysia (up 49.9% YoY) and Lao PDR (up 10.6% YoY). Exports of cement rose 11.6% YoY, with exports to Myanmar (Thailand’s most important overseas market for cement) climbing 31.3% YoY, though sales have now been adversely affected by the country’s deepening political woes.
Combined revenue for the major producers (the 12 companies listed on the stock exchange) slipped 0.5% but the industry net profit margin climbed from 5.1% in 1Q20 to 8.7% in 1Q21. Total revenue for traders[7] also surged 7.8% YoY, while net profit margins stood at 9.8%, helped by players’ use of a wider range of distribution channels. Online sales were especially strong thanks to the emergence of a new wave of COVID-19 infections and the subsequent need for many people to work from home.
Industry Outlook
Demand for construction materials is forecast to pick up over the next 3 years. Krungsri Research sees overall investment in construction rising by 4.9-5.2% annually over 2021 to 2023, driven by government spending that is expected to climb by 7.0% per year as work moves forward on megaprojects that are linked to the EEC development (many of which are joint partnerships with the private sector). This will include phase 3 of the Map Ta Phut Port development and the high-speed rail link connecting the areas 3 airports, for which ground has already been broken. The economic recovery will also help to boost spending on construction by the private sector, which should rise by 2.1% per year (Figure 15).
Outlook for producer and trader: Business trends for players in the construction materials sector are outlined below.
- Cement: The quantity of cement distributed to the domestic market over 2021-2023 is forecast to rise by 3.0-4.0% per year (Figure 16), supported by (i) heavier spending by the public sector on infrastructure construction, especially for work in the EEC (Table 4), and (ii) higher demand from the private sector as the real estate market revives, most notably for residential accommodation (the source of 45% of all demand for cement, Figure 17) in the Bangkok Metropolitan Region (Figure 18).
Having seen depressed conditions in 2020, exports are also forecast to return to growth over 2021-2023 as the economies of the CLV region rebound and investment rises, in particular in infrastructure and real estate (Table 5). The International Monetary Fund (IMF) sees strong GDP growth over the next 3 years for all the CLV countries (Figure 19). In addition, Thai players will be looking to expand into new overseas markets, including Australia and New Zealand. Moving against the trend, Myanmar’s recent decent into severe political uncertainty will impact investment in both residential and non-residential construction and as such, growth in exports there will stall or go into reverse, while the condominium market in Yangon is now weighed down by a supply glut.
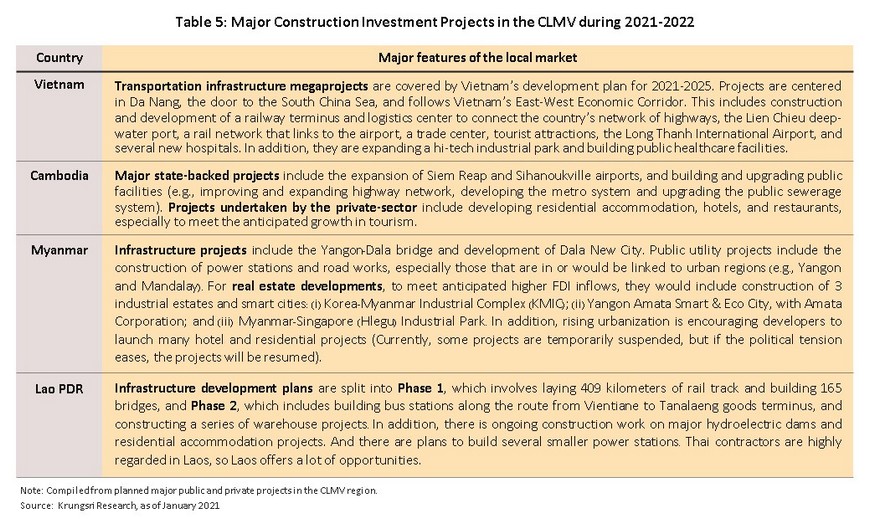

- Ready-mixed concrete: Through 2021-2023, the quantity of ready-mixed concrete distributed domestically should grow by 4.0-5.0% annually, or to around 16 million cu.m. per year (Figure 20) thanks to a stronger demand for use in both public and private sector construction.
- Construction steel: The domestic market sales volume should return to growth that will tend to grow 4.0-6.0% per year over 2021-2023 (Figure 21). This outlook will be supported by (i) an acceleration in the pace of public sector infrastructure construction work, much of which will be for road and rail networks, and (ii) the government’s ‘Made in Thailand’ scheme, which specifies that by value or volume, at least 90% of all construction steel used in government-backed construction projects (excluding public-private partnerships) should be produced in Thailand.
Exports are also forecast to revive in the coming period. (i) Spending on infrastructure construction will increase in many countries, including in Thailand’s main export targets in the ASEAN zone. Following a drop in demand of 0.2% in 2020, Worldsteel thus sees global demand for steel rising by 5.8% to 1.874 billion tonnes in 2021 and then by another 2.7% in 2022 to 1.925 billion tonnes (Worldsteel, April 2021). (ii) Chinese production capacity has fallen by around 20% as a result of government efforts to manage problems with pollution that have resulted in the closure of many dirty foundries.
Ceramic tiles and sanitary wares: The forecast is for the domestic market to recover and for the quantity of goods distributed within Thailand to rise, especially in 2022 and 2023 when an uptick in work on government infrastructure megaprojects (Table 4) will help to lure crowding-in effects in private construction in high- and low-rise residential accommodation. The latter will be particularly concentrated along extensions to Bangkok’s mass transit system and in suburban areas on the outskirts of the city.
Exports are likely to expand further with an improving outlook for real estate markets in the region, boosted by stronger Chinese investment in residential and commercial property.
- Ceramic tiles: Domestic sales volume is expected to rise by 2.0-3.0% per year, bringing total distribution to around 165-170 million sq.m. Export values should also climb by some 5.0% annually (Figure 22) on stronger demand from the US, Lao PDR and Cambodia (major export markets). However, the recovery in the Thai real estate market will in addition pull in more imports, especially from China and Vietnam.
- Ceramic sanitary ware: The domestic sales volume should expand by 4.0-5.0% per year, bringing annual distribution up to 3.5-3.7 million pieces, while export value will grow at the slightly slower rate of 3.0-4.0% per year (Figure 23) as demand deepens in the main markets. This will include the US, where Forisk Research predicts a 7.3% increase in housing starts up to 1.481 million in a year, and which will then continue to grow through to 2027.
Trader of construction materials: Over 2021-2023, modern trade outlets should experience stronger growth than traditional distributors.
- Modern trade operation: In the period 2021-2023, revenue would rise with recovery in the real estate market. Growth will also be supported by a number of different business strategies, including: (i) reducing shop sizes to allow greater expansion into local communities; (ii) opening new types of outlets in cooperation with major manufacturers in order to better meet the particular needs of individual customer groups, for example, the joint venture between Boonthavorn and SCG, which have together launched a construction materials retail operation under the ‘SCG Home Boonthavorn’ brand that will expand into the regions; (iii) increasing the quantity of goods sold under their own brands as a means of controlling costs and increasing profits; (iv) increasing the range of distribution channels used to connect with customers, for example, extending the use of online channels and mobile applications; and (v) expanding the number of branches in the ASEAN region, for example HomePro’s entry into the Malaysia market and the move by Siam Global House to establish a presence in Lao PDR and Cambodia.
- Traditional trader: Over 2021-2023, revenue will tend to remain flat. Players will benefit from an economic recovery that will help to lift the incomes of low- to mid-level segments of the market, especially in the provinces. But traditional outlets will struggle against strong competition from modern trade operations and manufacturers, which will increasingly distribute directly to construction companies.
Over the mid to long term, manufacturers will need to invest in overhauling their production processes and increasing their deployment of technology as they shift to the production of new, higher-quality goods. Players will want to develop new distribution channels that are better suited to meeting the needs of individual consumer groups (e.g., real estate developers or major building contractors), whether that be with regard to design, construction time or durability, while environmentally-friendly materials will also likely rise in importance. At the same time, distributors will need to adapt their services to match how consumer needs are evolving under the pressure of digitalization, for example by offering end to end services, expanding the range of online and offline contact points that connect distributors and consumers (i.e., engaging in omni channel marketing), and developing personalized marketing platforms.
In the next 3 years, prices for construction materials will tend to rise (Figure 24) because of: (i) stronger demand from the construction sector; (ii) government policy that specifically encourages the use of Thai-made products; (iii) an expected increase in the price of upstream imports, for example, of scrap and billet, which should rise with stronger global markets; and (iv) rising energy costs.
Krungsri Research’s view
Both producers and traders of construction materials will see better business conditions over the years 2021-2023 as the construction sector strengthens on (i) an increase in public sector construction both at home and in the broader region, especially in work on megaprojects; (ii) recovery in the real estate market, in particular in the Bangkok Metropolitan Region and in the bigger provincial centers; and (iii) the economic recovery that will come in the wake of the COVID-19 crisis. Given these factors, the market for both building materials and for home decorations should improve in the coming period.
Producer:
- Cement: Revenue is expected to rise in line with a return to investment in construction by the public and private sectors. In addition, cement manufacturers will also look to expand into new territories (e.g., Australia and New Zealand) to relieve their dependency on existing markets in the CLMV countries.
- Ready-mixed concrete: Revenue for manufacturers will grow with expansion in domestic construction, although large players that have expanded overseas will also see revenue rise from these markets.
- Construction steel (bar and section): Having been depressed for some time, revenue should begin to grow again on stronger demand and rising prices. However, Thai manufacturers will have to deal with stiff competition from low-cost imports from China and Vietnam.
- Ceramic tiles and sanitary wares: For players in this segment, revenue should rise in step with the better outlook for the real estate market, especially for residential accommodation. However, the supply of unsold housing stock remains high, and this may pose a risk to revenue, while players will also have to contend with the challenges posed by imports of low-cost goods from China.
Trader:
- Modern trader: Revenue for these operators will tend to increase as the economy returns to growth and businesses expand the number of outlets that they operate, extend the range of distribution channels that they utilize, and increase their involvement with own-brand products. Moreover, modern trade operations benefit from consumers’ increasing preference for shops that carry a wide and comprehensive range of choices and that offer after-sales services such as home repairs and extensions.
- Traditional trader: For wholesaler, revenue growth is likely to be flat or improve slightly because of a likely increase in construction-related activity across the country. Players will face obstacles in the form of rising competition from modern trade outlets and manufacturers selling directly to their customers. For retailer, revenue is likely to remain flat, although sales of home decorations or goods used in home repairs and extensions may see some growth.
[3]This number includes companies that are registered with the Ministry of Commerce, that have submitted a complete set of financial accounts for each of the 5 years from 2015 to 2019, and that have declared an annual revenue of at least THB 500,000.
[4]Calculations of the quantity of construction materials distributed to the market are based on figures for cement, ready-mixed concrete, tiles, sanitary wares and construction steel. Together, these account for 60% of the market for building materials in Thailand.
[5]Exports are calculated from sales of cement, tiles, sanitary wares and construction steel.
[6]Prices for Dubai Crude crashed 33.2% in 2020 to an average of USD 42.2/bbl from USD 63.2/bbl in 2019. Prices for natural gas also dropped 19.8% in 2020, falling to an average of USD 2.03/MMBtu.
[7]This includes HomePro and Siam Global House but because Thai Watsadu is not listed on the stock exchange, there are no accounts available for 1Q21 and so it is excluded from the calculations.