EXECUTIVE SUMMARY
The construction materials industry will enjoy an improving outlook over 2023 to 2025 thanks to better conditions on both domestic and international markets. (i) Overall domestic expenditure on construction is forecast to expand by 3.0-3.5% annually, lifted by a combination of an acceleration in government investment on megaprojects connected to the Eastern Economic Corridor (EEC) and upgrades and expansion of the national road and rail networks, and growth in the economy that will then feed greater private sector spending on residential accommodation. (ii) With the COVID-19 pandemic now receding, regional economies are rebounding, and this will support increased spending on infrastructure and real estate projects across the region, especially in Thai operators’ principal export market of the CLM nations.
Manufacturers and distributors will see their income rise amidst the stiff competition coming from both other Thai players and overseas producers exporting into the Thai market. Manufacturers will tend to respond to this situation by stepping up their investment in technology, and this will then pave the way to the production of higher-quality goods that are a better match for changing market demand, especially given the increasing focus on sustainability and the ESG model. Likewise, in response to consumer behavior that is evolving under the impact of new digital technologies, distributors will also need to adjust their operations, for example by developing new channels through which to connect with their customer base. Despite this positive outlook, players will nevertheless face the risk arising from: (i) rising imports of construction steel and ceramic tiles, especially from China and Vietnam since these enjoy a price advantage relative to Thai products; (ii) the likely elevated price of crude, which will add to energy costs; and (iii) continuing labor shortages that will affect both the construction industry and manufacturers of construction materials.
Krungsri Research view
Over the three years from 2023 to 2025, producers and traders of construction materials will see improving market conditions as activity in the construction sector picks up, boosted by: (i) strengthening investment in construction (especially in megaprojects) by the Thai and neighboring countries’ governments; (ii) recovery in the real estate sector, in particular in the Bangkok Metropolitan Region and in provincial centers; and (iii) increasing demand for repairs and improvements to residential properties that is forecast to occur as the economy expands and consumer purchasing power rises.
Producers of construction materials:
-
Cement: An overall increase in spending on construction will lift incomes for cement manufacturers, though exporters will also tend to move beyond their traditional markets in the CLM countries as they explore new opportunities in Australia and New Zealand.
-
Construction steel (bar & section): Rising prices will mean that manufacturers’ income will recover from its recent depressed state, but the domestic industry will have to contend with strong competition from low-cost imports from China and Vietnam.
-
Ceramic tiles and sanitary wares: Greater activity in the real estate sector, in particular in the market for residential accommodation, will support a steady recovery in income, though the significant backlog of unsold housing stock and pressure from cheaper imports from China will place a limit on how far incomes will rise.
Traders of construction materials:
-
Modern traders: For these players, income will tend to strengthen as: (i) economic activity picks up and investment in construction improves; (ii) businesses expand their branch networks and exploit new distribution channels (e.g., online platforms); (iii) operators deepen their involvement with own- or house brand products; and (iv) consumer preference increasingly favors outlets that carry a wide and comprehensive range of choices and that offer after-sales services such as home repairs and extensions.
-
Traditional traders: For traditional wholesalers, income growth will be flat or at best only mild because despite a likely increase in construction-related activity across the country, players will face rising competition from modern trade outlets and manufacturers selling directly to their customers. For traditional retailers, income will remain flat, although sales of home decorations or goods used in home repairs and extensions may see some growth.
Overview
Construction supplies are a crucially important upstream component of the construction and real estate sectors. As some 60% of all construction costs are for materials (Input-Output Table, 2015), the outlook for the construction supplies industry tends to move with these in a coordinated fashion (Figure 1). The most important product groups can be split into building materials (e.g., cement and construction steel), which account for 39% of the market for all construction materials, and home decorations (e.g., ceramic tiles and sanitary wares), which represent another 10% of the market (Figure 2). Apart from sanitary wares, sales of the main product categories are mostly in the domestic market (Figure 3).
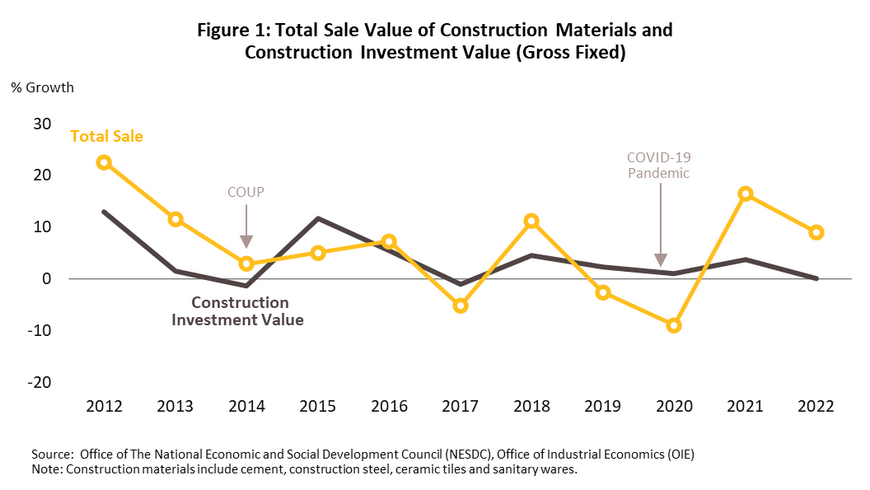
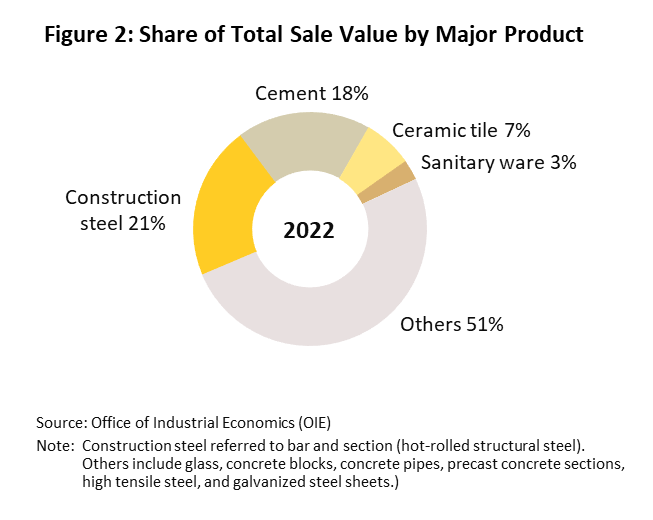
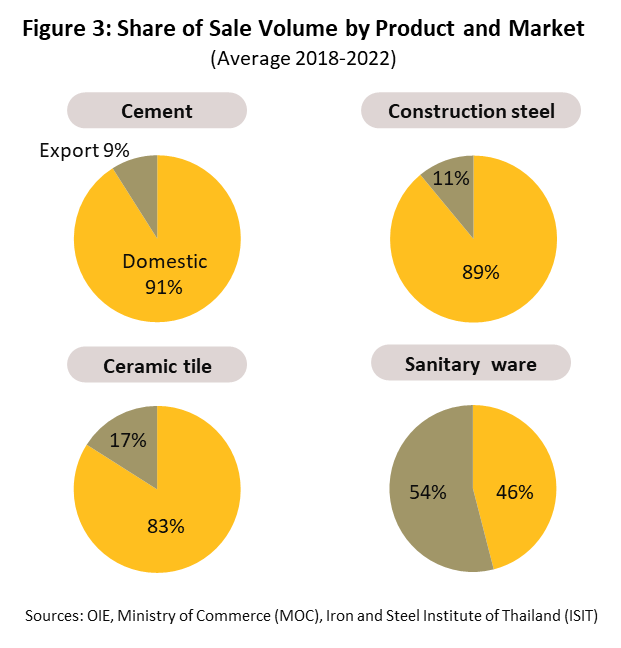
Industry structure
-
Producers: As of 2022, there were 122 mid- and large-sized operators registered in Thailand (i.e., companies that had submitted accounts for the period 2018-2022). These enjoy advantages over smaller players in virtue of their stronger financial base, their better management of production processes, and their favorable bargaining position relative to suppliers with regard to, for example, price and deliveries of inputs. This then allows these players to mass produce goods more efficiently, which in turn generates economies of scale for them. In contrast, smaller operators, of which there are 205, tend to have limited finances and this then forces these to produce goods in smaller production runs, adding to marginal manufacturing costs. The structure of the manufacturing side of the industry is summarized in Table 1 below.
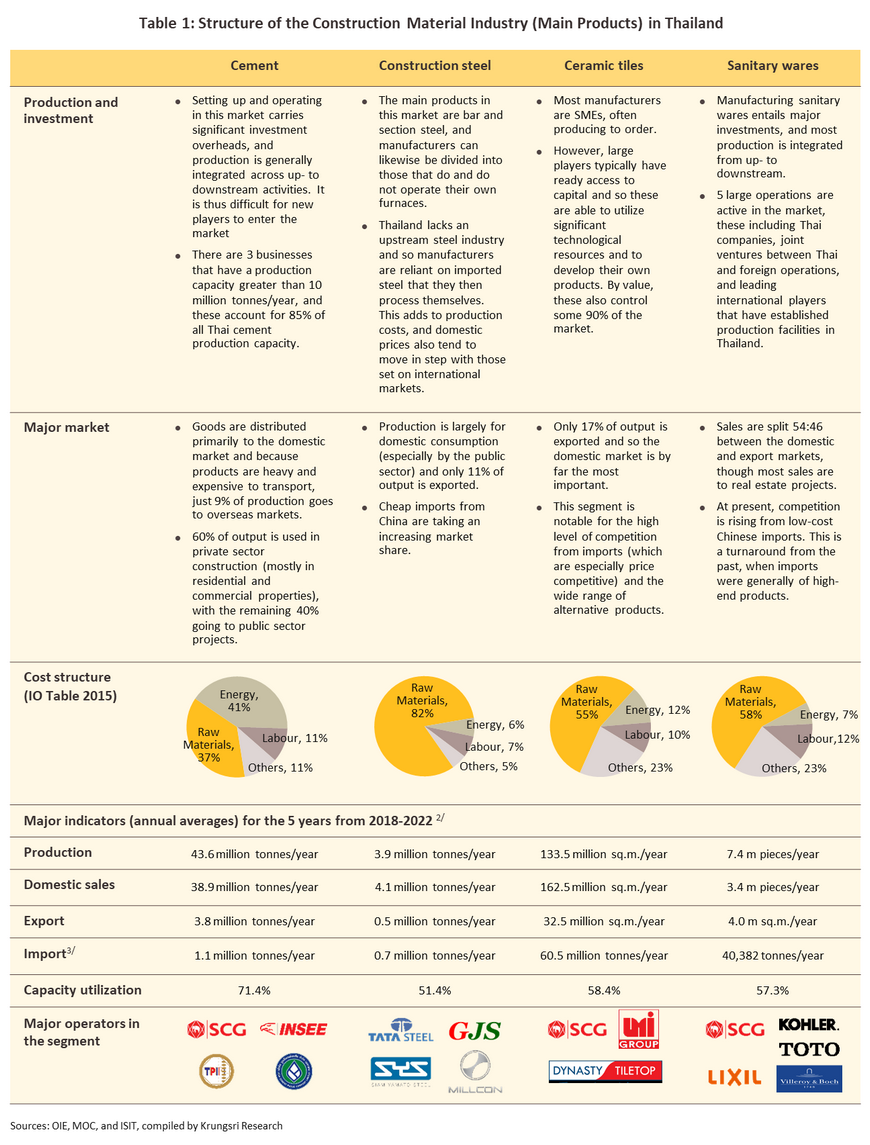
-
Traders: As of 2022, Thailand was home to around 980 distributors of construction materials1/, split between 35 large players, 127 mid-sized operators, and 818 small companies. These can be further categorized according to the characteristics of each business.
-
Modern Traders are notable for their use of comprehensive management systems across their businesses, from sales floor to back-office services. These operations stock a wide range of construction materials and related goods under a single roof, and these generally cover the complete spread of consumer and trade needs, from basic construction materials to home repairs, decorations, and furniture. Players are generally medium- or large-scale operations, and these have advantages in terms of their capital base and their lower operating costs. Many of these are now in the process of expanding their customer bases in the provinces by extending their upcountry branch networks. One favored strategy for increasing contact points with customers is by offering after-sales services, such as those for home repair and the installation of appliances in and outside the home. Within Thailand, five large players dominate the market and as of 2022, these had a combined 75% share of all income going to retailers of construction materials. These are: The HomePro group (HomePro shops themselves are more oriented towards retail and home decorations, while MegaHome is focused on the wholesale and trade market), Thai Watsadu, Siam Global House, Dohome, and the Boonthavorn Group.
-
Traditional traders in the construction sector have more old-fashioned management systems and their operations emphasize the distribution of basic building materials, such as cement, sand, and hardware (e.g., locks, nails, etc.) together with materials used in home repairs and decoration targeted at the consumers in the local area. However, in the face of rising competition from modern trade outlets, some players are also now beginning to raise their competitiveness by modernizing their operations and offering a more comprehensive set of services. This extends to giving their customers a wider range of choices that includes not just building materials but also home decorations, renovating their premises, using alternative distribution channels (especially by increasing their online presence), putting in place modern stock control systems, and offering organized delivery services. Nevertheless, traditional players remain at a disadvantage relative to modern trade outlets with regard to their finances, marketing, and the strength of their brand.
Situation
Producer
In 2022, depressed conditions in the construction sector undercut production and domestic sales in almost all the main product categories. This was principally the result of the only slow progress that was made on government infrastructure projects, though private sector real estate also demonstrated only weak levels of growth in the year. (Overall spending on construction expanded by just 0.2% in 2022, with public sector investment contracting -0.8% and private sector spending up 1.6%). Alongside this, exports also slipped4/ on the weaker economic outlook in core export markets.
-
Cement
-
Production (excluding clinker) dropped -1.5% to 42.7 million tonnes, thus continuing the 3-year decline that began in 2020. Domestic sales also slipped, weakening -3.2% to 38.5 million tonnes on depressed conditions in the construction sector and the run-up in energy prices, which then added to manufacturing and transportation costs. This was the first such decline in sales reported since 2018 (Figure 4).
-
Exports volume slumped -37.9% by volume and -25.7% by value to totals of respectively 2.2 million tonnes and THB 4.7 billion. Sales to Myanmar (42% of Thai cement exports) dropped -34.5% as a result of the country’s ongoing political troubles and the impact of this on government construction projects. Exports to Cambodia (24% of the total) also crashed -34.1%, although those to Lao PDR (11% of all cement exports) edged up 2.5% (Figure 5).
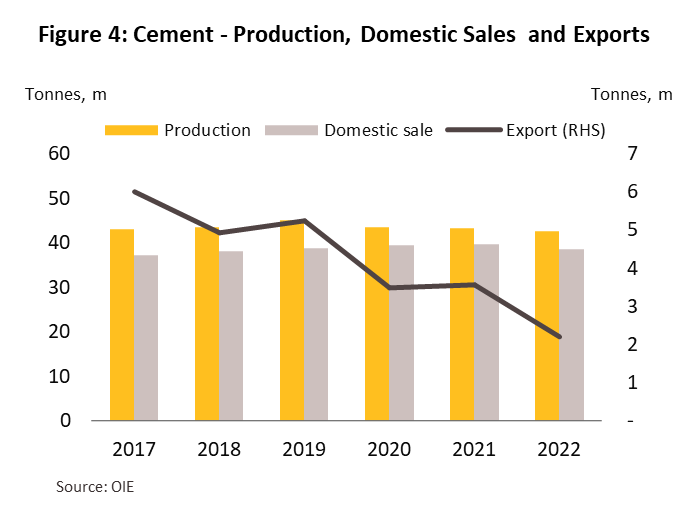
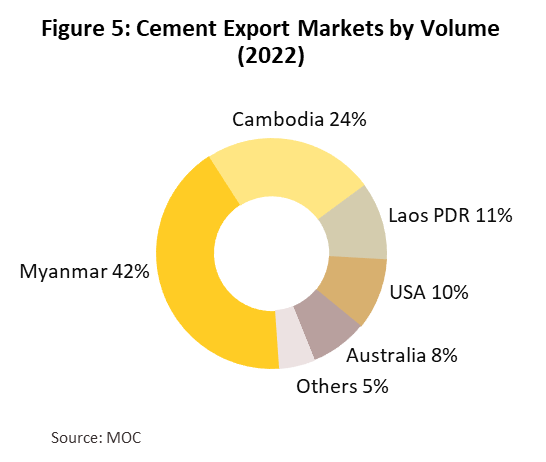
-
In recent years, cement manufacturers have begun to move the industry onto a more sustainable footing by investing in the development of new technology, including in the production of hydraulic cement. Because the latter uses eco-friendly materials in place of clinker5/ (Figure 6), this helps to cut CO2 emissions. The Ministry of Industry (February 2023) estimates that compared to producing a tonne of Portland cement, producing a tonne of hydraulic cement reduces CO2 emissions by 0.05 tonnes. Given this and because hydraulic cement can be used in place of more carbon-intensive Portland cement, it is estimated that its use helped to prevent the release of more than 0.3 million tonnes of CO2 in 2021 (Thai Cement Manufacturers Association: TCMA) (Figure 7).
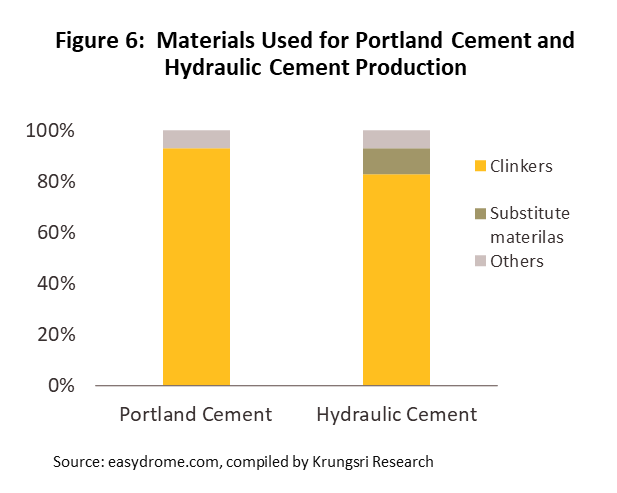
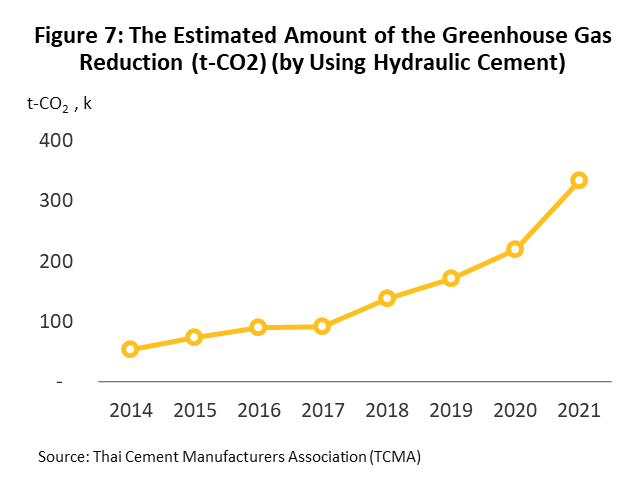
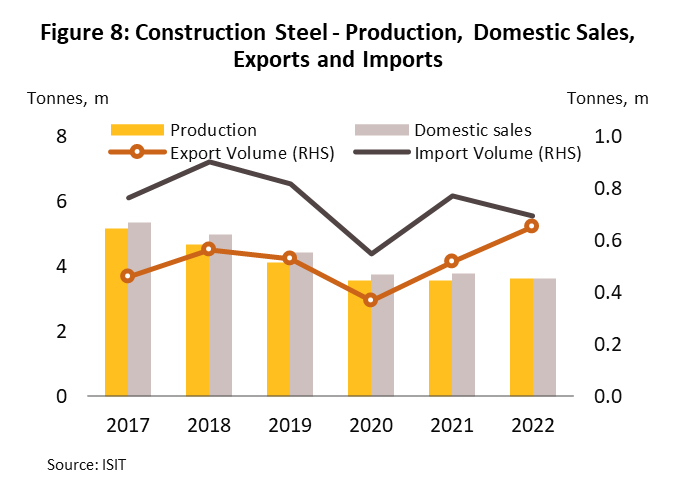

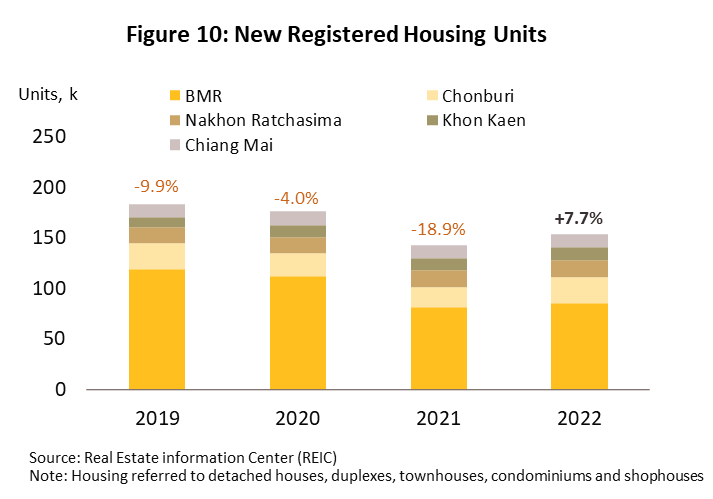
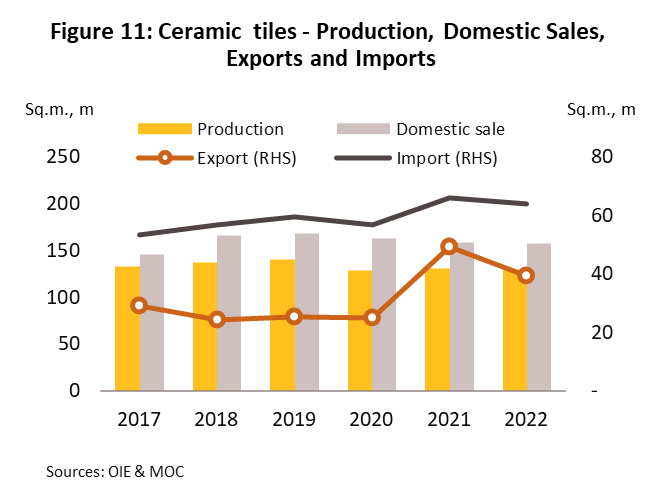
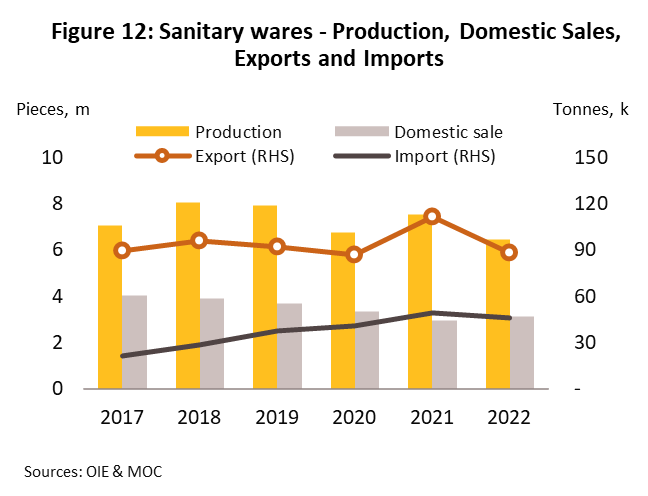
Construction materials price index
Construction Materials Price Indexes (CMPI) rose by 5.7% in 2022, having already climbed 8.0% in 2021. In particular, prices for steel and cement strengthened by 8.3% and 6.5% on higher prices for energy, raw materials, and transport, despite weak demand from the construction sector (Figure 13). (i) Global energy costs increased year-on-year due to intense geopolitical tensions, especially over the extended Russia-Ukraine war. (ii) Higher production and transportation costs lifted prices for inputs including gypsum and scrap steel. (iii) Electricity costs were up (Figure 14). (iv) The baht weakened from a year earlier, adding to the cost of imports of raw materials (especially of steel). (v) Global output of steel contracted as Chinese production came under pressure from weakness in the real estate sector (in 2022, Chinese steel output fell -1.7%). As such, steel supply to the global market contracted and prices rose.
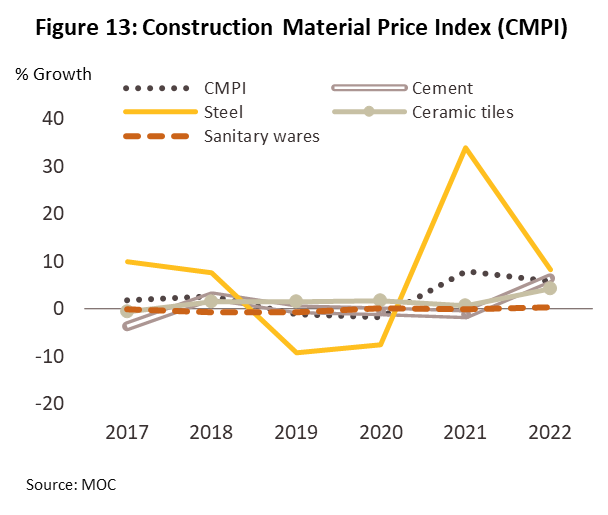
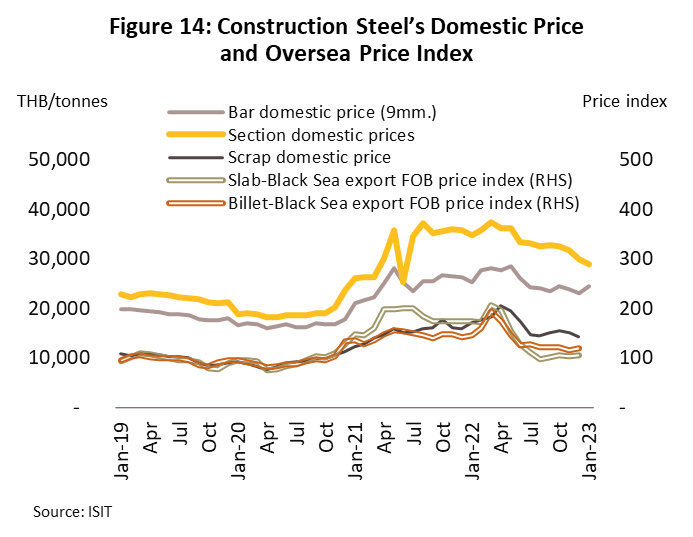
Business performance in 2022
Producers
Overall income for manufacturers of construction materials6/ expanded by 12.0% to THB 398 billion (Figure 15), though net profit margins for the 10 largest players tightened to 3.0%, down from 5.8% in 2021.
-
Cement: Overall income (for 3 players) climbed 15.1% on higher prices that were themselves pushed up by the elevated cost of energy (the latter accounts for 40% of all production costs, see Table 1). However, income failed to keep pace with costs and so average net profit rates softened from 9.8% to 7.1%.
-
Construction steel: Income for the 3 main players fell -0.5% on weaker demand for steel for use in infrastructure projects, though this followed a 17.0% jump in income in 2021, when tight supply led to surging global prices that then boosted turnover. However, conditions were depressed in the construction sector in 2022, while rising energy costs added to production overheads. Net profits thus turned negative, contracting -3.4% (this compares to growth of 6.2% a year earlier).
-
Ceramic tiles and sanitary wares: Overall income (for 4 main players) rose 11.4%, doubling average net profits from 2.4% to 4.8%. This segment benefited from recovery in investment in residential accommodation (52% of all private sector investment in construction made in 2022).
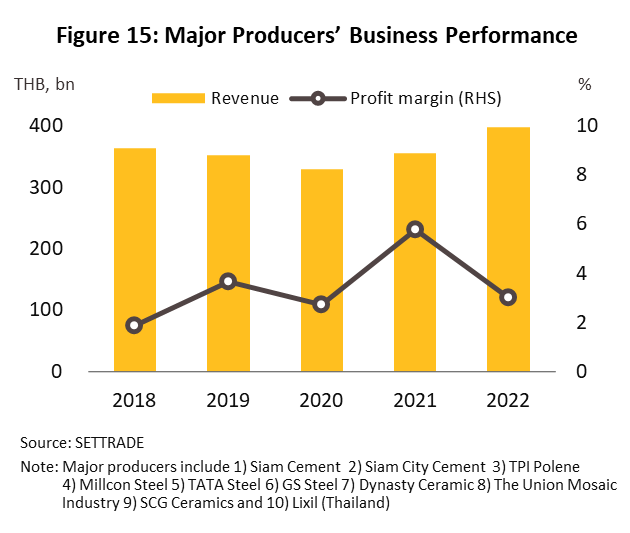
For modern trade outlets7/ turnover was up 15.0%, with net profits averaging 6.0% (Figure 16). Through 2022, the industry benefited from: (i) the expansion of operators’ branch networks, both in the Bangkok Metropolitan Region and upcountry; (ii) the development of online distribution channels, which helped to better align retailers with the behavior of modern digital consumers; (iii) the provision of comprehensive building services to the public that cover construction, house extensions, and decoration and renovation; and (iv) expansion in sales of house brand goods, which because they carry lower marketing costs, are cheaper than other branded products.
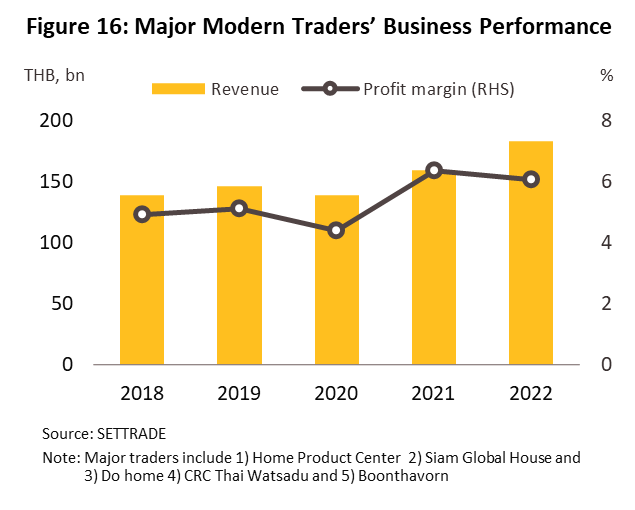
Situation over the first 5 months of 2023
Overall spending on construction rose 5.9% YoY through the first quarter of 2023, with this split between a 7.6% YoY increase in public sector construction investment and 3.1% YoY growth in private sector construction. In particular, the acceleration in work outlined in phase 2 of the EEC development plan (covering the years 2023-2027) fed through into a 9.2% YoY expansion in spending on government infrastructure projects, and this then supported a 13.0% YoY increase in sales of construction steel over the first 5 months of the year. Likewise, the volume of ceramic sanitary wares distributed to the market inched up 1.1% YoY on stronger investment in private sector residential real estate (up 4.6% YoY). However, the situation was less favorable in the markets for cement and ceramic tiles, and over 5M2023, sales of these declined by respectively -3.1% YoY and -6.2% YoY. These declines were partly driven by the effect of the rising cost of living on consumer spending power, which then affected demand in the renovation market.
Exports fell in all the major product categories during 5M2023. Overseas sales of cement fell to 0.75 million tonnes (down -29.0% YoY), with sales into Myanmar, which with a 49% share of cement exports is Thailand’s most important market, dropping -26.0% YoY as the country’s ongoing political trials took their toll on the construction sector. Exports of construction steel were also down -23.7% YoY, though this was split between a decline of -39.3% YoY for sales of formed steel/section and growth of 25.7% YoY in sales of rebar. Likewise, sales of ceramic tiles and sanitary wares dropped by respectively -35.4% YoY and -27.2% YoY (Table 2) on weaker sales into the main markets of, in the former case, Myanmar (down -28.6% YoY on squeezed consumer spending power) and in the latter, the US (down -49.3% YoY as the housing market weakened in the face of an aggressive cycle of rate rises). At the same time, imports strengthened, though this was especially so for low-cost goods from China, the supply of which expanded following the ending of lockdowns there. Thus, imports rose 25.2% YoY for all types of construction steel, 12.7% for ceramic tiles, and 19.2% YoY for sanitary wares, though considering just tiles and sanitary wares from China, imports were up by an average of 8.2% YoY and 21.6% YoY.
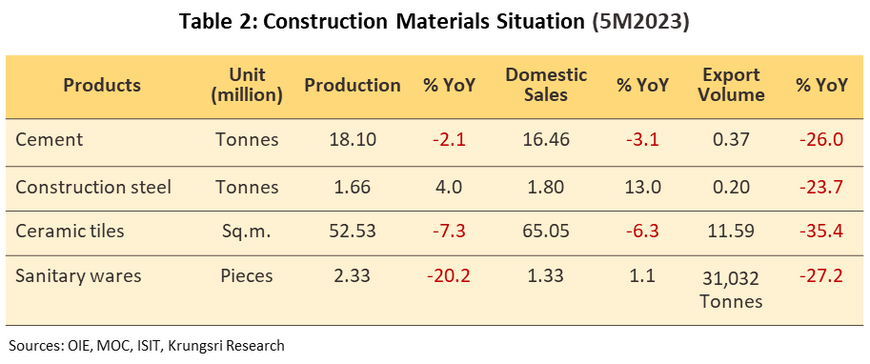
-
Over 1Q23, combined income for producers of construction materials listed on the stock exchange8/ fell back by -5.5% YoY (Figure 17), with net profit margins also sliding to 3.7% from 7.5% in 1Q22. Profits were hurt by the higher cost of energy and transport since these contribute a significant share of all overheads (Figure 18). For traders9/, overall income was up 3.0% YoY and net profit margins averaged 7.2%. Players benefited from expansion in the use of alternative (and especially online) distribution channels and from growth in sales of house brands, which helped to reduce marketing costs.
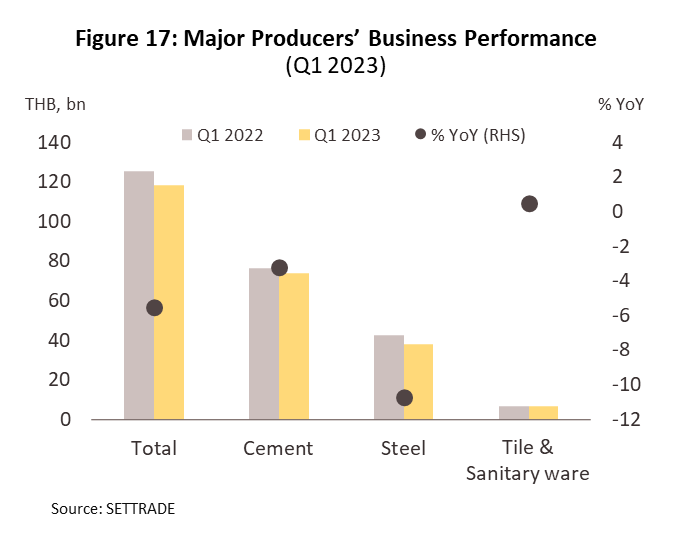
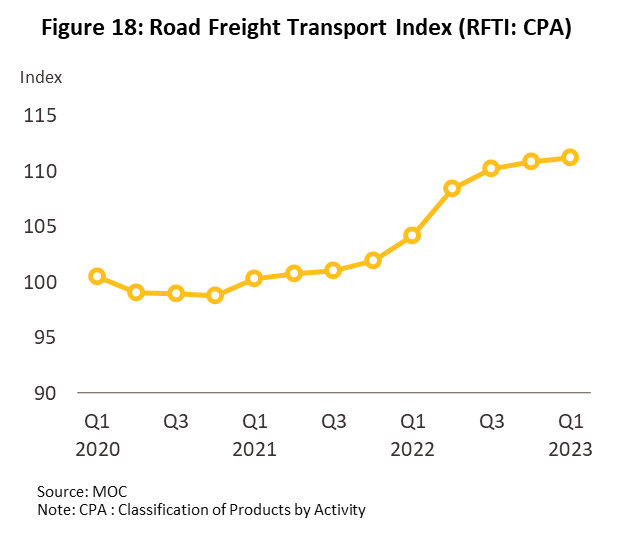
Outlook
Over 2023-2025, demand for construction materials will strengthen in step with growth in investment in the construction sector itself. The latter is forecast to expand by 1.5-2.0% in 2023 and then by an average of 3.5-4.0% in each of 2024 and 2025 (Figure 19).
-
Producers will strengthen on greater investment in large scale projects, especially those connected to the EEC development. In particular, the action plan for phase 2 of the EEC development covers the years from 2023 to 2027, and this specifies work to be completed on infrastructure and utilities that initially includes 77 projects with a value of THB 340 billion (Figure 20), though demand will also be driven by work on megaprojects elsewhere in the country. In addition to the initial outlay by the government, these are expected to pull in further private sector investment in their wake, including for the construction of residential housing projects along new mass transit lines and roads, as well as of factories and industrial estates in nearby areas.
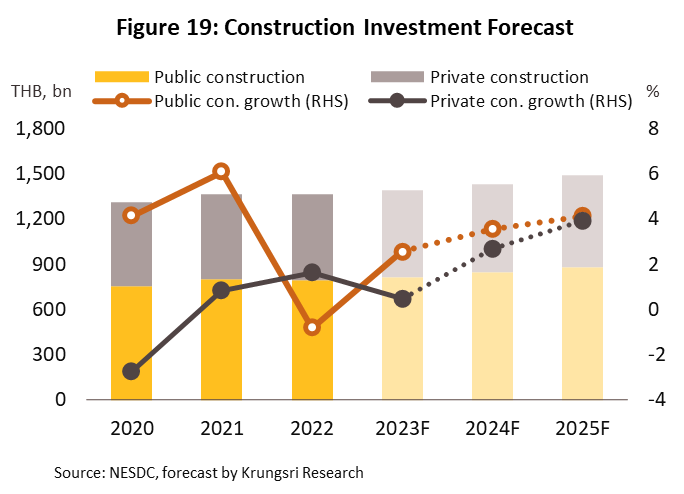
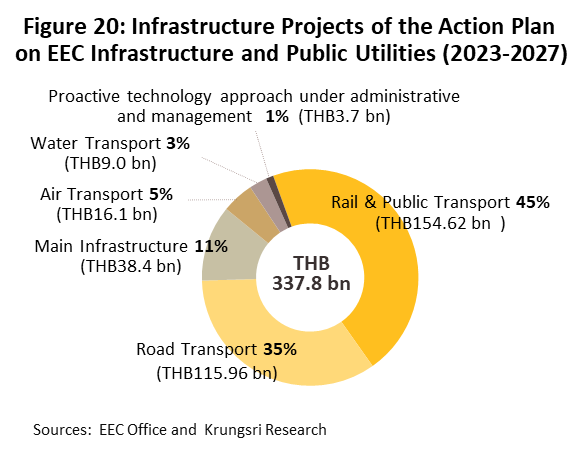
-
Cement: The volume of goods distributed to the domestic market should expand by 3.0-4.0% annually over 2023-2025 (Figure 21). Sales will be boosted by greater progress on infrastructure projects, though demand will be especially strong during the first phases of work on these projects, e.g., the laying of foundations for elevated mass transit lines and the build out of new train tracks that will connect to the EEC. Export markets will remain sluggish through 2023, but the outlook should improve in 2024 and 2025 as economies improve and investment in construction (especially in infrastructure and real estate) picks up in neighboring countries. The International Monetary Fund thus sees the GDP of the CLM countries continuing to grow through 2023 and 2024 (Figure 22), while Thai players will also look to open up new opportunities and diversify their exposure to risk by expanding exports to new markets including Australia and New Zealand.
In keeping with rising global concerns over the environment, the industry, particularly the largest manufacturers, is moving towards a greater focus on the production of ‘green cement’. Interest in hydraulic cement is especially intense since unlike regular Portland cement, which generates around 60% of its weight in CO2 during the production process, for hydraulic cement, this falls to around 40% (Verified Market Research, November 2022). This is in line with the targets set by the TCMA for cutting greenhouse gas emissions10/ by at least 1 million tonnes of CO2 by 2023 (Figure 23), and with general ESG (environment, social, and governance) considerations that underline the importance of reducing environmental impacts across the product life cycle.
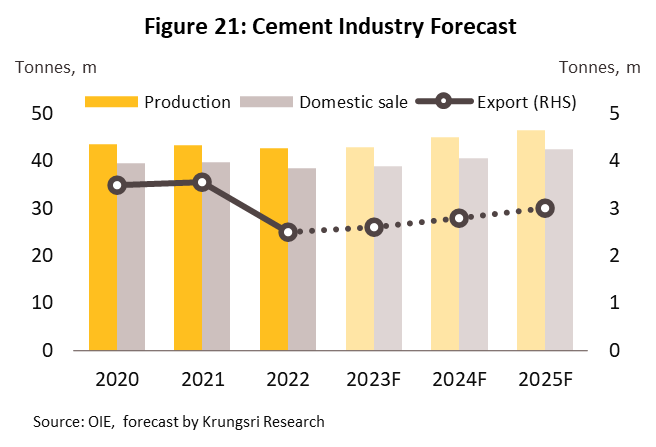
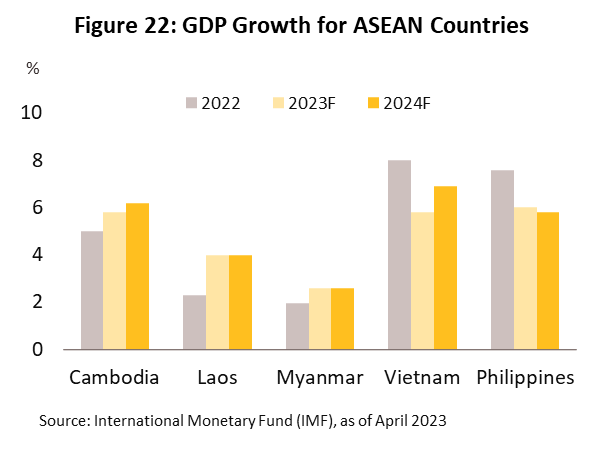
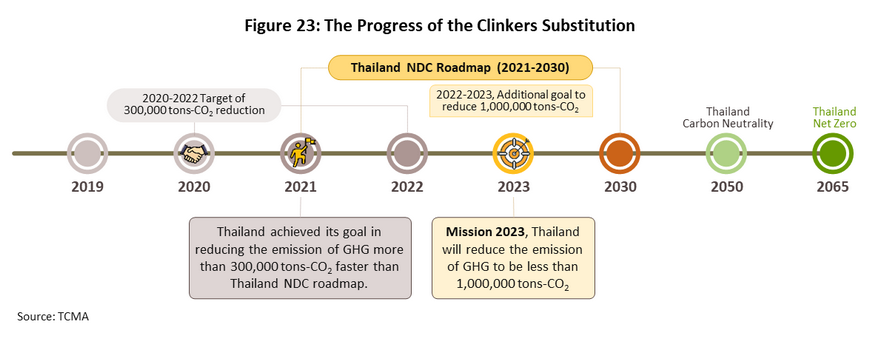
-
-
Construction steel (bar and section): The quantity of construction steel distributed to the domestic market is expected to stay flat in 2023, though this should then expand by 5.5-6.0% in each of the following two years (Figure 24) as spending on construction by both the public and private sectors picks up. Exports will strengthen steadily as governments in many countries begin to accelerate investment in infrastructure projects now that COVID-19 is in abeyance, though this will be especially noticeable in the ASEAN region, home to Thailand’s main export markets. Indeed, Worldsteel estimates that having contracted by -0.3% in 2022, demand for steel in the ASEAN countries will grow by 6.2% in 2023 and then by 5.7% in 2024 (Worldsteel, April 2023) (Figure 25). However, imports will also rise in step with growth in activity in the construction sector.
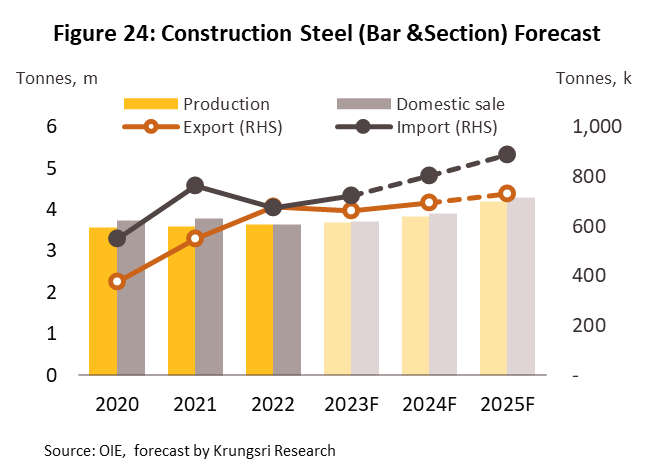
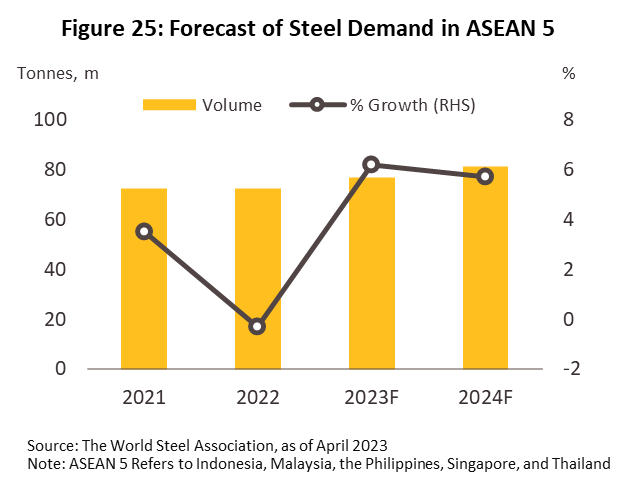
The Thai steel industry, and in particular those players manufacturing for the export market, will see sales come under greater pressure from stiffening barriers to trade. In particular, the EU’s new Carbon Border Adjustment Mechanism (CBAM)11/ specifies that from October 2023, importers to the EU of heavy industrial goods (including steel) must declare the carbon emissions involved in the manufacture of these goods in their originating country, and from 2026, importers will also need to purchase a CBAM Certificate if these goods are responsible for carbon emissions in excess of the specified limits. This will then naturally add to import costs, though in 2022, combined imports of iron, steel and aluminum products from Thailand to the EU had a value of THB 9.3 billion, or just 1.0% of the value of all Thai exports to the bloc. Rather, the main suppliers of iron and steel to the EU are Turkiye, Russia, and India (Figure 26).
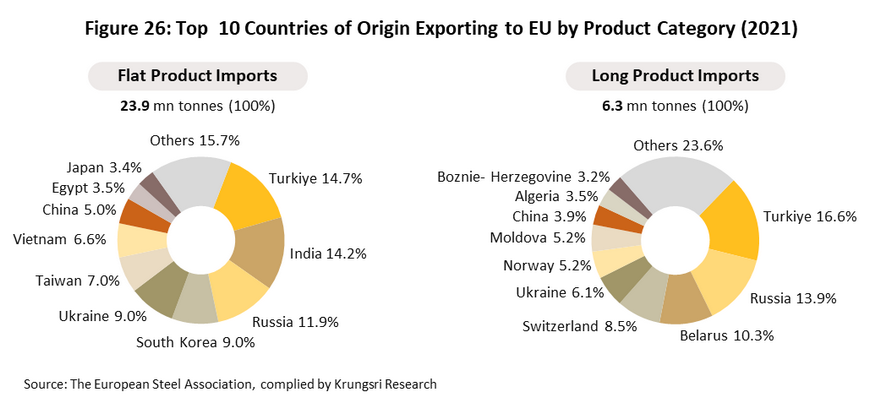
Thai players that are currently exporting products to the EU that fall within the scope of the new CBAM regulations will likely have to shoulder higher costs arising from the need to invest in new production technology and then to pass CBAM assessments, and one result of this may be to encourage those who fail to meet the CBAM standards to look for new export markets. Thai manufacturers are also likely to increase their use of electric arc furnaces (EAFs) and many, especially major players, are indeed already moving down this road. Use of EAFs offers several advantages, and in addition to giving foundries better control over the quality of their output (EAFs are able to remove impurities from molten steel), these also cut energy use by up to 75% compared to traditional furnaces (Millcon Steel, 2022). Replacing carbon-intensive fossil fuel-fired furnaces with EAFs will therefore have an important role to play in cutting greenhouse gas emissions and increasing production of environmentally friendly or ‘green’ steel. In fact, at present over 20% of production capacity in the major steel producing countries comes from EAFs. This is, however, with the exception of China, though as a consequence, Chinese officials trying to control pollution levels have had to close foundries that failed to meet emissions standards) (Figure 27).
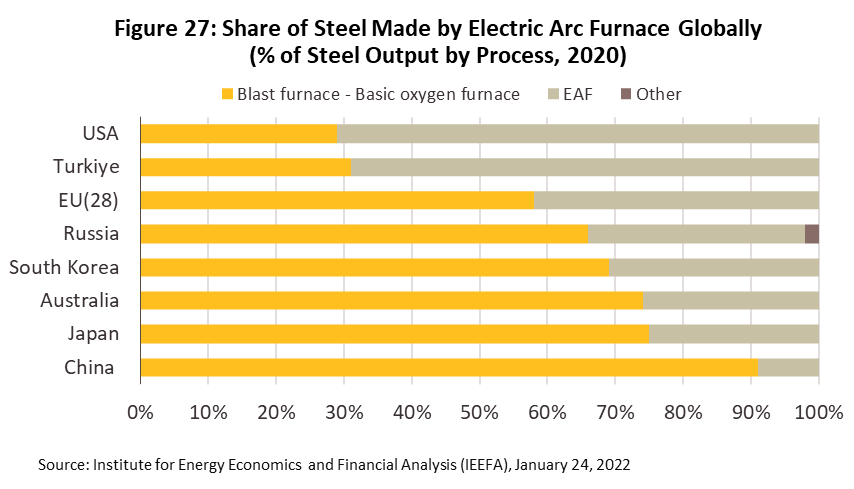
-
-
Ceramic tiles and sanitary wares: Domestic sales of tiles and sanitary wares to the domestic market is forecast to grow at an annual rate of respectively 1.0-2.0% and 2.5-3.0% over the period from 2023 to 2025 (Figure 28 and Figure 29). Sales will benefit from the rebound in foreign tourist arrivals and an increase in overall economic activity, which will support a rise in consumer spending power, and with this, domestic real estate markets should strengthen. Over the same period, exports are forecast to expand at an annual rate of 3.3% for tiles and 0.8% for sanitary wares, with growth especially strong in the main markets of Lao PDR and Cambodia. In 2021 (the most recent year for which data are available), 40% of all imports of ceramic tiles to Lao PDR were from Thailand, and imports will continue to trend upward as the country’s residential property market grows. Likewise, sales in Cambodia will benefit from the forecast 11.5% (CAGR) expansion in spending on the construction of residential accommodations that should be seen over 2021-2026 (Market and Research, November 2022). Similarly, imports of tiles and sanitary wares (mainly from China and Vietnam) are expected to rise by respectively 1.6% and 2.0% annually as the domestic markets for residential, commercial, and industrial property all strengthen.
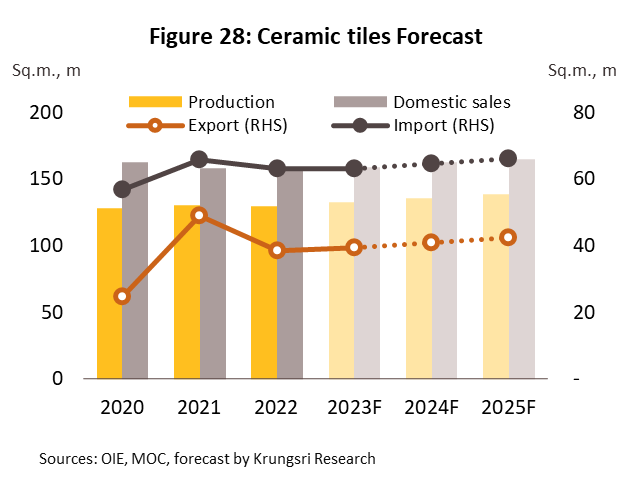
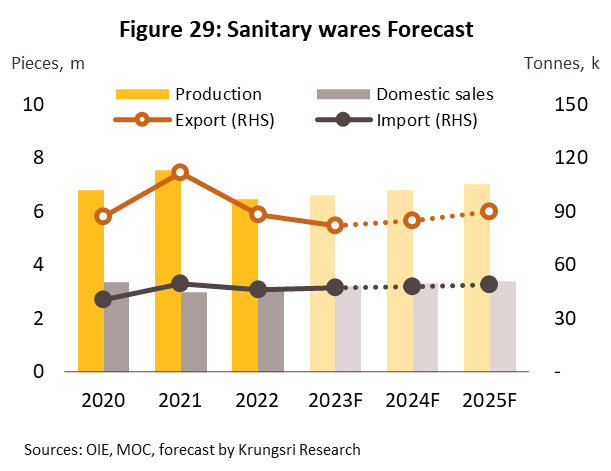
Over the medium term, producers of construction materials will likely invest in the new technology required to produce higher quality goods, especially more environmentally friendly products such as green steel and green (or hydraulic) cement (Figure 30). This will then allow players to better meet what is expected to be rapid growth in the total area of new green buildings under construction (Figure 31). In addition, players will exploit new distribution channels as they develop their ability to respond to more individualized consumer demand from property developers and major construction companies, which may include design services, shortening construction times, and improving building durability. Traders will also look to adjust their operations in light of the changing behavior of modern digital consumers. For their part, this may extend over offering end-to-end services, connecting with consumers through a range of means that mix on- and offline channels (i.e., using omnichannel marketing), and building personalized marketing platforms that take advantage of the opportunities offered by big data analytics. In the long run, as global megatrends unfold and support for the ESG goals strengthens, manufacturers and distributors are expected to form tighter alliances as they look to move their business development onto a more sustainable footing.
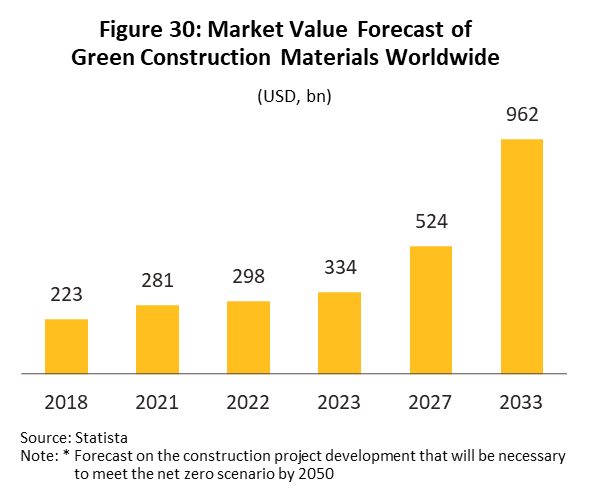
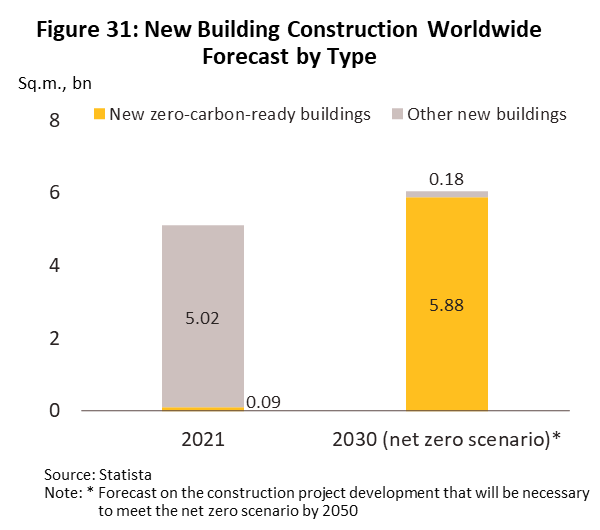
Prices for construction materials will tend to rise over the 3 years from 2023 to 2025 (Figure 32) on: (i) stronger demand from the construction sector, especially in 2024 and 2025; (ii) an expected increase in the price of upstream imports, for example, of scrap and billet, which should rise with stronger global markets; and (iii) energy costs that are predicted to remain elevated due to unresolved geopolitical tensions.
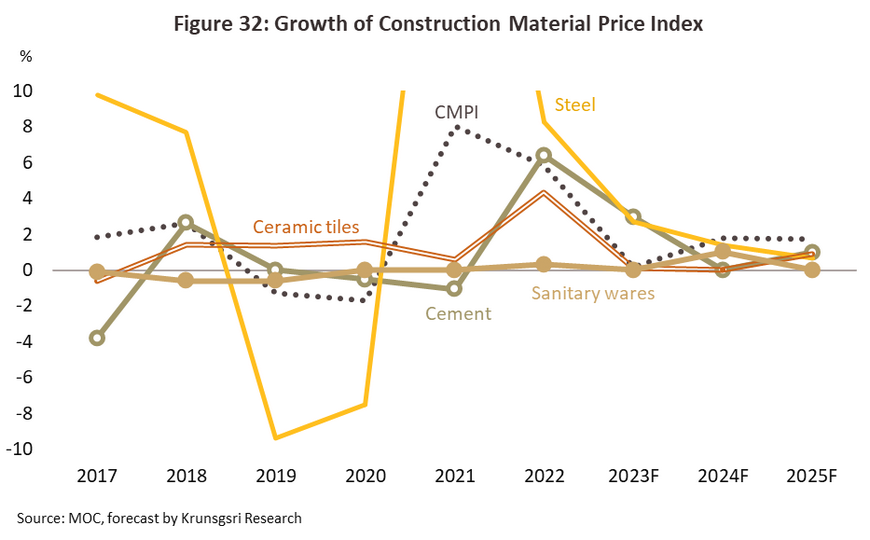
1/This includes only companies registered with the Ministry of Commerce and that have submitted complete accounts for the years 2018-2022.
2/Data from the Office of Industrial Economics on production capacity utilization and domestic consumption and production have been adjusted from 2016 onwards.
3/The move by Thai producers to establish production facilities overseas and then to reimport from there to Thailand has led to a large amount in the import figures.
4/Exports of construction materials include sales of cement, construction steel, ceramic tiles, and ceramic sanitary wares.
5/Materials that are used in place of clinker include limestone (Thailand’s ample supplies of high-quality limestone mean that this is a common domestic option), lime, fly ash, pozzolan (e.g., silica fume, rice husk, and kaolin), and slag sourced from blast furnaces.
6/10 manufacturers of construction materials (cement, construction steel, and ceramic tiles and sanitary wares) that are registered on the Thai stock market.
7/Calculated from 3 companies listed on the Thai stock market and 1 unlisted companies.
8/ 9 companies listed on the Thai stock exchange (financial statements for Lixil for 1Q23 were unavailable so the company was excluded from consideration).
9/ Does not include CRC Thai Watsadu since this is not a listed company and so financial information for 1Q23 was not available.
10/The major greenhouse gases are: carbon dioxide (CO2), methane (CH4), nitrous oxide (N2O), and fluorinated gases, including the hydrofluorocarbons (HFCs), sulfur hexafluoride (SF6), perfluorochemicals (PFCs), nitrogen trifluoride (NF3), and the chlorofluorocarbons (CFCs).
11/In the transition phase (October 2023-31 December 2025) the CBAM will apply to products for which production processes typically result in the release of significant quantities of greenhouse gases, including cement, fertilizer, iron and steel, aluminum, electricity, and hydrogen (added to the scheme later).