Output by the Thai rubber sector is forecast to slide through the period 2019-2021 as producers confront the problem of declining demand in export markets, especially as regards exports to China of sheet rubber and technically specified rubber. The market is expected to face the twin challenges of a persistent oversupply of products and subsequent high levels of stockholding, and pressure from additional supply coming on-stream from new competitors in the CLMV region, where Chinese investors have been establishing new rubber plantations over the past few years. Despite this generally negative outlook, positives will be found in exports of concentrated latex and compound rubber, for which opportunities for growth will exist on world markets. The steadily falling price of rubber, which has now hit low levels, will however, pull down the total value of exports and this will expose producers to the risk of stock losses.
Overview
The natural rubber supply chain in Thailand has three major components. (i) Upstream industries involve the growing and harvesting of rubber on plantations by growers and tappers but to add value to primary production, some producers are now beginning to engage in basic processing of their rubber to produce dried rubber products, such as rubber cup lump, rubber scraps, sheet rubber and crepe rubber. Almost all upstream production in Thailand is consumed as inputs into domestic midstream industries[1]. (ii) Midstream industries, or natural rubber processors, take rubber produced from plantations[2] and convert this into semi-finished products, such as ribbed smoked sheets (RSS), technically specified rubber (TSR), concentrated latex, compound rubber and skim rubber, which variously have the qualities and properties required as inputs to downstream producers in both domestic and international markets. (iii) Downstream producers, or producers of rubber products, include manufacturers of items such as automobile tires, latex gloves, condoms, elastics, rubber shoes, and so on. In some cases, synthetic rubber (SR), which has been developed by the petrochemical sector[3] or for mixing with NR to become more suitable properties for each applications.
Investment in the development of downstream rubber industries in Thailand has unfortunately been only limited in extent, and so 82% of midstream rubber production is exported for additional processing in factories producing end-products abroad. In 2018, the principal buyer of Thai rubber was China, which by value took 42.5% of all exports of Thai midstream rubber production. China was followed in importance by Malaysia (18.8% of exports), Japan (6.1%), the United States (5.6%) and South Korea (3.5%). Of the remainder, the majority (around 18%) was consumed in Thailand as raw materials in the manufacture of tires (60.5% of domestic consumption of Thai-produced midstream rubber), elastic (15.0%), latex gloves (12.2%) and other less important products, such as rubber piping, rubber bedding and elastic bands. (Figure 2)
In 2018, output by Thai midstream players had a total value of approximately THB 0.18 tn. Thanks to domestic upstream producers outputting primarily field latex (92% of output[4]), which can be used as a raw material in all midstream processes, Thai operators have the capacity to produce a wide range of midstream products. This differs from the situation in Malaysia and Indonesia, where primary producers tend to output rubber cup lump and so in these countries, the focus is on the production of TSR.
Thai midstream production is split between that of technically specified rubber, concentrated latex, and sheet rubber. By volume, TSR is the most important and accounts for 42.3% of all midstream output.
- Ribbed smoked sheet (RSS) is produced by first filtering field latex to remove dirt and impurities. This filtered latex is then mixed with concentrated formic acid, which causes the rubber to coagulate and these solids are then rolled into raw sheet rubber before being dried for six hours in the sun to produce air-dried sheets. If these sheets are then smoked or further dried, a process which reduces the moisture content and with it the risk of fungal infection, these are called ‘Ribbed Smoked Sheet’ (RSS). This is a form of dried rubber which can be stored for longer periods of time than can other types.
- Generally, the quality of RSS is graded on a scale from RSS1 to RSS5, with RSS1 the highest quality and RSS5 the lowest. Grading is made according to a variety of criteria, including the number of air bubbles in the product, the proportion of dirt and impurities, its color, the consistency of the material, and so on. Over 80% of Thai output is of RSS3, which has properties equivalent to TSR, and this can be used in the production of tires, belts, hosing, rubber parts for automobiles, and rubber shoes.
- Over more than a decade, world exports of ribbed smoked sheet rubber fell from around 1.5 million tonnes in 2006 to just 1.1 million tonnes in 2017 (latest data). This fall has been precipitated by a turn to the increasing use of technically specified rubber as a replacement for ribbed smoked sheet because quality control of the former is easier and so it is possible to meet higher standards more consistently. The result of this has then been to encourage tire manufacturers to increasingly deploy production technology that uses technically specified rubber as an input, especially in China, where tire production has jumped forward in step with the country’s explosive growth in automobile assembly; between 2006 and 2018, while global output of automobiles grew at an annual rate of 2.4%, China experienced average growth of 11.2% per year.
- In 2018, the value of the market for Thai ribbed smoked sheet (including distribution to both the Thai and export markets) fell to just THB 39 bn following average declines over the previous decade (2008-2018) of -5.9% per year (CAGR). The majority of production (73%) is for export, with the main consumers of this being China (23% of the value of exports of Thai ribbed smoked sheet), Japan (21%) and the United States (14%).
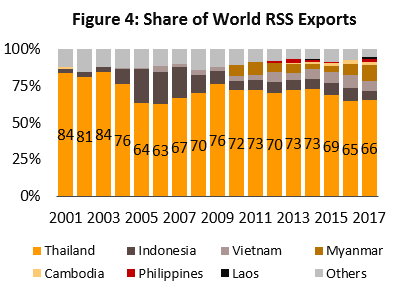
- Technically specified rubber (TSR) or block rubber is made from either field latex or some form of dried rubber such as sheet rubber, cup lump and scrap rubber that is separated into small pieces, washed, dried, and cut into bars. TSR that is produced in Thailand is thus made from one of these materials. (i) Field latex, which forms the basis of 80% of Thai TSR, produces a product with good physical properties (i.e. it has high levels of purity, flexibility and high viscosity) and that is therefore suitable for use in high-performance and quality products such as automobile, radial and aircraft tires. In addition, TSR made from field latex can be used in several types of products such as elastic bands, hair bands, sports goods, rubber parts and so on. Standard of TSR made from field latex is divided into the three grades[5]: STR XL, STR 5L and STR 5, with the majority of Thai TSR production belonging to the last category. (ii) Dried rubber, the remaining 20% of Thai TSR. Its physical properties may be inconsistent and lack uniformity as this type of TSR is made from a number of different rubber inputs. These products are divided into two grades[6]: STR 10 (made from cup lump and high-quality sheet rubber) and STR 20 (made from rubber scraps mixed with raw sheet rubber, cup lump or RSS).
- The technically specified rubber (TSR) segment has a combined value of THB 85 bn (as of 2018). As elsewhere in the sector, production is largely for export 84%. China is again the most important export market, with a 55% share by value of exports of TSR, followed by South Korea (6%), Japan (6%) and the United States (6%). Domestically, tire production accounts for almost all consumption of Thai TSR.
- Concentrated latex is produced from field latex. The latter comes directly from tapping and typically has a rubber content of around only 33% and it usually also has properties which make it unsuitable for use directly in downstream production. It is therefore converted into concentrated latex by high-speed spinning to separate out water, dissolved chemicals and other impurities. The resulting concentrated latex is at least 60% rubber and now has the qualities required for use as a raw material in further processing.
- In 2018, domestic output of concentrated latex had a value of THB 51 bn. 86% of this was exported and much of this went to downstream production of latex gloves and condoms, with 44% by value going to Malaysia and 40% going to China. 14% was used within the country.
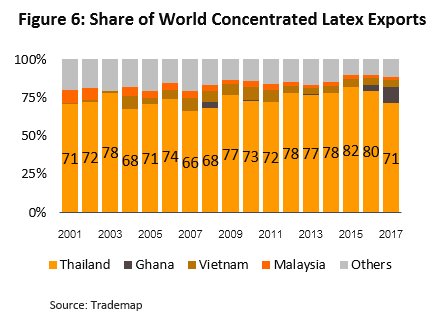
- The other important part of the midstream rubber sector comprises compound rubber products. These are midstream products that mix natural rubber with synthetic rubber and other chemicals such as vulcanite, accelerators, and fillers in order to produce a material that has the special properties required for a particular downstream forming process. Examples of the latter include the manufacture of automobile tires, latex gloves, condoms, rubber bearing pads, hosing and elastic bands. This industry has developed in Thailand as a result of the demands of the Chinese market, which in 2018 took 65% of compound rubber products. Thai producers focus on the manufacture of compound rubber products that are 95% natural rubber.
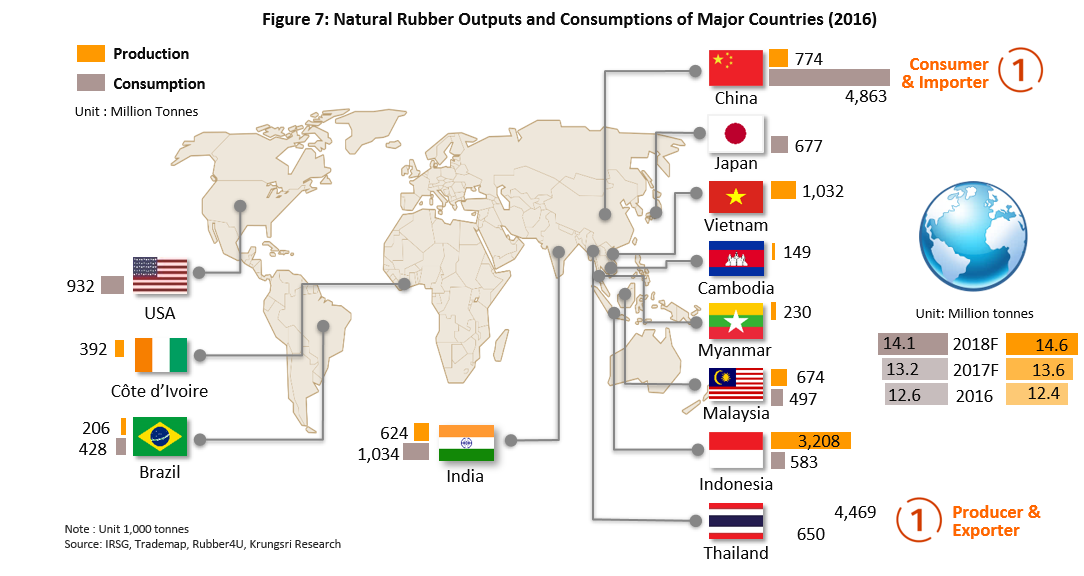
However, the Thai midstream rubber sector’s reliance on exports means that Thai operators are exposed to fluctuations in world economic conditions and to changes in the state of downstream industries in export markets. In addition, because products are dependent on only primary products and have just low levels of product differentiation, Thai midstream producers are subjected to high levels of competition. At the moment, this is coming particularly from other ASEAN countries, especially Indonesia and CLMV, which like Thailand produce a large surplus supply of natural rubber[7] (Figure 7). Despite this, Thailand was the world’s biggest supplier of concentrated latex and RSS in 2017 (latest data), producing 71.2% and 66.9% of global exports, respectively. Thailand was also the source of 24.1% of exports of TSR (2nd world ranking) and 6.7% of exports of compound rubber (5nd world ranking) (Figure 8).
Providing over 90.5% of global supply, Asia is by far the world’s most important source of natural rubber and Thailand is the world’s largest single producer, its output of 4.87 million tonnes representing 33.4% of world production in 2018. Thailand is followed in order of importance by Indonesia, Vietnam, China and Malaysia, which respectively account for 24.7%, 8.5%, 6.4% and 3.8% of global output.
An examination of the markets for Thai midstream operators reveals that exports of TSR, concentrated latex and compound rubber are highly concentrated and so exporters are at an elevated risk of being adversely affected by serious fluctuations in the state of these major export markets; at present, China takes over 56% of Thai exports of TSR and compound rubber, while Malaysia consumes almost 44% of exports of concentrated latex.
In addition, because China is the world’s biggest consumer of rubber (it takes around 30% of world output) and the major export target of Thai midstream operators, China made extensive investments in expanding rubber cultivation in the CLMV (Cambodia, Laos, Myanmar and Vietnam) region between 2006 and 2012. Chinese production of rubber has thus expanded significantly and China now enjoys a much stronger negotiating position in the world market. Indeed, in 2017, the total tapping area of Chinese production (including rubber plantations in the CLMV region) came to 15 million rai, compared to Thailand’s 20 million rai of tapping area[8].
The replacement of natural rubber with synthetic rubber is another factor which has had an influence over the operations of Thai midstream players. Although synthetic rubber cannot be used as an alternative to natural rubber in all applications, because it is able to overcome some of the shortcomings of natural rubber in terms of better tolerating exposure to heat, sun, oil, and chemicals with better controllable standard in quality and production volume consequently, it is used in downstream production slightly more than is natural rubber; in 2018, global natural and synthetic rubbers were consumed in the ratio 45:55. The uniformity, and quality and quantity of production of synthetic rubber is also more easily managed since this is an entirely industrial process (oil products are its primary input) and this allows downstream producers to plan and to control costs better.
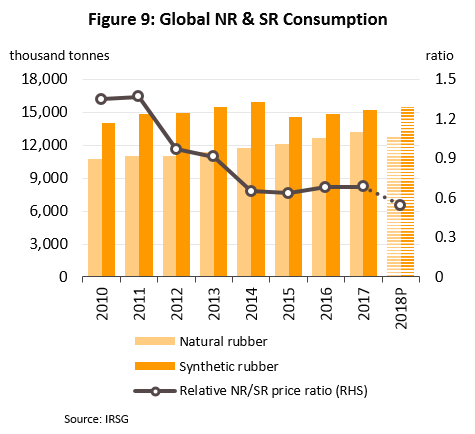
Situation
In the period 2004-2011, the price of rubber rose to historic highs. Two factors were behind this. (i) The tremendous demand for rubber in world markets, especially from China and India, which at this time saw their economies grow quickly and their automobile sectors develop rapidly. (ii) Speculative flows in the global commodity market, due to the high oil prices during this period. Causing the synthetic rubber price (a petrochemical product) to increase as well. Since natural rubber is a replacement for this, this caused increasing demand for natural rubber accordingly. While the cultivation of rubber has not met with the demand, which pushed up the price of rubber.
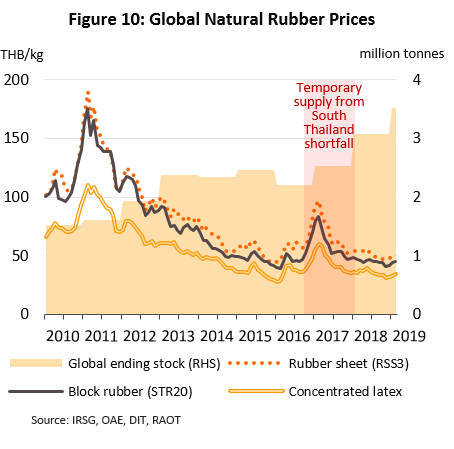
These high prices stimulated an expansion of the rubber plantation areas especially in Asia. Meanwhile, the global consumption has decreased in accordance with the slowing global market conditions. The world rubber industry is constantly facing the continuing over-supply of the market. It is estimated that at the end of 2018, total world stock holdings of rubber came to 3.08 million tonnes and this has put downward pressure on prices. The price of RSS3, which is used as a reference price in the industry, decreased from THB 190.51/kg in February 2011 (the highest price is THB 198.5/kg as of 24 February 2011). But since then prices have slid dramatically, averaging just THB 44-49/kg at the end of 2018. Details are as follows.
- Global supply of natural rubber has increased on an expansion of cultivation of rubber trees in many Asian countries, though especially so in Thailand (as a consequence of the plan to extend the area of national rubber plantations by 1 million rai that was put into effect by the Thai government between 2004 and 2006) and the CLMV nations (as a consequence of Chinese investment in rubber plantations, which added 7 million rai to the area cultivated between 2006 and 2012). Generally, rubber trees open for tapping begin production of latex after 7 years so the expansion of supply began to be felt from 2012 onwards but problems with over-supply accelerated since 2016 as both the total area under tapping and yields (which increases after 3-4 years of tapping) continued to rise. As a consequence, world output of rubber increased from 11.1 million tonnes in 2011 to 14.6 million tonnes in 2018.
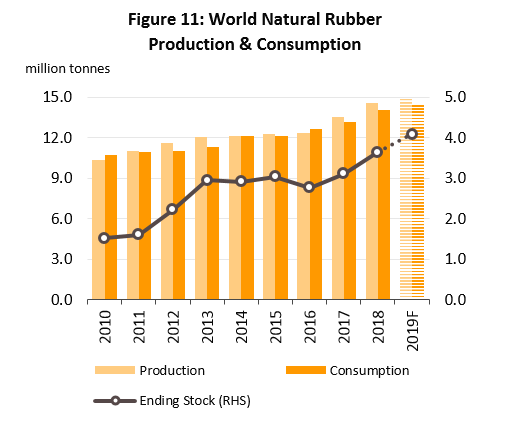
- From 2012, growth in demand for rubber slowed as growth rates in China, the world’s largest consumer of rubber, eased[9]. In addition, synthetic rubber has increasingly been used as a replacement for natural rubber since developments in production technology have enabled downstream producers of tires and latex gloves, which account for 83% of world demand for rubber, to increasingly use synthetic rubber and subsequent changes in the market for rubber products (such as radial tires for passenger car[10] and mixed natural and synthetic rubber gloves[11]) have meant that even as the relative natural rubber/synthetic rubber price ratio has fallen below 1, synthetic rubber is still used in greater amounts than is natural rubber (Figure 9).
- Beyond this, an analysis of the factors determining movements in rubber prices over the past period shows that demand and supply factors within the industry are exerting a greater influence than they did in the past, while the relationship between the prices of oil and rubber is weakening. Analysis shows that the correlation coefficient of the prices of Dubai oil and natural rubber price fell to -0.11 in 2018 from an average of 0.55 and 0.74 during 2015-2017 and 2005-2012 respectively. (Figure 12)
The changing market conditions and declines in prices described above have inevitably had negative consequences for Thai midstream producers over the past few years. For Thai players, income has declined steadily since 2012 while market share in export targets has been lost to new entrants to the sector, particularly those from the CLMV region. This region has benefitted from heavy Chinese investment and this start tapping, as is reflected in the steady fall over the past 3-4 years in both the quantity and market share of exports on world markets of Thai-produced RSS and compound rubber (Figures 13).

In 2018, the domestic rubber industry encountered stiff headwinds that pushed prices to very low levels. On the supply side, rubber production has been increasing, especially in the south of Thailand where conditions returned to a more normal state following the extensive flooding that was seen in 2017, while at the same time, global levels of stock holding have continued to rise. Meanwhile, on the demand side, the China-US trade war is beginning to take its toll and as a result, demand for rubber, in particular from China (Thailand’s most important trade partner), is softening. These negative impacts have depressed prices for rubber, and with production costs currently averaging in the range of THB 56-61/kg, rubber tappers are now having to sell their products at a significant loss, while rubber traders and middlemen are also seeing stock losses. Thus, in December 2018, the price of ribbed smoked sheet 3 (RSS3) realized by farmers fell to THB 36.8/kg (-12.1% YoY), while the export prices of RSS3, TSR and concentrated latex were THB 47.0/kg (-12.0% YoY), THB 42.1/kg (-11.9% YoY) and THB 31.8/kg (-11.1% YoY), respectively. For 2018 as a whole, average export prices of RSS3, TSR and concentrated latex were respectively THB 51.1/kg, THB 45.1/kg and THB 35.4/kg; these prices represent declines of -26.4%, -24.6%, and -22.4% YoY.
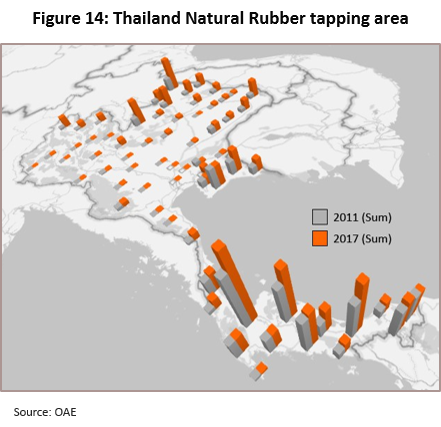
Considered in terms of volume, exports of rubber from Thailand shrank in 2018 by -3.8% YoY to 3.53 million tonnes, while by value, these exports were worth USD 4.602 bn. This figure, though, represents a crash in income of -23.6% YoY that was caused by a steep fall in the average price of rubber, coupled with a strengthening of the baht. Through the year, the sector was badly affected by the softening of demand for rubber on world markets and in particular by contracting demand in China, a major global consumer of rubber, and in the year, Chinese imports of rubber from Thailand slid by 13.9% YoY to 1.50 million tonnes with the value of these imports declining at 32.7% to USD 1.96 bn. China has itself been suffering from high levels of stockholding in rubber that have continued to rise; at the end of 2018, Chinese stocks of rubber climbed to 427,000 tonnes, up from the 383,000 tonnes held at the end of 2017. The situation has also been worsened by the move by Chinese importers to increase their purchases in the CLMV region and the fall in demand that has been triggered by the ongoing Chinese-US trade disagreements, which has cut demand especially for imports of rubber for use in downstream industries, such as in auto assembly and the manufacturing of auto parts. The situation for exports of individual intermediate rubber products is given below.
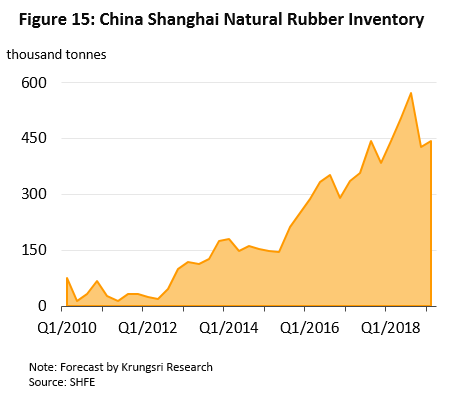
- Ribbed Smoked Sheet: 2018 exports totaled 0.56 million tonnes (-21.3% YoY), bringing in income of USD 899.0 m (-37.3% YoY). Two main factors weighed on the market: (i) purchases from China slid on high levels of stockholding from 2016; and (ii) demand for RSS declined as it is increasingly replaced with TSR as an input in downstream production.
- Technically specified rubber: For 2018, combined exports of TSR came to 1.53 million tonnes, a decline of -3.5% YoY. Exports to China were notably weak for the year due to (i) high levels of stockholding that fed into lower demand and (ii) slowing activity in the Chinese automobile assembly and tire production sectors that was driven by a decline in the number of cars distributed to the Chinese market (down -11.4% YoY to 25.7 million units). Exports of TSR generated income of USD 2.22 bn, a fall of -22.8% YoY on a combination of falling prices and weakening exports.
- Concentrated latex: Exports of concentrated latex increased by 9.5% YoY to 1.30 million tonnes on strengthening demand in China (+18.4% YoY) and Malaysia (+4.3% YoY), countries that are important global producers of latex gloves. However, despite these positive developments, the continuing decline in rubber prices pulled down the concentrated latex export value by -11.3% YoY to USD 1.35 bn.
- Compound latex (95% natural rubber): Exports of compound latex rose in terms of both volume and value. With regard to volume, they increased by 18.9% YoY to 0.18 million tonnes, while by value, exports rose 7.9% YoY to USD 359.3 m. This segment benefited from stronger demand in downstream industries, in particular for rubber wheel production in China (a major trade partner), India and the United States.
Industry Outlook
Over the next 3 years, global output of rubber is forecast to increase by an annual average of 3-6%[12], growing in line with the total area of rubber under cultivation. Through the period 2004-2012, the area given over to rubber plantations steadily rose and production from these is increasingly entering the market. Among these newer plantations, Chinese-backed production in the CLMV countries will have a strong impact on the market as these trees begin to be tapped and yields increase. Over the same period of time, demand for rubber on world markets is expected to grow by 4-5% per year, and the likely gap between supply and demand will lead to an average annual supply glut of 0.35-0.45 million tonnes, which is then expected to lift stockholdings of rubber above 4 million tonnes in 2019-2020. This will then put downward pressure on the prices of rubber on global markets in 2019-2021 and prices are therefore expected to remain flat from the low levels seen at the end of 2018. Thus, export prices for RSS3 should average THB 50-55/kg, compared to production costs of THB 56-60/kg[13].
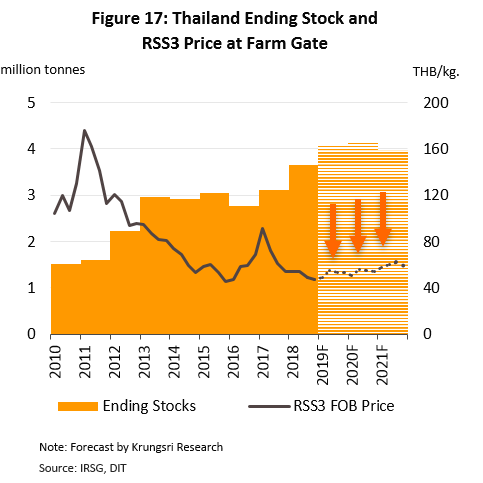
Over the next 3 years, the Thai rubber sector will be exposed to risks arising from a combination of falling demand from trade partners and stiffening competition on global markets. However, for some product groups, the outlook will be somewhat better and growth in downstream industries may support increased demand.
- RSS: Exports of RSS are forecast to decline by 1% to 3% per annum as competition from Chinese production in the CLMV region strengthens. The majority of this production is of cup lump and RSS, and competition with this supply will also push down the prices for Thai exporters.
- TSR: Exports of TSR are likely to decrease 2-5% annually. This is because: (i) tire manufacturers are tending increasingly to use synthetic and compound rubber as raw materials in the production of tires as technology develops and also to follow the standards of the European Union and the United States, which do not use more than 80% natural rubber; (ii) China would increase imports of rubber from CLMV countries.
- Concentrated latex: Exports of concentrated latex should rise by 4-7% per year. Growth will head in the same direction as growth in the output of latex gloves and other medical equipment but concentrated latex is also slowly being displaced by synthetic rubber and cause the demand for latex to grow at a level lower than the growth of rubber gloves production that is expected to grow at an average of 7-9% in the same period. The Malaysian Rubber Manufacturers Association (MARGMA) predicts demand for rubber gloves. Global sales in 2018 will be 246 billion pieces, grow 7.9% YoY and increase to 287 billion pieces by 2020, or an 8.0% CAGR.
- Compound rubber: Producers of compound rubber will be exposed to the risk of fluctuating demand. China, the major market for compound rubber, has changed the rules governing its imports by reducing the proportion of natural rubber that imported compound rubber should contain14/, and this has then pushed Chinese importers to source a greater proportion of their purchases in countries other than Thailand, though it is hoped that secondary markets, such as India and the United States, will still see growth in their imports of Thai goods.
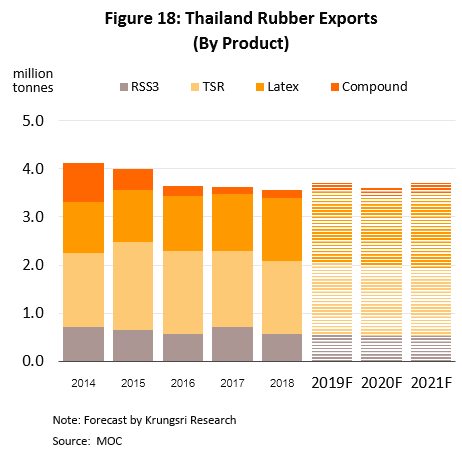
However, on the positive side, demand for rubber from domestic producers will tend to increase following investment in the manufacture of automobiles, tires, auto parts, and medical devices. Thai rubber producers will also benefit from the fact that the medical device sector is one of the government’s targeted industries and so investors in it are eligible to apply for special investment assistance. In addition, the Thai government aims to increase public-sector consumption of rubber. If this policy meets its targets, this will help to ease the sluggishness of the export market.
In terms of operators, investments or seeking trading partners in downstream high value-added rubber production could mitigate risks from fluctuation and intense competition in global markets. Particularly, investment should be embarked in downstream businesses with the government’s support under “Thailand 4.0” policy and the ongoing market growth such as rubber used for medical and healthcare products (e.g. medical gloves, surgical gloves, condom, urinary catheterization, feeding tube, and IV tube), vehicle tires, and aircraft tires.
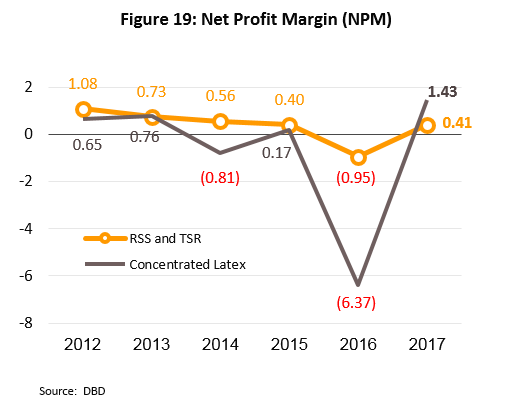
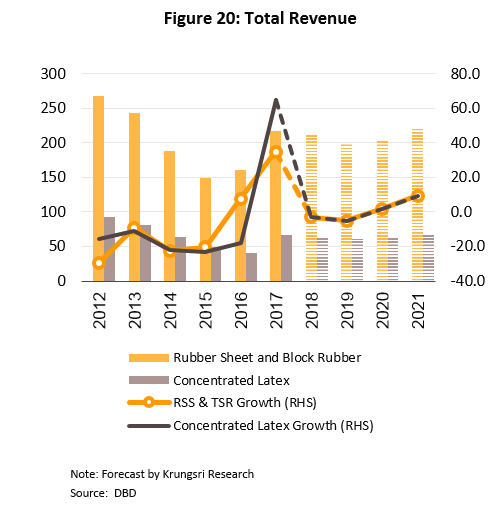
Krungsri Research’s view
Over the 3 years from 2019-2021, producers of midstream rubber products may face the prospect of weakening markets and rising competition, while operators of plantations will likely have to contend with the losses arising from sale prices tending to run below operating costs.
- Producers of midstream rubber products: Players in the market for concentrated latex will see the opportunity to increase their exports thanks to greater demand in downstream industries such as in the production of rubber and medical latex gloves. In addition, players will also benefit from a constrained supply of latex to the market; the fact that the rubber sectors in most countries still emphasize the production of rubber cup lump and rubber pieces that are of low quality and which cannot be used in place of concentrated latex reduces the competition that Thai operators have to face. However, for Thai producers of sheet rubber, technically specified rubber and compound rubber, the outlook is less positive as these players are forecast to experience both falling demand from Chinese buyers and rising competition from new suppliers in the ASEAN region, especially from recent entrants to the market located within the CLMV region. Exports to China by the latter are forecast to grow on, relative to Thai operators, their lower costs, reduced transport overheads and the fact that most of these operations have been established by Chinese investors, and as such, the Thai share of the Chinese market will be steadily eroded. However, more positively, prices for rubber are not forecast to fluctuate sharply and so the risk of future stock losses for operators is reduced.
- Rubber traders: Trends in income over the next 3 years will be somewhat uncertain for this group as the marketing channels available to traders narrow. Downstream industrial consumers are increasingly tending to buy directly from producers, central markets, or cooperatives, while Chinese buyers are also starting to purchase straight from producers, thus cutting out the middleman and reducing the role of Thai traders within the market.
- Rubber growers: This group may face continuing losses despite government efforts to support farmers through measures such as financial assistance for rubber growers, low-interest loans and financial support for the planting of alternative crops. Unfortunately, the costs of production of Thai rubber are typically THB 55-60/kg. and this is somewhat higher than the average forecast prices of THB 43-45/kg. which their product is likely to realize
[1] In 2017, some rubber producers began to work together to process their primary output into crepe rubber by cleaning and pressing rubber cup lump and rubber scraps into sheets. These sheets are then dried through exposure to the sun or by using hot-air dryers to produce principally brown crepe rubber, which is in demand on the Chinese market as an input into the manufacture of TSR. This form of processing has been increasingly practiced by growers in the north and north-east of Thailand, areas which are relatively new to rubber but which have increasingly been producing for the market. This growth is reflected in the fact that in 2018, exports of crepe rubber from Thailand has dropped to 40,000 tonnes from 2017, which has exported 93,000 tonnes, but increased when compared to an average of 10,000-15,000 over the previous 5 years.
[2] Growers may either sell to middlemen or directly to midstream processors.
[3] In the production of synthetic rubber, precursors include butadiene, which is produced from oil. Important types of synthetic rubber include styrene butadiene rubber (SBR), butadiene rubber (BR), ethylene propylene-diene rubber (EPDM), nitrile butadiene rubber (NBR), chloroprene rubber (CR), isoprene rubber (IR), isobutylene isoprene rubber (IIR), and styrene block copolymer (SBC).
[4] Information from the Rubber Research Institute, Department of Agriculture
[5] The standards for Thai rubber produced from field latex are: (i) STR XL, which contains no more than 0.02% impurities and has a color of not more than 4 degrees Lovibond; (ii) STR 5L, which contains no more than 0.04% impurities and has a color of not more than 6 degrees Lovibond; and (iii) STR 5, which also contains no more than 0.04% impurities but which may be of any color and so may be used in any high-quality product that is not highly colored.
[6] Standards for Thai TSR that is manufactured from dried rubber specify grades according to the level of impurities, the initial plasticity, the plasticity retention index, the volatile matter content, and the nitrogen content. Material graded as STR 10 has a higher quality than that marked as STR 20.
[7] Natural rubber consumption in Thailand, Indonesia and Vietnam accounts for only 15-20% of total output in each country. Therefore, excess supply for export is ample.
8] Based on the analysis “Thai Rubber and ASEAN” by Associate Professor Dr. Aat Pisanwanich, Center for International Trade Studies (CITS), University of the Thai Chamber of Commerce.
[9] The growth rate of the Chinese economy has fallen from the double-digit rates recorded during 2003-2007 to 9-10% in 2008-2011, 7-8% in 2012-2014, and 6-7% in 2015-2017.
10] Radial tires are produced with a mix of approximately 40:60 natural and synthetic rubber. These tires give a better ride and also grip the road surface better.
[11] Using synthetic rubber helps to reduce problems with skin allergies reaction or dermatitis caused from natural latex.
[12] In the case of no permanent felling of rubber trees and there is no cooperation in reducing the rubber supply of rubber-producing countries in Asia
[13] Office of Agricultural Economics
[14] China has set new import standard for tires which are mixed by 95% natural rubber and 5% synthetic rubber from up to 88% and 12%, respectively. Entrepreneurs have to invest and take times to change new machines.