The Thai rubber industry can look forward to improving business conditions over the period 2021-2023, during which stronger demand for rubber will be underpinned by growth in downstream industries including tire manufacturing and medical supplies, especially latex gloves. In addition, an acceleration of work on public-sector infrastructure will also boost demand for rubber products for use in the construction sector. However, exports will present a mixed picture. While Thai producers of RSS and TSR will struggle against rising output from the CLMV region, where Chinese players have been investing in both rubber plantations and processing facilities, strong growth in overseas demand for concentrated latex, and compound and mixed rubber will present new opportunities for Thai manufacturers.
Overview
The Thai rubber supply chain has three main components.
(i) Upstream industries involve the growing and harvesting of rubber on plantations by growers and tappers, but to add value to primary production, some producers engage in basic processing of their field latex to produce dried rubber products, such as cup lump, scraps, raw sheet and crepe rubber[1]. Almost all upstream production in Thailand is consumed as inputs into domestic midstream industries.
(ii) Intermediate or midstream industries, or rubber processors, take rubber produced on plantations2/ and convert this into semi-finished products, such as ribbed smoked sheet (RSS), technically specified rubber (TSR), concentrated latex, compound rubber and skim rubber, which variously have the qualities and properties required as inputs to downstream production.
(iii) Downstream producers include manufacturers of items such as automobile tires, latex gloves, condoms, elastics, and so on. Meanwhile, synthetic rubber, which has been developed by the petrochemical sector3/, may be used in place of natural rubber in applications where its qualities make it more suitable.
The lion’s share of Thai-produced intermediate rubber goods is sold on overseas markets for processing into downstream products (as of 2020, 86.7% of Thai intermediate goods were sold abroad). The most important export markets are China (36.6% of all exports of Thai intermediate goods, by value), Malaysia (22.6%), the United States (6.5%), Japan (5.7%) and South Korea (3.4%).
The remaining 13.3% of midstream production is consumed domestically. The most important end-use is for the production of tires (48.9% of domestic demand for intermediate rubber products), followed by elastics (19.7%), latex gloves (13.0%) and then other products such as hosing, condoms and rubber bands (Box 1).
In 2020, the total value of intermediate rubber production in Thailand came to around THB140bn, including goods sold on both domestic and export markets. Thailand is in the fortunate position of its production being overwhelmingly of fresh rubber (92% of upstream production is of fresh latex rubber[4]) and because this can be used as an input for processing into all types of midstream rubber goods, Thai intermediate rubber production is very diversified. This differs from the situation in Malaysia and Indonesia, where most upstream production is of cup lump, which is largely used for conversion into TSR.
Given this, the output from Thai intermediate rubber production encompasses RSS, TSR, concentrated latex and other products, though of these, TSR is the most important, accounting by quantity for 30.5% of all production.
Ribbed smoked sheet (RSS) is produced by first filtering field latex to remove dirt and impurities. This filtered latex is then mixed with concentrated formic acid, which causes the rubber to coagulate and these solids are then rolled into raw sheet rubber before being dried for six hours in the sun to produce air-dried sheets. If these sheets are then smoked or further dried, a process which reduces the moisture content and with it the risk of fungal infection, these are called ‘ribbed smoked sheet’. The resulting dried sheets can be stored for longer periods of time than can other types of rubber.
- Ribbed smoked sheet is graded according to its quality on a 6-point scale that goes from 1X (the best) and then from 1 to 5 (the worst). Grading is made according to a variety of criteria, including the number of air bubbles in the product, the proportion of dirt and impurities, its color, the consistency of the material, and so on. Over 90% of Thai output is of grade 3 RSS, a standard quality that has properties equivalent to TSR, and this can be used in the production of tires, belts, hosing, rubber auto parts, and rubber shoes.
- Over the past decade, demand for RSS has softened, and global exports have slipped from 1.7 million tonnes in 2010 to just 1.3 million tonnes in 2020. This has been at least partly driven by the fact that because quality control is more certain with technically specified rubber, tire manufacturers have increasingly been using TSR in preference to RSS. This has been especially true for Chinese tire producers, where growth has outpaced the rest of the world.
- The value of the Thai RSS segment has likewise dropped, crashing from THB83bn in 2010 (combined distribution to domestic and export markets) to THB27bn in 2020, or an average annual decline of 10.7% (CAGR). In this period, exports, which represented up to 81.2% of the value of all sales, declined by 11.4% per year, but despite this, Thailand remains the world-leader in this segment (Figure 2). At present, the most important export markets are Japan (23.9% of all exports of RSS from Thailand, by volume), the US (16.1%) and China (15.4%) (Box 1).

Technically specified rubber (TSR) is made from either field latex or some form of dried rubber such as sheet rubber, rubber cup and scrap rubber that is separated into small pieces, washed, dried, and cut into bars.
TSR that is produced in Thailand is typically made from one of the two following materials. (i) Field latex produces a product with good physical properties (i.e., it has the preferred levels of purity, viscosity and flexibility) and that is therefore suitable for use in manufacturing high-quality goods such as radial and aircraft tires. In addition, TSR is also used to manufacture products such as elastic bands, hair bands, sports goods, and different types of parts. Standard Thai rubber is divided into the three grades[5] of STR XL, STR 5L and STR 5, with the majority of Thai export product belonging to STR 5L
(ii) TSR that is made from dried rubber may be inconsistent and lack uniformity as the manufacturing process involves using and mixing different rubber inputs. These products are divided into two grades[6]: STR 20 (made from rubber scraps mixed with smoked sheet rubber, rubber cup or RSS) and STR 10 (made from rubber cup and high-quality raw sheet rubber). Most Thai TSR made from dried rubber is of the former type, which is then consumed by downstream tire manufacturers
- In total, the value of the Thai TSR market is worth THB60bn in 2020 (combined distribution to domestic and export markets). 82.8% of this was sold on overseas markets, putting Thailand in second place after Indonesia in the ranking of suppliers to the world market (Figure 3). Thailand’s main export markets are China (which takes 47.9% of Thai-made TSR by quantity), the United States (8.5%) and South Korea (5.9%). Almost all TSR sold on the domestic market is used in the manufacture of tires (Box 1).
Concentrated latex is produced from field latex by using high-speed centrifuges to separate out water and other impurities. The resulting concentrated latex is at least 60% of rubber content and now has the qualities required for use as a raw material in further processing (generally, field latex is no more than 33% of rubber content, making it unsuitable for midstream processing).
- The value of Thai concentrated latex amounted to THB50bn in 2020 (combined distribution to domestic and export markets). 75.9% of this went to overseas buyers, and with almost 70% of global supply, Thailand is comfortably the world-leader (Figure 4). Malaysia is the most important export target, taking around half of Thai concentrated latex, followed by China (33.5%) and South Korea (1.8%) (Box 1). Most concentrated latex sold on export markets is used in the manufacture of latex gloves and condoms.
Other important parts of the midstream rubber industry include compound rubber and mixed rubber. These midstream products mix natural and synthetic rubber with other chemicals such as vulcanite, catalysts, and fillers in order to produce a material that has the special properties required for a particular downstream forming process. Examples of the latter include the manufacture of tires, latex gloves, rubber bearing pads, hosing and elastic ties.
- The value of Thai compound and mixed rubber is worth THB7.5bn. 99.0% of output is distributed on export markets. After South Korea, Thailand is the world’s second most important source of compound and mixed rubber (Figure 5), though Thai production is overwhelmingly for the Chinese market, which soaked up 87.9% of output in 2020 (Box 1). Thai-made compound and mixed rubber is generally 80-95% of natural rubber content, though the exact proportion will depend on where the rubber is being sent and what final uses it will be put to.
However, the Thai rubber sector’s reliance on exports means that midstream Thai operators have to manage a high degree of exposure to changes in the health of the global economy and in the state of downstream industries in export markets. Moreover, because products are generally dependent on only simple production methods and have low levels of product differentiation, Thai players are subjected to high levels of competition in a market that is also currently awash with surplus production. In 2020, global supply came to 12.9 million tonnes. 38.2% of this, or 4.4. million tonnes, came from Thailand, which remains the world’s most important source of rubber. Thailand is followed in importance by Indonesia, Vietnam, China, Malaysia and India (Figure 6), and indeed overall, Asia is the source of a full 93% of the world’s rubber. Thailand’s main competitors are thus other ASEAN producers, and in particular, Indonesia, Malaysia and the CLMV group (Cambodia, Laos, Myanmar and Vietnam) (Figure 7), all of which like Thailand are suffering from a supply glut[7]. Nevertheless, despite these rising threats to its dominance,
the Thai intermediate rubber industry has retained its place as the world leader, and it is still the number one supplier to global markets of concentrated latex and RSS.
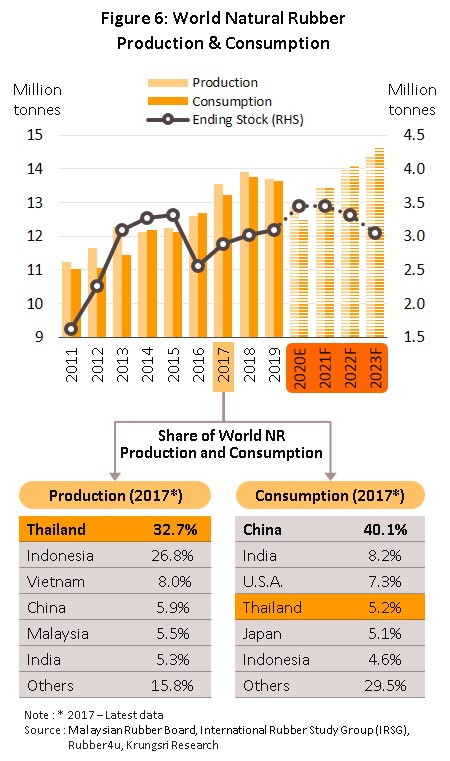
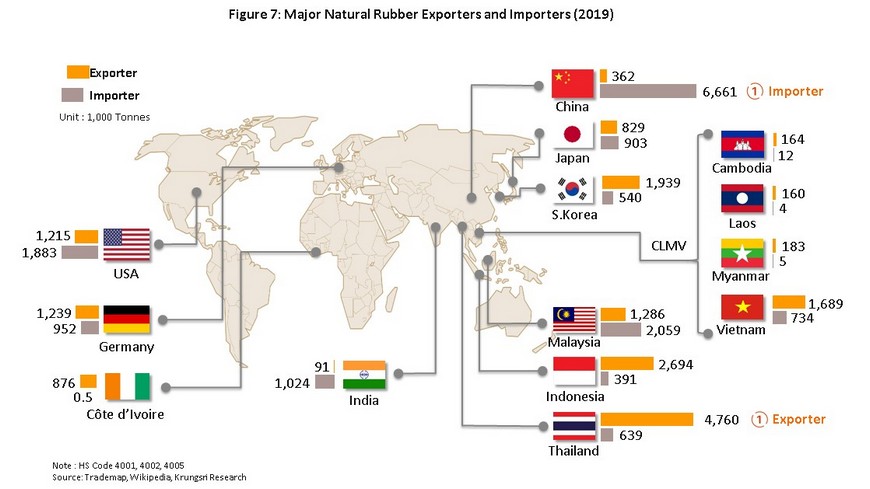
Global demand for rubber products totaled 12.5 million tonnes in 2020. The most important market for rubber is China, which in the year accounted for 40.1% of global consumption and 23.2% of global imports, followed by India, the United States, Japan, Indonesia, Malaysia and the European Union (Figure 6 and 7). Because of the way the market is structured, Thai exporters tend to be reliant on demand from a small number of countries that are major consumers. In 2020, 36.6% by value of exports of all Thai rubber products went to China and another 22.6% went to Malaysia. This clustering of demand is especially noticeable in the TSR segment, where 47.9% of exports went to China, and for concentrated latex, where 49.9% of overseas sales were made in Malaysia and another 33.5% were made in China. This degree of concentration then leaves the industry highly exposed to the risk of changes in the economic outlook in these export markets.
In addition, Chinese investors ploughed funds into developing rubber plantations in the CLMV region between 2006 and 2012, and this is now translating into a steady expansion in supply. As a result, Thailand is losing market share to these countries, and this is being replaced by the rising contribution of CLMV exports to world supply (Figure 2), while simultaneously,
China is producing more rubber products and so its bargaining position on world markets is rising relative to suppliers.
The use of synthetic rubber is another growing threat to the Thai intermediate rubber industry. Although it is not possible to substitute synthetic for natural rubber in all applications, synthetic rubber is now used slightly more than natural rubber in midstream production (in 2020, inputs were split 48:52 between natural and synthetic rubber) (Figure 8). The rising importance of synthetic rubber stems from the fact that it can overcome many of the weaknesses of its natural counterpart, including greater tolerance of heat, light, oil and chemicals. In addition, because synthetic rubber is an industrial product (it is derived from oil), the manufacturing process is easier to control and the final product displays a much greater uniformity than does natural rubber, which is subject to all the vagaries of biological systems. Using synthetic rubber in industrial applications thus makes it easier for midstream producers to plan and to control production costs.
Overview
Over the years 2004 to 2011, the price of rubber rose to historic highs (Figure 9) on a combination of two factors. (i) Global demand for rubber rose sharply through this period, especially from China and India, which at this time saw their economies grow quickly and their automobile sectors develop rapidly. (ii) Strong speculative pressure inflated commodity prices during the years following the new millennium, and with this, oil prices rose to record highs. Because synthetic rubber is produced from petrochemical inputs, its production costs rose, stoking stronger demand for natural rubber as a replacement. However, because there is a lengthy lead time between planting rubber trees and being able to harvest them, prices for natural rubber rose through this period,
adding to the incentives to expand rubber plantations, especially in Asia.
Following this boom period, though, demand slackened substantially and world commodity markets deflated as speculative pressure had faded, leaving global stocks of rubber at around 3.0-3.1 million tonnes at the end of 2018-2019. Naturally, this weighed on prices, and those for RSS3 (an industry reference price) slumped from an average of THB190.51/kilogram in February 2011 (the highest price was set on 24 February 2011, at THB 198.5/kilogram) to an average of just THB50-52/kilogram in 2018-2019, even as average production costs ran in the range of THB56-61/kilogram. Details of this turbulent market history are given below.
- The supply of natural rubber increased strongly from 2012, driven by the earlier expansion in plantations that had taken place across Asia, though especially in Thailand[8] and the CLMV nations[9], and this extra production then flooded world markets[10]. Because rubber yields tend to step up a level after the first 3-4 years of tapping, global supply increased strongly in 2016, and from 11.2 million tonnes in 2011, total supply rose to 13.7 million tonnes in 2019. Much of this increase went into stockholdings, and worldwide these rose from 1.6 to 3.1 million tonnes. For Thailand, total supply climbed from 3.6 to 4.7 million tonnes and stocks doubled from 0.4 to 0.8 million tonnes (Figure 10).
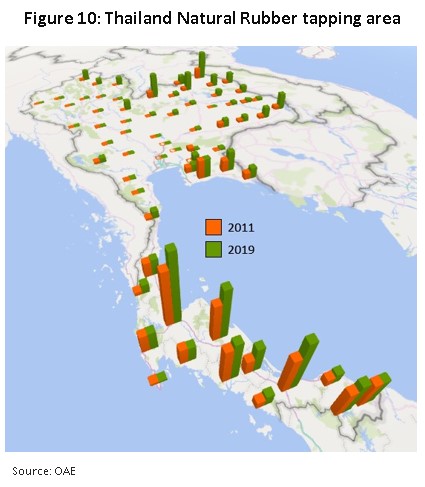
- At the same time as supply was expanding, demand growth went into reverse, premised on the following factors. (i) Overall economic growth in China (the world’s largest market for rubber products) continued to slow down[11]. (ii) The substitution of natural with synthetic rubber increased following the development of new techniques by tire manufacturers[12] (a major player in downstream rubber consumption) that improved the use of synthetic rubber and made it suitable for use with, for example, radial car tires[13] and mixed-rubber gloves[14]. Indeed, although at some times the relative natural rubber/synthetic rubber price ratio was less than 1, in terms of quantities used, synthetic rubber has continued to outperform natural products (Figure 8). (iii) The long-running US-China trade conflict has had knock-on effects on demand for rubber for use in industry, especially in the global auto and auto parts industries through 2019. (iv) China’s stock holdings of rubber have been accumulating, and these reached 0.48 million tonnes in October 2019 (Figure 11), while China has also switched to importing a greater share of its rubber from the CLMV group, thus eroding demand for Thai rubber from what has been the country’s main customer.
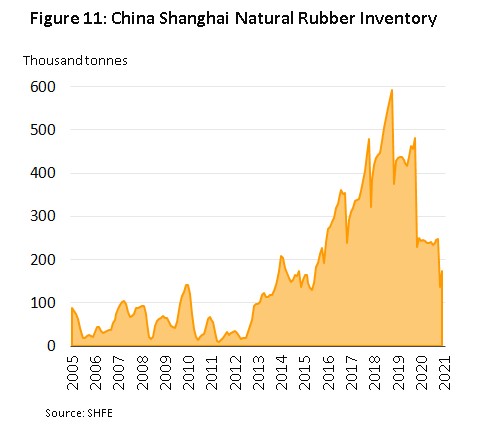
- Research into the factors affecting price movements of natural rubber shows that this is driven principally by changes in supply and demand within the global rubber industry, rather than changes in the price of oil, although in the past this had a much greater impact. Thus, the correlation coefficient between prices for Dubai crude and the average monthly price for natural rubber dropped to -0.13 in 2018, compared to 0.74 in 2005-2012 and 0.61 in 2012-2017 (Figure 12).
The changes to the market described above have resulted in Thai players in intermediate rubber production seeing a significant turnaround in their fortunes, and between 2011 and 2019, revenue for the Thai rubber industry crashed from THB430bn to just THB160bn. Competition has also been intensifying and new supply has steadily eroded Thailand’s market share, especially as yields from Chinese-backed plantations in the CLMV region have begun to rise. Thailand’s share of world markets for RSS has thus been sliding for the last 7 years (Figure 13).
In 2020, global output of intermediate rubber products totaled 12.9 million tonnes, falling 5.9% on a combination of extreme weather, serious outbreaks of leaf fall disease across Asia[15] (the primary area of rubber production), and labor shortages precipitated by the COVID-19 pandemic.
At the same time, worldwide demand shrunk 8.1% to 12.5 million tonnes as the global economy slid into recession, though this was particularly driven by the contraction in the auto industry; the International Rubber Study Group (IRSG) estimates that in 2020, global demand for rubber from automotive industry softened by 10.2%.
Thai production moved with global trends, and 2020 output of intermediate rubber goods declined 6.71% to 4.42 million tonnes. Production fell in all product groups due to: (i) outbreaks of leaf fall disease in the South; (ii) drought at the start of 2020 and then heavy rainfall that reduced supply; and (iii) the strict controls on cross-border travel that were implemented in response to COVID-19 and which then made it very difficult to recruit the migrant laborers who usually work in rubber plantations.
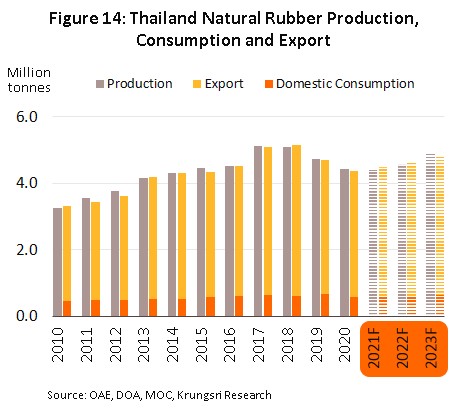
Domestic demand also weakened in 2020, falling 12.3% to 0.58 million tonnes[16] on the general slowing of the economy caused by the COVID-19 pandemic and the temporary closure of production lines in downstream industries, especially the automotive industry. Exports of intermediate goods likewise worsened in the year, dropping 4.4% YoY to 4.6 million tonnes[17] and generating receipts of USD6.2bn (-5.5%). Declines were recorded in almost all markets, though in the main market of China, growth was sustained by: (i) an expansion in demand from tire manufacturers, which was itself supported by Chinese government policy that encouraged rural consumers to buy new vehicles (through part-exchange programs) as part of a drive to boost domestic consumption and to tackle problems with pollution by increasing sales of EVs; and (ii) a rapid fall in Chinese stocks of rubber, which shrank to just 0.17 million tonnes in December 2020, stoking stronger demand for imports of rubber for use in the automotive industry. However, a shortage of shipping containers and COVID-19-driven delays in shipments weighed on exports to China, and these rose by just 2.7% in the year. Exports of concentrated latex to Malaysia also rose slightly by 1.5% on greater demand for the production of surgical gloves and other medical equipment that was needed in the global fight against COVID-19.
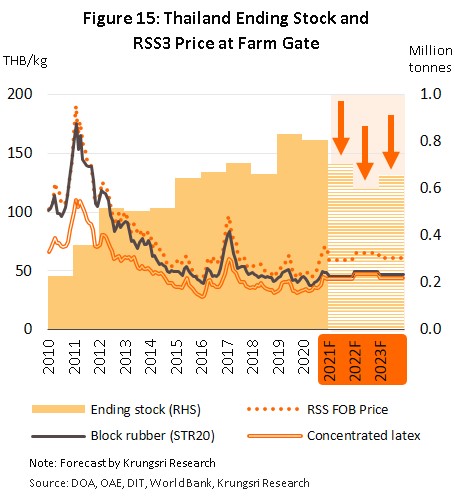
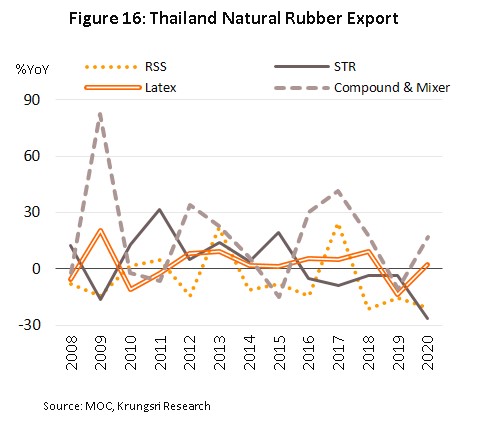
Details of 2020 exports of Thai midstream rubber products are given below.
- Ribbed smoked sheet: Exports crashed 20.8% to 0.38 million tonnes, generating receipts of USD649.6m (-14.6%). This was a consequence of: (i) the slowing global economy and the effects of this on demand; (ii) stiffening competition that is eating into Thailand’s market share, especially from the CLMV zone; and (iii) substitution of RSS with TSR and compound and mixed rubber. However, falling world output led to a rise in average export prices and these rose 7.8% to USD1,728.0/tonne.
- Technically specified rubber: Exports dropped 26.1% to 1.09 million tonnes, which brought in USD1,550.8m for Thai producers (-28.3%). The worsening market was driven by a slowdown in downstream industries, though a fall in demand from tire manufacturers was particularly important. This then undercut export prices, which in 2020 fell 3.0% to USD1,419.3/tonne.
- Concentrated latex: Exports strengthened 2.4% in 2020, rising to 1.15 million tonnes and generating revenue of USD1,275.3m (+11.0%). Export growth was driven by much stronger demand for latex gloves and other types of medical supplies that were used in huge quantities as countries struggled against the COVID-19 pandemic. Exports to Malaysia were especially strong in the year, rising 10.6% thanks to the country’s position as a major supplier of latex gloves to world markets, though exports of latex gloves from Thailand also jumped 34.8% YoY to the historic high of 24.9 million tonnes (Figure 17). Expectations of continuing strong demand for surgical gloves also encouraged manufacturers to invest in an expansion in production capacity. In 2020, strong demand helped to boost export prices, which averaged USD1,110.3/tonne (+8.4%).
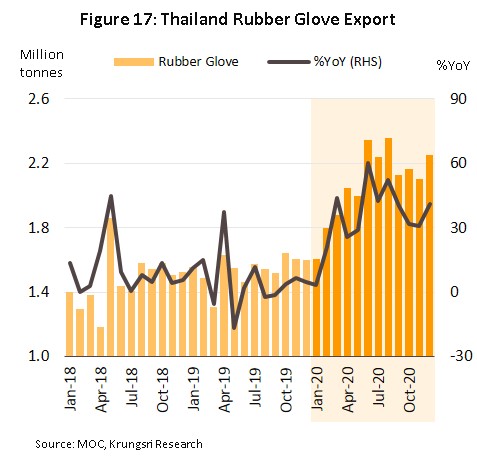
- Compound and mixed rubber: Exports jumped 17.2% to 1.9 million tonnes on stronger demand from downstream industries, especially Chinese tire manufacturers. Receipts for this segment rose 10.6% to USD2.7bn, despite a 5.6% fall in average export prices to USD1,417.2/tonne. The latter was caused by a drop in the price of factice synthetic rubber[18], which was in turn driven by a 33.3% drop in prices for crude oil.
Outlook
Over the next three years, global rubber outputs are forecast to rise by an annual average of 3.0-4.0%[19], supported by: (i) the expansion in the area given over to rubber plantations that occurred in the period 2004-2012, which will increase both total outputs and yields per rai as trees mature; (ii) weather that is expected to be more favorable to rubber cultivation; (iii) stronger prices for rubber, which will be lifted by rising demand from downstream industries; and (iv) support for agriculture industries in a number of countries, which will incentivize farmers to increase outputs.
Simultaneously, demand for intermediate rubber products on world markets is expected to strengthen by 5.0-6.0% per year as economies and rubber-consuming industries rebound in the aftermath of COVID-19. The more rapid growth in demand than supply will cause a fall in stocks, and so these are forecast to shrink to 3.0 million tonnes by 2023 from 3.4 million tonnes in 2020 (Figure 18). This will also then affect prices, and over 2021-2023, the price for RSS3 set on world markets is expected to rise to USD1,680-1,800/tonne, compared to USD1,620/tonne in 2020.
The Thai rubber industry will see better business conditions over the period 2021-2023, and domestic demand is expected to expand by 3.5-4.5% per year on a number of different factors. (i) Demand from downstream industrial consumers will rise, especially for use in auto assembly and the manufacture of auto parts, tires, and latex gloves and other medical supplies. (ii) Consumption of rubber in other high-value industries, such as beauty products, will also strengthen. (iii) Progress on the build out of public-sector infrastructure projects will support stronger demand from the construction sector. (iv) Government support for the industry will lead to higher spending by the public sector on rubber for use in, for example, dam construction, road surfacing, and the production of traffic control and road safety fixtures.
Exports are also forecast to increase by 3.0-4.0% annually. (i) Once vaccination programs have had widespread results, the COVID-19 pandemic will abate and with this, economies will rebound to growth, boosting activity in downstream industries, though an improving outlook for auto assembly will be particularly important. (ii) Growth in demand for medical equipment (especially latex gloves and other types of personal protective equipment) will likely continue. (iii) Outputs in Indonesia and Malaysia will suffer as a consequence of outbreaks of leaf fall disease. Given these influences on the market, export prices for RSS3 are forecast to strengthen, rising from THB54.7/kilogram in 2020 to an average of THB60-65/kilogram by 2023, against production costs of THB56-60/kilogram[20]. The outlook for exports of individual product groups is given below (Figure 19 and 20).
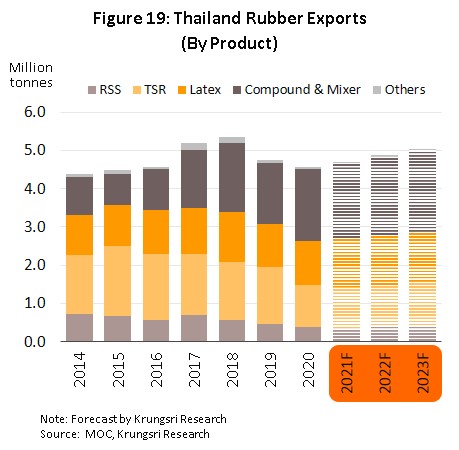
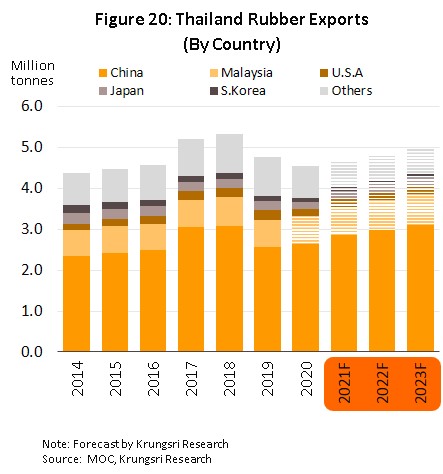
- Ribbed smoked sheet: Exports of RSS are forecast to return to growth of 1.0-2.0% per year thanks to the widespread acceptance on world markets of Thai RSS’s high-quality, and improving business conditions in downstream industries. Nevertheless, Thai exporters of RSS will see only anemic levels of growth due to stiffer competition from both established rubber producing nations (Indonesia, Malaysia and Vietnam) and new entrants to the market that are closer to home (Cambodia, Lao PDR and Myanmar), most of which produce low-cost cup lump and RSS.
- Technically specified rubber: Exports are expected to increase by an annual average of 1.5-2.5%, again on recovery in the economy and in downstream industries, most importantly in auto assembly and the manufacture of auto parts and tires. This outlook may be boosted by fears over the spread of COVID-19 and by habits developed during the enforcement of social distancing becoming a much more established ‘new normal’ that then encourages a greater dependency on private transport. Indeed, IHS Markit forecasts a strong boost in sales of autos in the near future, with these expected to rise by 9.0% in 2021 and then by 4.2% and 3.2% in each of 2022 and 2023.
- Concentrated latex: Exports is forecast to rise by 5.0-8.0% per year, and this will be driven principally by increasing production of latex gloves and other medical supplies. The main market for Thai exporters will remain Malaysia, which will in turn keep its place as the world’s biggest supplier of latex gloves. The Malaysian Rubber Glove Manufacturers Association (MARGMA) predicts that world demand for latex gloves will grow by 23.1% (CAGR) over the next 3 years, with the world consuming 662 billion latex gloves by 2023.
- Compound and mixed rubber: Exports should perform reasonably well, and the segment should see annual growth of 3.0-4.0% on stronger demand from China (Thai exporters’ main market) for use in the manufacturing of tires and auto parts that will be linked to China’s encouragement of greater vehicle ownership, for example by allowing rural residents to part-exchange old vehicles for new ones and providing support for the production of EVs. However, exports to China should see limited growth, capped by increasing Chinese investment in the production of compound and mixed rubber.
Krungsri Research’s view
Taken as a whole, the Thai intermediate rubber industry will see earning improve over the period 2021-2023, but competition from neighboring countries will be intense and although rubber growers will see positive price signals in the market, they will need to be careful about the possible impacts of disease on outputs.
- Producers of intermediate products: Manufacturers of RSS and TSR will be exposed to the twin risks of softening demand from China and rising competition from new entrants to the market, especially the CLMV countries, which will tend to increase exports to China (CLMV-based producers benefit from lower costs for production and transport, and most recent investment has been made by Chinese players). As such, any improvement in earning for players in this segment will be limited. The outlook for producers of concentrated latex is rather better, and these players can look forward to opportunities for ongoing growth thanks to anticipated increases in demand from downstream manufacturers of latex gloves, medical supplies and condoms. In addition, supply is somewhat limited as manufacturers tend to produce cup lump and rubber scraps, rather than concentrated latex, and so competition in export markets is not unduly intense. Producers of compound and mixed rubber will also benefit from an improving business environment that will benefit from rising demand from Chinese auto assembly and auto parts manufacturers. However, investment in domestically produced compound rubber is rising in China, and because this is the major market for Thai exporters, room for growth may be limited.
- Rubber traders: Revenue will be uncertain for this group because distribution channels are narrowing as midstream processors increasingly buy directly from growers, central markets and cooperatives. In addition, Chinese operators are increasingly traveling to Thailand to buy from rubber farmers directly, and this too may help to cut Thai traders out of the loop.
- Rubber growers: Revenue should rise for farmers, supported by the effects of outbreaks of leaf fall disease and widespread drought on stocks both in Thailand and globally. Demand will also strengthen on domestic and export markets, and this will lift the prices that growers are able to realize for their products. In addition, this will be helped by government assistance for the industry in the form of income guarantee schemes and grants for rubber growers, low-interest loans and financial support for the planting of alternative crops. However, growers may also have to face a cut in outputs caused by leaf fall disease, and any further outbreaks will thus eat into farmers’ revenues.
[1] Crepe rubber is made by cleaning rubber cup lump and rubber scraps and then rolling this into sheets that are dried through exposure to the sun or by using hot-air dryers. The resulting sheets are called brown crepe rubber. This form of processing has been increasingly practiced by growers in the north and north-east of Thailand, areas that are relatively new to rubber-growing but which have been increasingly important suppliers of the market.
[2] Rubber farmers may sell either to middlemen or directly to midstream processors.
[3] Precursors used in the production of synthetic rubber include butadiene, which is produced from oil. Important types of synthetic rubber include styrene butadiene rubber (SBR), butadiene rubber (BR), ethylene propylene-diene rubber (EPDM), nitrile butadiene rubber (NBR), chloroprene rubber (CR), isoprene rubber (IR), isobutylene isoprene rubber (IIR), and styrenic block copolymer (SBC). [4] Source: Rubber Research Institute, Department of Agriculture
[5] The standards for Thai TSR produced from field latex are: (i) STR XL, which contains no more than 0.02% impurities and has a color of not more than 4 degrees Lovibond; (ii) STR 5L, which contains no more than 0.04% impurities and has a color of not more than 6 degrees Lovibond; and (iii) STR 5, which also contains no more than 0.04% impurities but which may be of any color and so may be used in any high-quality product that is not highly colored.
[6] Standards for Thai TSR that is manufactured from dried rubber specify grades according to the dirt content, the initial plasticity (Po), the plasticity retention index (PRI), the volatile matter content, and the nitrogen content. (i) STR 20 should have dirt content no greater than 0.16% and Po and PRI values of no more than 30 and 40, respectively. (ii) STR 10 should have a dirt content no higher than 0.08% and Po and PRI values that are no higher than 30 and 50 each. Thus, material graded as STR 10 is of higher quality than that marked as STR 20. In addition, there is also STR 10 CV and STR 20 CV, with the CV standing for ‘constant viscosity’. This type of rubber has been modified through the addition of chemicals that control the rubber’s viscosity, thus making it easier (and less energy-intensive) to cut, mix, and heat (source: Rubber Research Institute, Department of Agriculture).
[7] Thailand, Indonesia and Vietnam consume only around 15-20% of their rubber output domestically (average for 2016-2020), and as such, a supply glut has steadily built up on export markets (source: Trademap, Rubber4u, Krungsri Research).
[8] A consequence of government policy to boost the area of rubber plantations by 1 million rai that ran from 2004-2006.
[9] Between 2006 and 2012, Chinese players invested in expanding rubber plantations by more than 7 million rai.
[10] It usually becomes possible to begin tapping rubber trees after 7 years.
[11] The growth rate of the Chinese economy has fallen from the double-digit rates recorded during 2003-2007 to 9-10% in 2008-2011, 7-8% in 2012-2014, and 6-7% in 2015-2017.
[12] Tire manufacturing consumes 75% of all natural rubber produced globally.
[13] Radial tires are produced with a mix of approximately 60:40 synthetic and natural rubber. These tires give a better ride and also grip the road surface more firmly.
[14] Mixing in synthetic with natural rubber helps to reduce problems with allergies to latex.
[15] Includes Indonesia, Malaysia, India, Sri Lanka and Thailand.
[16] Calculated as dry rubber content (DRC) only, and so does not include water or any other added chemicals.
[17] Based on the weight assessed for customs and excise duties. Considered on a dry rubber content basis, this would be approximately 3.8 million tonnes, assuming that the average DRC of concentrated latex is 60% while that of compound and mixed rubber is in the range 80%-95%.
[18] Factice is mixed with other products when manufacturing tires to help additives and chemicals disperse more evenly, to control the thickness and coverage of extruded products (i.e., their calendaring), to reduce imperfections (i.e., calendar grain), to prevent shrinkage, to reduce blooms on the surface of rubber products from oil and sulfur, and to reduce die swell.
[19] Assuming that there is no widespread clearing of plantations and the main Asian producers make no concerted joint effort to reduce supply.
[20] Source: Office of Agricultural Economics