EXECUTIVE SUMMARY
Periodic chip shortages have continued to drag on auto supply chains, in particular on the OEM market. The Thai auto parts industry thus grew at a slower pace through 2022. At the same time, the business environment has been made more difficult by a steep uptick in inflationary pressures that has eroded consumer spending power in domestic and international markets. The situation will remain somewhat unfavorable through 2023 and a combination of a global slowdown, which will adversely affect consumer demand, and a continuation of US-China tensions, which are impacting chip production, will mean that auto parts manufacturers will see only sluggish growth in the year. However, conditions should improve in 2024 and 2025, as major chip manufacturers expand their capacity, and the global economic outlook steadily improves. Also, on the positive side, the REM market will continue to grow with the expansion in the national vehicle fleet and the desire by some owners to defer purchases of new vehicles by making more extensive repairs to those currently on the road. Challenges in the coming period will include (i) the introduction of anti-dumping measures by the US government that target Thai tire exports, and (ii) the Thai government’s promotion of zero emission vehicles, which will bring with it extremely wide-reaching changes for the industry.
Krungsri Research view
Auto parts manufacturers will see income continue to rise through 2023, though global economic weakness and persistent problems with chip shortages will mean that growth rates will be somewhat low. Over 2024 and 2025, however, the business environment will improve. The outlook for manufacturers active in individual product segments is given below.
-
Manufacturers of parts and spares: Income will improve, with the domestic OEM market expanding with rising auto production and the REM segment benefitting from the steady expansion in the number of registered vehicles. However, the situation with exports is more uncertain, given the shaky outlook for US-China trade relations and the growing dominance of EVs in export markets, which is increasingly running counter to Thai exporters heavy focus on ICE parts.
-
Tire manufacturers: Players in this segment should see income grow but the July 2023 review of the anti-dumping measures by the US government that were originally implemented in May 2021 may result in an outcome that will increase the risk of manufacturers being locked out of the profitable US market. However, the REM market should benefit from the relentless increase in the number of registered vehicles.
-
Distributors of auto parts, spares, and accessories: Revenue will rise in line with the accumulated number of vehicles registered in the country, but competition is intense, and operators may be exposed to inventory risks.
-
Wholesalers and retailers of new parts and accessories: Demand for parts and spares and for decorative accessories which have a short lifespan will strengthen alongside rising sales of automobiles. Similarly, the growing number of autos on the road and the need among some owners to extend the life of their vehicles will also help to support increased demand for replacements and repairs, but the large number of players in this segment means that competition can be intense.
- Wholesalers and retailers of used parts and accessories (“Xiang Gong”): Operators in this group will see revenues rise in line with the growing national vehicle fleet, especially vehicles that are more than five years old. These vehicles would require more frequent repairs and replacement parts, and some vehicle owners may choose used parts to reduce cost. However, profits may be held back by a business model that requires operators to invest in carrying a wide range of stock, which in turn opens them up to the risk of holding outdated items and attendant problems with stock management.
OVERVIEW
The Thai auto parts industry has been the beneficiary of ongoing government support since 1963[1]. At first, state efforts to encourage investment in the domestic production and use of auto parts consisted of raising import duties on ‘complete built-up’ autos (CBUs) and ‘complete knock-down’ units (CKDs) but later, as it tried to encourage foreign companies to establish production facilities in Thailand, the Board of Investment (BOI) added to these policies by laying out its investment support measures, which included offering tax breaks to investors and waiving duties on imported machinery. In addition, the government put in place ‘local content requirements’ (LCRs) that set the minimum number or value of components and parts that had to be used in vehicles assembled in Thailand. LCRs have now been abandoned[2] but passenger cars manufactured in Thailand typically still contain 60-80% Thai-made parts (by value of the finished vehicle). LCR can reach 90% for eco-cars and pickups and is close to 100% for motorcycles. Important free trade agreements that affect the industry include the ASEAN Free Trade Agreement (AFTA), the Japan-Thailand Economic Partnership Agreement (JTEPA), and the Thailand-Australia Free Trade Agreement (TAFTA). One effect of the implementation of these trade agreements has been to cut the import duties placed on CBUs and CKDs.
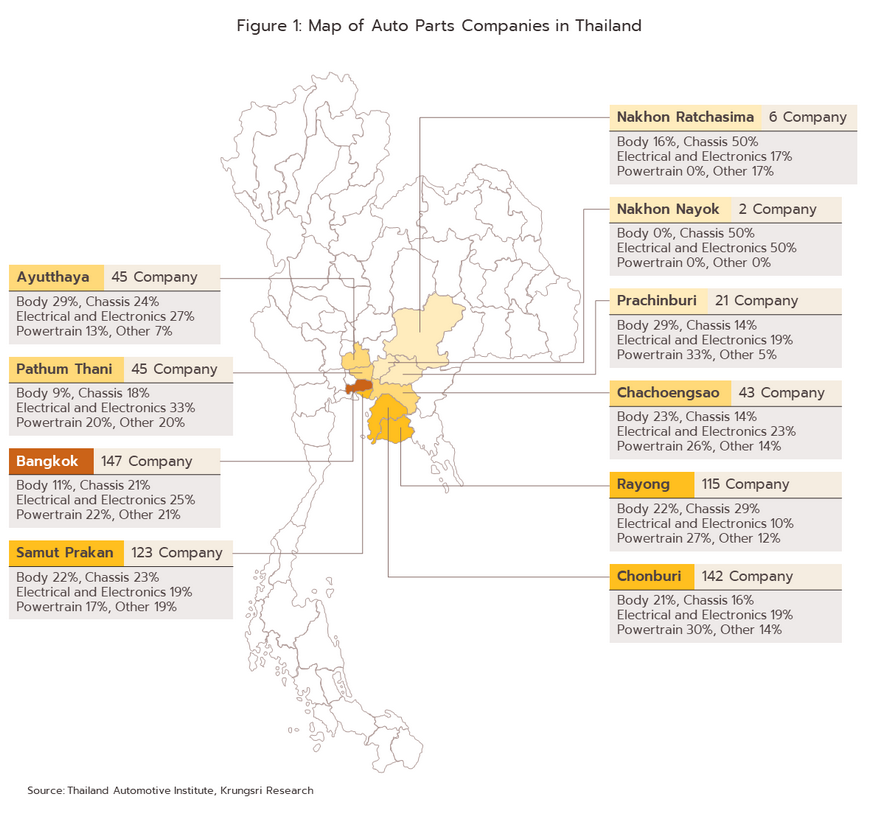
Up to the present, Thai and overseas investors have continued to set up Thai-based factories for the production of auto parts. The most important joint ventures and Thai-only operations include Thai Summit Auto Parts, Sammitr Auto Parts, Somboon Advance Technology, and Thai Auto Press Parts, while major international players active in the country include Robert Bosch, Denso, Magna, Continental, ZF, and Aisin Seiki (Table 1). The majority of overseas players in the industry have received some kind of investment supports for the production of: (i) parts made from rubber (which benefit from access to Thailand’s abundant supplies of rubber), including hosing, belts, window seals, and tires, the production of which uses high-tech processes; (ii) parts for the powertrain and engine, which in the case of producing internal combustion engines (ICEs), eat up a third of all manufacturing costs, though the government provides comprehensive support for manufacturers across the length of what are complex supply chains[3], including those connected to the production of radiators, exhaust systems, fuel supply systems, petrol tanks, ignition systems, and gearboxes; and (iii) parts for electric vehicles (EVs), for which the government is promoting a comprehensive investment package[4]. At present, there is a steady stream of applications from auto manufacturers looking to invest in the production of EVs and parts for these[5], in particular for the manufacture of batteries, a crucially important component in EVs and one which represents over 30% of all EV production costs.
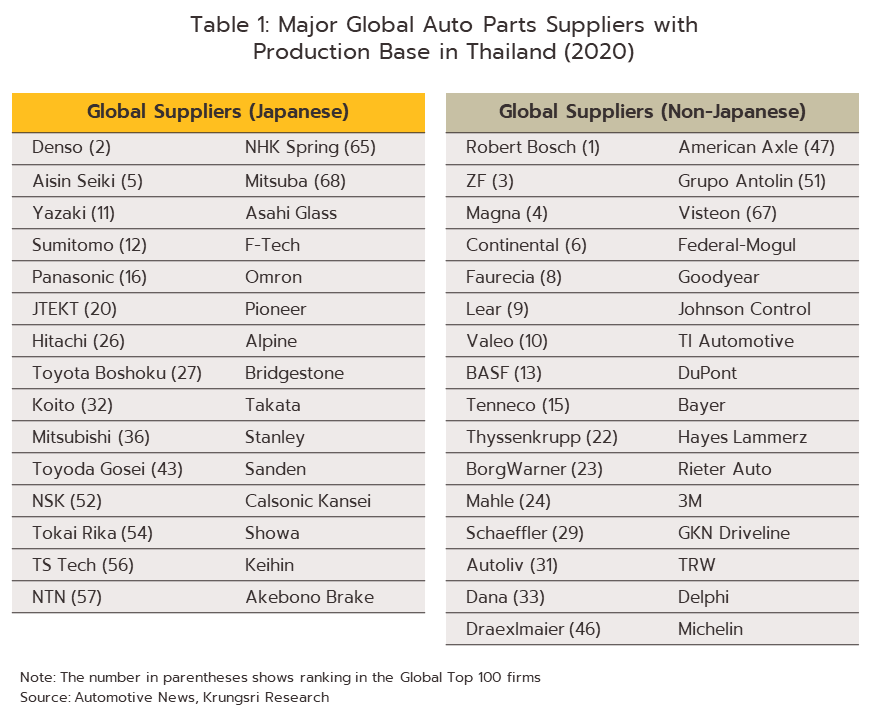
In February 2022, the government issued a new policy that will run until December 31, 2025, under which the government will provide subsidies to buyers of battery-powered passenger cars, pickups, and motorcycles. Under this scheme, manufacturers can import battery electric vehicles (BEVs) for domestic distribution over the period 2022 to 2023. However, auto manufacturers will have to compensate for any imports with increased domestic production of BEVs. If these vehicles are produced in 2024, the ratio of imports to production will be governed by the rule ‘Import 1, produce 1’ but if these come off production lines in 2025, the rule will change to ‘Import 1, produce 1.5’. The following regulations will also apply to vehicles manufactured to balance imports: (i) for imports of passenger cars equipped with batteries with a maximum capacity of not more than 30 kWh and a price of not more than THB 2 million, manufacturers may produce any BEV car for distribution in Thailand; (ii) for imports of passenger cars equipped with batteries with a maximum capacity greater than 30 kWh and a price between THB 2-7 million, manufacturers will be permitted to produce only the same model for distribution in Thailand; and (iii) for imports of motorcycles equipped with batteries with a maximum capacity greater than 3 kWh, or that have a maximum distance of 75 kilometers or more per charge, and that whose price is not exceeding THB 150,000, manufacturers may produce any BEV motorcycle for distribution in Thailand. Manufacturers may include pickups in the scheme only if these will be produced in Thailand over the period 2022 to 2025, their battery has a capacity of at least 30 kWh, and they have a price no higher than THB 2 million. It is hoped that the scheme will increase the usage of BEVs in Thailand, encourage auto manufacturers to begin Thai-based production of these, and help to generate greater demand for BEV auto parts (Table 2). As of December 2022, 12 companies had enrolled in the program, 9 auto manufacturers (MG, GWM, Neta, Mine Mobility, Volt, Toyota, BYD, Mercedes-Benz, and Honda) and 3 companies producing motorcycles (Honda, Deco, and H Sem).
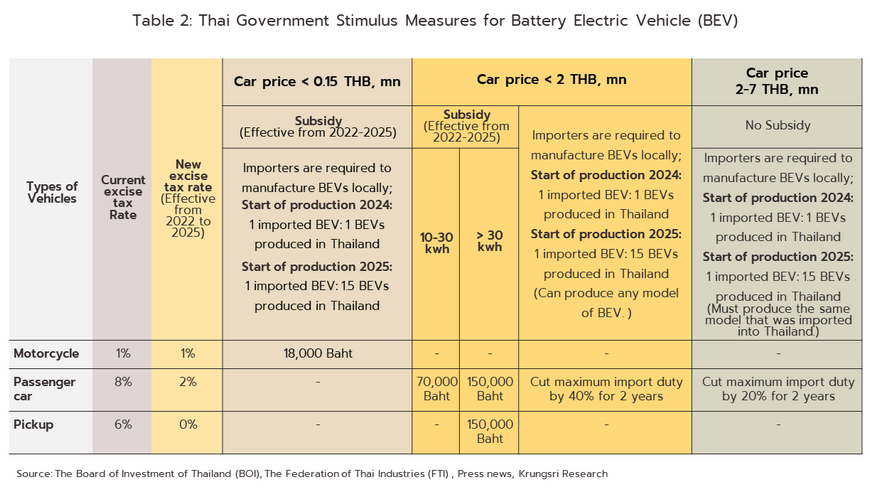
The auto parts market is predominantly domestic, and this supplies around 60-70% of income to the industry, although this is split between sales of parts that are used in vehicle assembly (the original equipment manufacturer, or OEM market) and the market for replacements and spares (the replacement equipment manufacturer, or REM market). Details of these are given below.
-
The OEM segment: This accounts for 30-40% of the value of the domestic auto parts market, though the outlook for this segment moves with overall output by the auto sector. Over 80% of auto parts used for the domestic assembly of vehicles are manufactured in Thailand, with those that are not made locally tending to be technology-intensive components that manufacturers import either directly from their parent company or from an overseas supplier to the parent company, such as the microcontroller chips (MCUs), which are imported from Japan to Thailand. In addition, parts for use in both ICE-powered vehicles and BEVs are imported from China for use in the Thai assembly lines operated by Chinese manufacturers.
- The REM segment: By value, around 60-70% of the domestic auto parts market is attributable to REM sales, which are growing with the expansion in the size of the national vehicle fleet. Demand for REM spares comes from the need to replace parts, and this is determined by the age and mileage of particular vehicles. REM spares are distributed through a number of different channels including dealers’ and distributors’ service centers, retailers and wholesalers of spares, and general garages. REM parts account for 10-20% of all imports of auto parts, with these coming from Japan (43% of all imports of REM parts, by value), China (17%) and the US (8%), though the latter is making greater inroads into the Thai market.
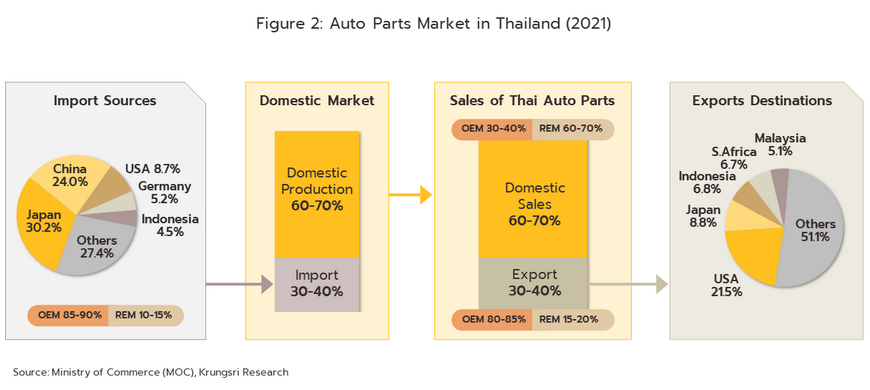
Receipts from the export of auto parts provide around 30-40% of income for the industry, split between OEM products (80-85% of exports of all auto parts by value) and REM goods (the remaining 15-20%). The most commonly exported goods are engines, electrical systems, body work, windows, gearboxes, tires and rubber products. Due to its extensive and well-developed supply chains, the Thai auto parts industry is able to generate economies of scale, and thanks to this and manufacturers’ ability to produce quality products that meet auto manufacturers’ specifications, Thai producers are highly competitive on world markets. Thailand is also lucky with regard to its location, which makes it a center of production in the ASEAN zone geographically as well as industrially[6]. Thanks to these factors, Thailand is a major supplier of auto parts globally and in 2021, exports of all types of auto parts from Thailand placed the country 1st in the ASEAN zone and 14th in the world. Considering just some of Thailand’s more important products, the country is 2nd in the world for exports of tires, 3rd for motorcycle parts (not including engines or tires), 13th for engines, and 15th for other automobile parts (excluding engines and tires). Exports are most often distributed to production facilities elsewhere in the ASEAN zone, including those in Indonesia, Malaysia, Vietnam and the Philippines, which combined take 22% of exports of auto parts by value, followed by the United States (22%) and Japan (9%).
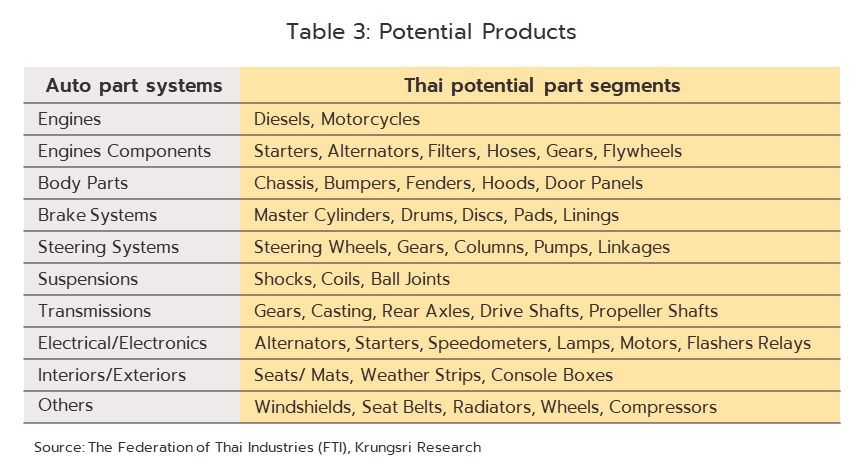
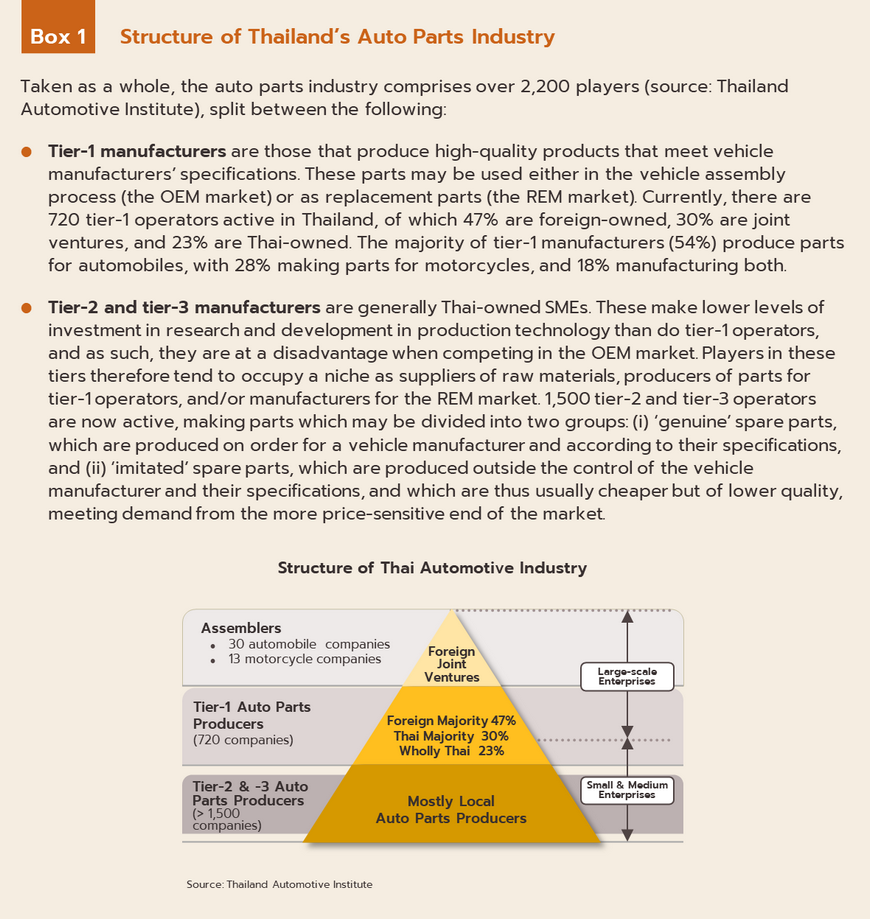
SITUATION
Auto parts production continued to expand through 2022, though the rate of growth in the industry’s manufacturing production index slipped to 3.5%, in comparison to 2021’s 25.3% expansion, despite a continuing rise in vehicle sales. The market was impacted by ongoing worldwide problems with chip shortages, which then resulted in periodic disruptions to supply chains across the industry, including in Thailand, where manufacturers depend on imports of these and other major parts. Preexisting problems were amplified by the outbreak of war between Ukraine and Russia at the end of February; both countries are major providers of inputs into chip production, especially of neon and palladium, and naturally, supply of these has now been disrupted. Alongside this, China introduced a wide-reaching lockdown in Shanghai, one of the world’s leading centers of chip and auto parts manufacturing, that ran from March 28 to June 1. Then in July and August, parts of the country were hit by a heatwave that shut down much hydroelectric power generation in the most seriously affected parts of the country. More broadly, the economic outlook has darkened through the year, and this has tended to undercut demand for auto parts on both domestic and international markets. For the year 2022, the production of autos and auto parts continued to be affected by periodic supply chain disruptions that will be driven by the intensifying tech war. Most recently, tensions have been ramped up by the enforcement from October 7, 2022, of America’s CHIPS and Science Act of 2022, which allocates USD 52 billion to the support of US-based chip production and outlaws the transfer to Chinese companies of specified semiconductor production technology (from KLA Corp, Lam Research Corp, and Applied Materials Inc). This followed the August 12 move to impose multilateral export controls that now block China and over 150 other countries from access to the US electronic design automation software that is used in the development of advanced integrated circuits. This will generate considerable problems for the Chinese chip industry as it looks to develop new products, and indeed, over 8M22, a historic high of 3,470 Chinese chip companies closed from a total of 47,000 across the industry. Nevertheless, these problems will be partly balanced by falling demand for chips for use in personal computers and mobile phones, with Gartner reporting that in 2022, global sales of these slided by respectively -16.0% and -11.0% as inflation eats into consumer spending power and prices rise with the higher cost of energy and inputs. Thai manufacturers thus found it easier to source automotive semiconductors from Q3 onwards, which will in turn help to ease the backlog of orders for autos and auto parts.
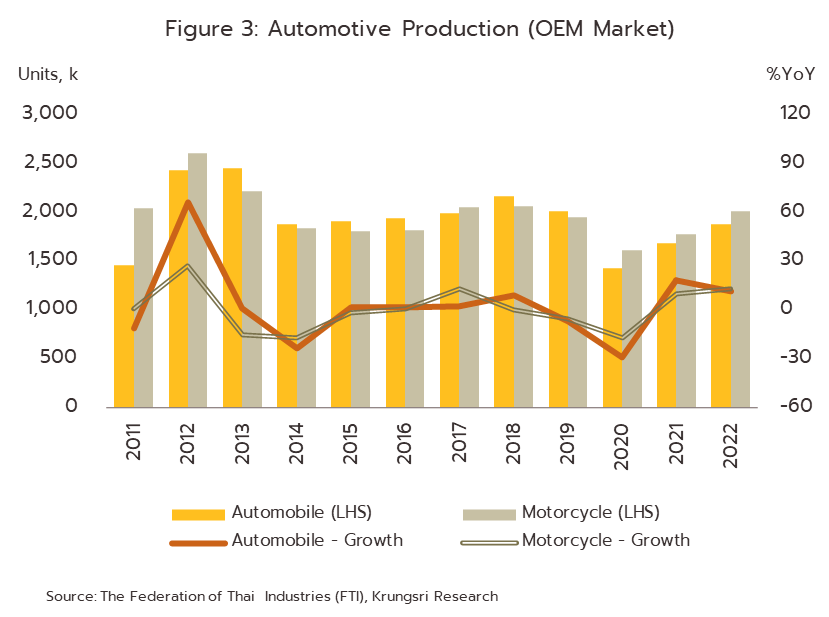
-
The domestic market has seen ongoing growth through 2022, though for the first half of the year, the OEM segment remained sluggish on only a 3% YoY rise in output of autos and the -7.1% YoY contraction in the number of motorcycles coming off production lines. The situation improved dramatically during the second half of 2022 with the ending of the Shanghai lockdown in June 2022 and the worsening global economic outlook, which fed into a softening of demand for PCs and mobile phones and this then freed up some semiconductor supply. Thus, the output of autos and motorcycles in the second half of 2022 surged by 20.5% YoY and 39.5% YoY respectively. At the same time, the REM market continued to grow because some consumers, faced with a worsening of their financial situation, have delayed the need to purchase new vehicles by spending more heavily on repairs due to weakening consumers’ purchasing power exacerbated by the rising cost of living and the impact of flooding in several areas. The output of autos and motorcycles in 2022 thus strengthened by respectively 11.7% and 13.2%, and with this, the market for auto parts will continue to grow.
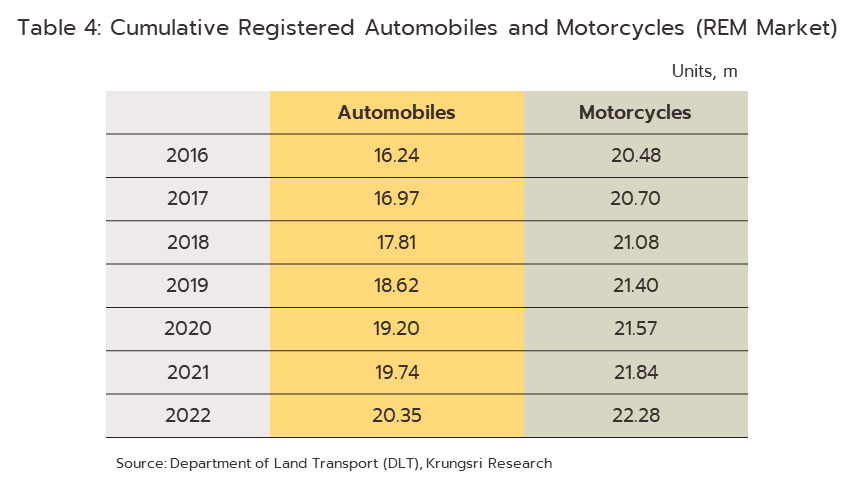
-
Exports contracted slightly at -0.3% to a total of USD 22 billion (by comparison, exports jumped 24.3% in 2021). The market was adversely affected by the year’s steep increase in inflation, which has eaten into consumer spending power and reduced demand for durable goods, including autos and auto parts.
-
Engines: By value, exports of engines stayed level at 0.01% to USD 4.2 billion, down from growth of 15.6% in 2021. Sales were very strong in some markets, including Hong Kong (+5,140.9%), China (+63.0%), the US (+31.3%), Malaysia (+34.7%), the Philippines (+32.8%), and Argentina (+11.4%), though these were mostly from the big Japanese players of Toyota, Honda, Isuzu, Mitsubishi, Suzuki, and Nissan.
-
Tires: Exports of tires increased by 4.8% to USD 6.9 billion in 2022, and although growth was down from 2021’s 20.4%,. Sales were supported by the continuing strength of the US market, which expanded 2.3% to USD 3.2 billion despite the introduction on May 27, 2021ม of anti-dumping measures by the US government targeting imports of Thai tires, specifically those for passenger cars and smaller trucks. Nevertheless, at 14.62% -21.09%, the duties on Thai imports remain below those faced by similarly targeted imports of tires from South Korea (14.72% to 27.05%) and Taiwan (20.04% to 101.84%). In addition, the ever-growing size of the US vehicle fleet is keeping the REM market buoyant, while consumers are also tending to put off purchases of new vehicles, which is again adding to demand; S&P Global Mobility estimates that as of 2021, the average age of vehicles on US roads has extended to a historic high of 12.2 years. Other overseas markets also remained strong in the period, with exports to the ASEAN zone up 18.0% to USD 876.7 million and those to the EU rising 23.2% to a value of USD 748.6 million.
-
Other auto parts: Exports other auto parts slipped -3.4% YoY to USD 11 billion on trading partners’ weaker economies -- the EU, Japan, and the US. Exports of other parts for automobile were down -3.3% to USD 9.8 billion, with declines of -15.1%, -7.5%, and -3.3% recorded for sales into markets in the EU, Japan, and the US. Likewise, exports of motorcycle parts dipped -4.4% to a value of USD 930.1 million. The two-wheel segment was pulled down by the poor performance of the Japanese market (with 10.8% share of motorcycle part exports by value, making it the 3rd largest), which slumped -33.4% (vs 81.3% growth in 2021). This was somewhat balanced by stronger sales to the ASEAN zone and the US (a combined 51.0% market share), which were up by respectively 4.4% and 1.8%.
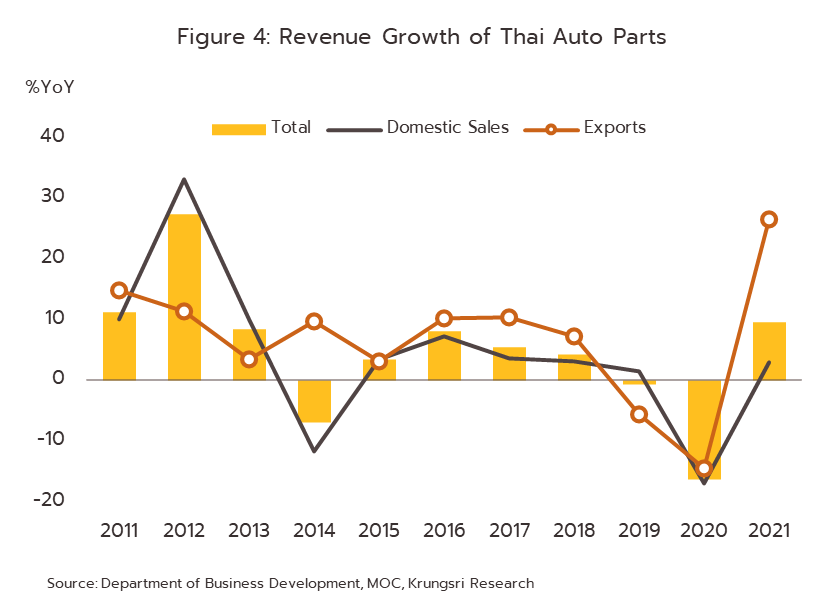
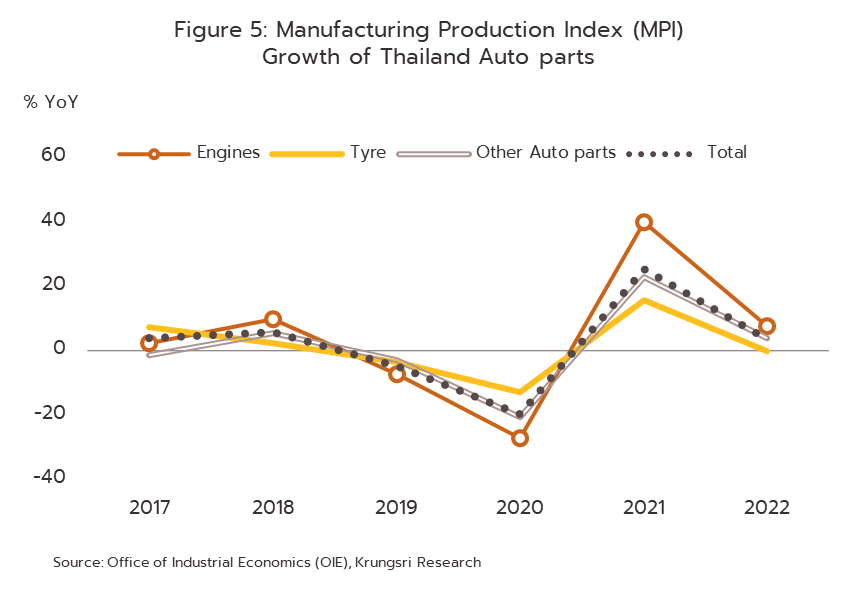
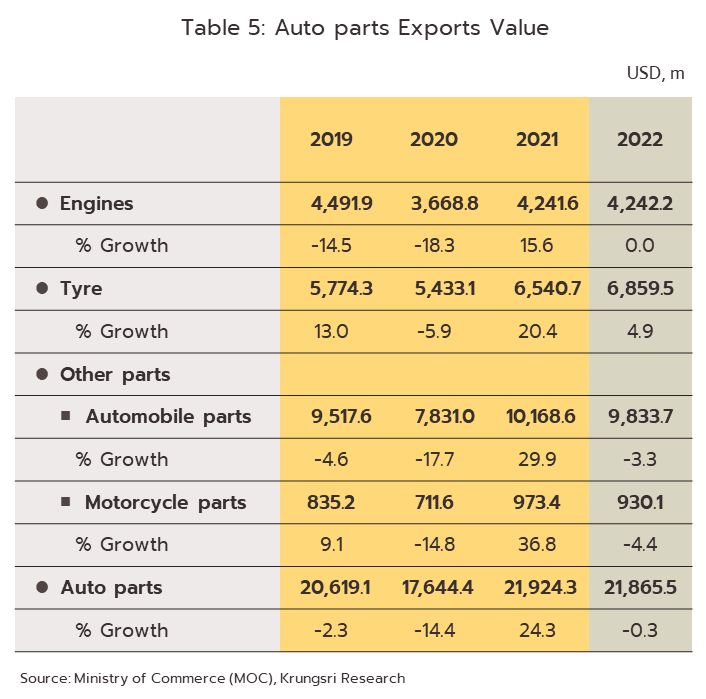
OUTLOOK
The output of auto parts is forecast to expand at the average annual rate of 3.5-4.5% from 2023 to 2025. Growth will remain somewhat constrained in 2023 due to the ongoing US-China tech wars and in particular the US block on the export of chip-related technology that will then likely trigger the periodic reemergence of problems with semiconductor shortages. The situation should improve in 2024 and 2025, and supply constraints will ease worldwide as investments start to bear fruit. The latter has included spending by the US, Germany, and Japan of respectively USD 52 billion, USD 10 billion, and USD 6.8 billion in new chip production facilities, as well as the USD 12 billion spent by TSMC (Taiwan Semiconductor Manufacturing Company Limited) on expanding its own wafer production capacity (source: Reuters). This will then support growth in the OEM market, while in the REM segment, demand will expand in step with the rise in vehicle numbers.
-
The domestic market will strengthen over 2023-2025. The OEM market will move with growth in the number of vehicles coming off Thai production lines (Table 6), which Krungsri Research expects will run to averages of 3.5-4.5% and 2-3% per year for cars and motorcycles respectively over the next 3 years. This will bring production back to close to its pre-Covid level by 2025, and so total output of motorcycles and autos will come to around 2 million vehicles annually. Demand for vehicles will be boosted by: (i) the easing of the pandemic and the space that this will provide for economic growth; (ii) the easing of tensions in crude markets generated by the war in Ukraine, which will then allow prices to fall back somewhat; and (iii) stronger demand for commercial vehicles that will be fed by an acceleration in work on government-funded infrastructure projects as phase 2 of the EEC development plan (Y2023-2027) is implemented, and by continuing growth in the e-commerce and logistics industries. The REM segment can also look forward to ongoing growth thanks to an average 5-6% and 9-10% annual expansion in the number of autos and motorcycles on the road that are over 5 years old; as these vehicles age and clock up ever more mileage, the need for replacement parts increases inexorably. However, growth in sales of accessories will likely be weak given the only mild increase in the number of motorcycles on the road that are less than 5 years old and the actual decline in the number of autos that are similarly aged (Figure 7 and Figure 8).
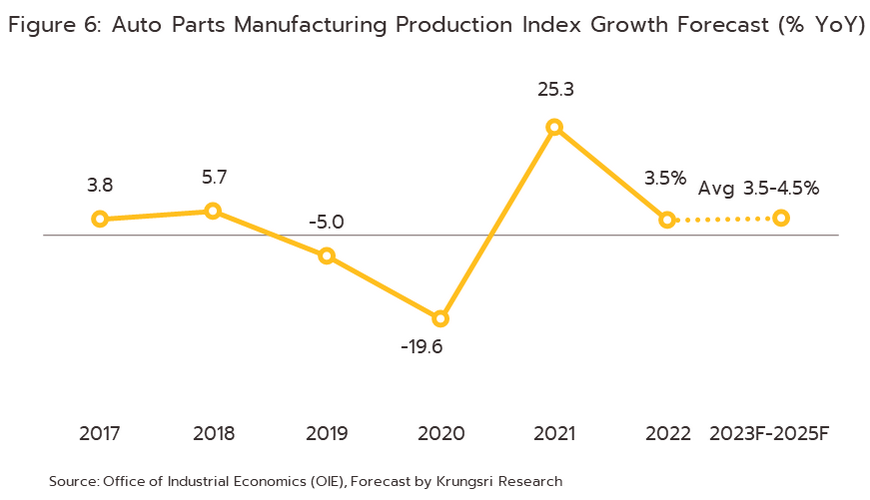
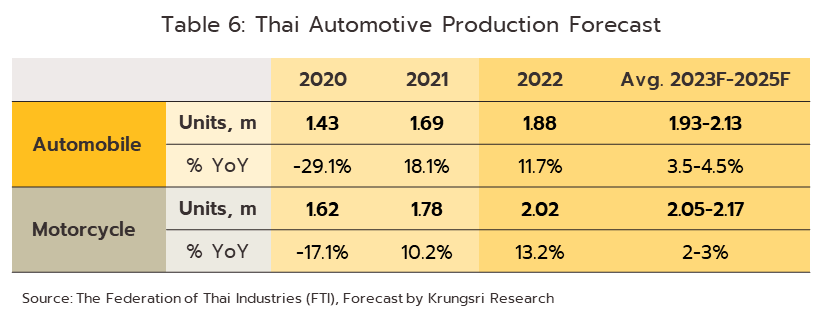
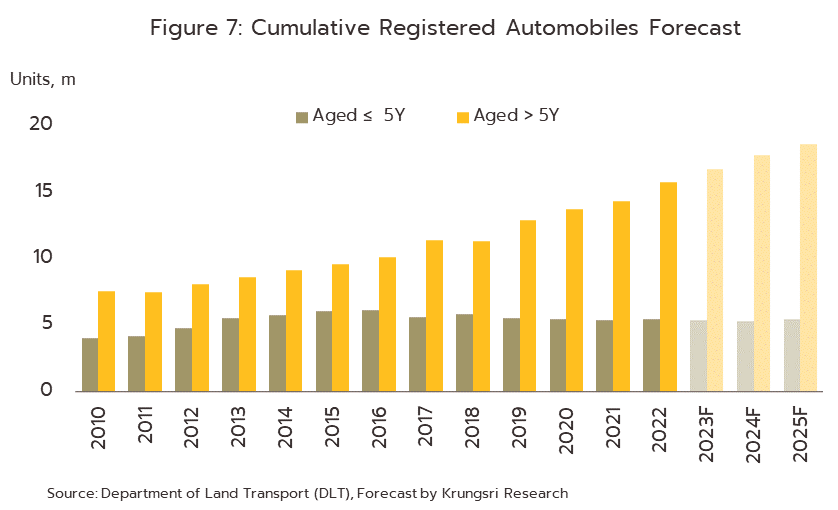
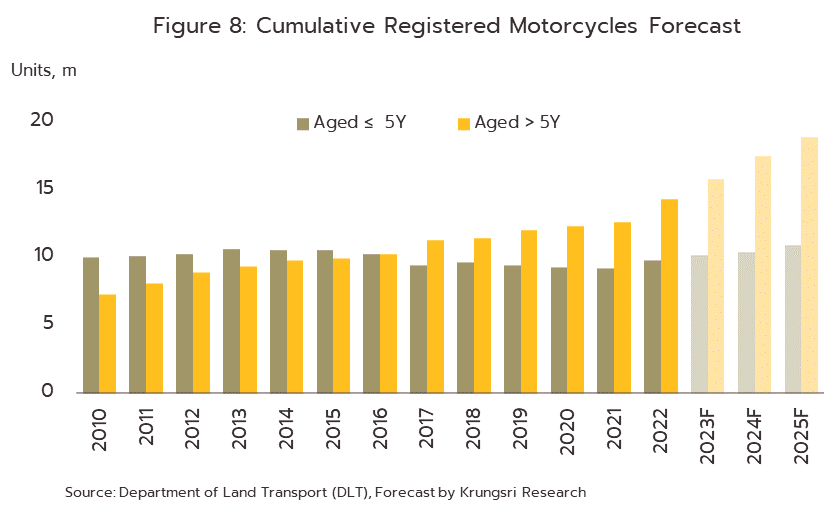
- Exports are expected to move in the same direction as the global auto industry over the next 3 years and to rise at an average annual rate of 2.0-3.0%. However, although Euromonitor (October 2022) sees stronger demand driving a 3-6% annual expansion in world auto output, exports of Thai auto parts will have to navigate headwinds generated by: (i) uncertainty over the direction of US-China trade relations; (ii) the raising of trade barriers by the major economies (e.g., the imposition of anti-dumping tariffs by the US authorities on imports of Thai tires); and (iii) the epochal shift currently transforming the industry as it moves from the production of vehicles powered by internal combustion engines (ICEs) to the output of electric vehicles (EVs). However, over the next 3 years, exports of Thai auto parts will likely remain overwhelmingly of components for ICE vehicles and although the government is attempting to encourage the domestic production of EVs and EV parts, these policies are likely to gain traction only with manufacturers that already have the potential to adopt new manufacturing technologies and to exploit the new export opportunities being opened up by rapid growth in the EV market.
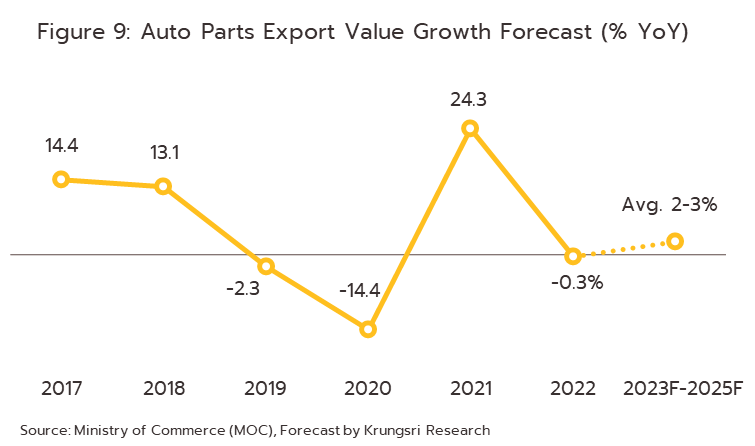
Clearly, the shift to the production and use of EVs will present a challenge to the auto parts industry and in some regards, this is being amplified by the government’s push to accelerate the pace of this transformation and to encourage greater domestic production of BEVs. At present, the government has put in place policies to promote the production and purchase of zero emission vehicles (ZEVs) that will run from 2022 to 2025. These have the goal of ensuring that by 2030, at least 30% of new Thai-made vehicles are ZEVs, with this increasing to 50% by 2035. The government has also set a target of at least 50% of all new vehicle registrations being ZEVs by 2030, with this escalating to 100% by 2035. Naturally, this will have dramatic consequences for companies manufacturing ICE-powered vehicles or parts for these, and the Thai auto parts industry is thus rapidly approaching an inflection point. As an example of the scale of changes faced by manufacturers used to producing for ICE supply chains, the powertrain of an ICE-powered vehicle typically contains more than 2,000 separate parts, whereas in an equivalent BEV, there might only be 20 components, and while in ICE vehicles, the engine is the most important part of the vehicle, in BEVs, the battery will be center stage and will account for some 30% of all manufacturing costs.
Investments are in fact beginning to be made in Thailand in the production of EV auto parts, especially for the manufacture of batteries, examples of which include the development and production of a nickel-metal hydride battery by Toyota and of a lithium-ion battery by BMW. As the EV market becomes more mature, the changing nature of auto supply chains will have consequences for the demand for a wide range of OEM parts, including engines, radiators, exhaust systems, fuel systems, petrol tanks, ignition systems, and gears, although demand for other product groups, such as the suspension, body work, lighting systems, and interiors will emerge from these changes relatively unchanged. Some BEVs also use electronic control systems to reduce wear on parts (e.g., tires and brake pads), while future automated driving systems will increase driving safety, and lower wear and the reduced number of crashes will feed into lower demand for REM parts.
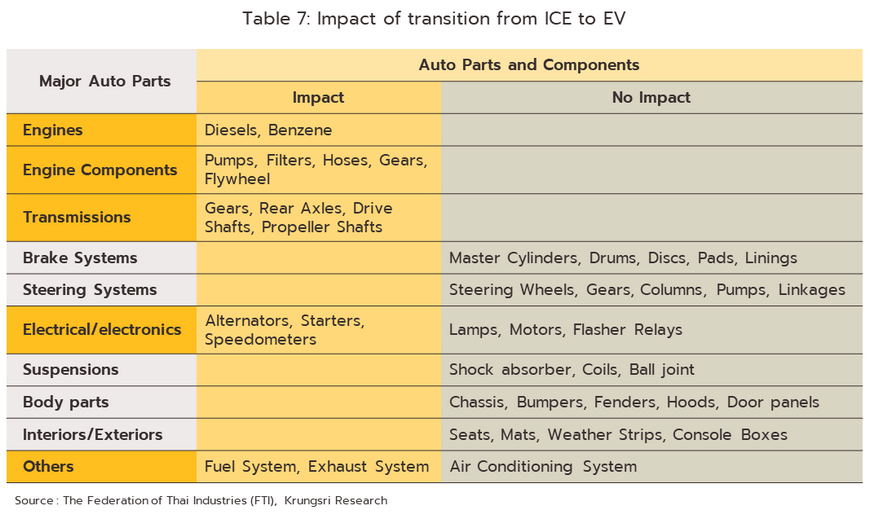
Thai auto industry supply chains will tend to be profoundly reshaped by the changes currently unfolding, and rather than participants in supply chains being connected in a strictly linear fashion, the industry will see the emergence of circular supply chains. That is, in traditionally arranged supply chains, orders pass along these in a fixed direction through the various layers of the auto parts industry (Figure 10), this consisting of: tier 1 suppliers, which produce goods that meet the quality control regimes set out by the major auto manufacturers, allowing them to supply these players directly; tier 2 suppliers, which supply parts to tier 1 producers and which may benefit from technology transfer from them; and tier 3 suppliers, small manufacturers that supply tier 1 and tier 2 players. Navigating linear supply chains like this is cumbersome and because it can take an extended period of time for an order to percolate through the various levels, to respond to the requirements of just-in-time delivery, it is often necessary for suppliers to maintain high levels of stock. This makes this kind of operation suitable only for the mass production of autos, when the economies of scales can justify supply chain structures such as this. However, the manufacture of EVs tends to be more dependent on robotic and automated production lines (as this ensures the necessary precision is maintained) and on the use of hi-tech end-user products. These include automatic driver assistance, automated impact detection sensors, automatic speed controllers and on-board systems that connect with on-line data that is then used to make the travel experience as smooth as possible, for example by collecting data on the weather, road and traffic conditions or by downloading relevant maps. In the future, this will also extend to providing ever-higher levels of automated driving assistance (Figure 11).
Because of these differences, the structure of EV supply chains often diverges markedly from those for ICE-based production, taking a circular, networked form rather than existing as a straight line from start to end (Figure 12). This network will generally consist of auto parts suppliers, device manufacturers, telecom companies, online players and IT suppliers, and within this web of connections, the various participants have non-hierarchical relationships with one another. This then helps to make production quicker and more flexible, while doing away with the need for companies to maintain excessive stocks, and the result is that the system is better able to respond to a wider variety of needs. In light of these changes, when responding to the emergence of EV-based supply chains, OEM auto parts manufacturers will need to adapt across a broad front that encompasses technology, manufacturing, and management and organization, all the while keeping a firm focus on how best to add value to products, rather than simply mass producing at the lowest marginal cost.
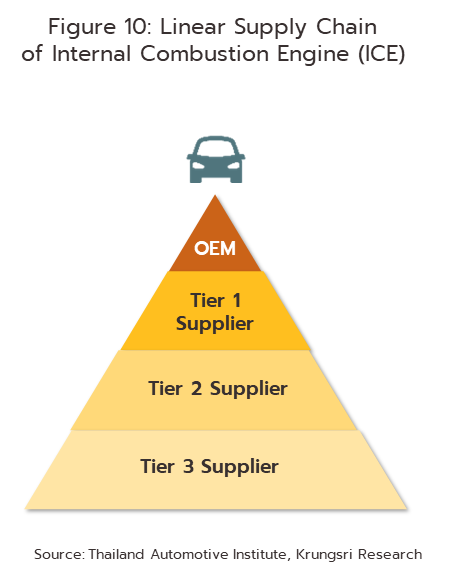
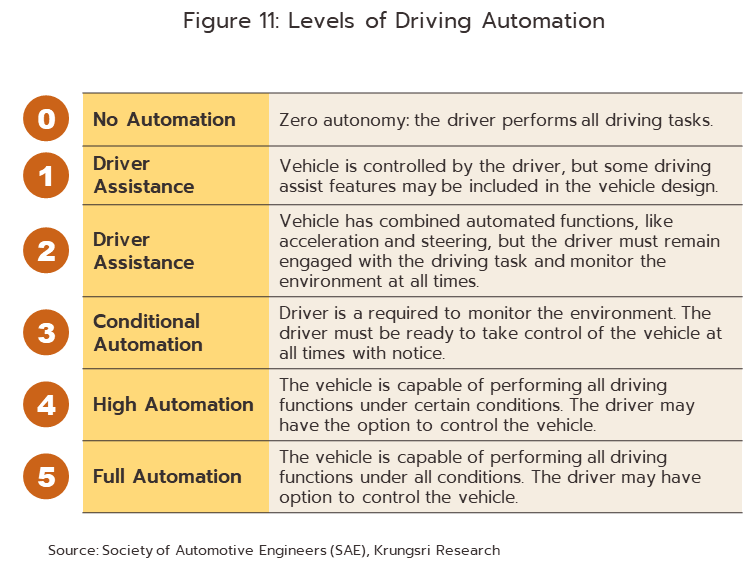
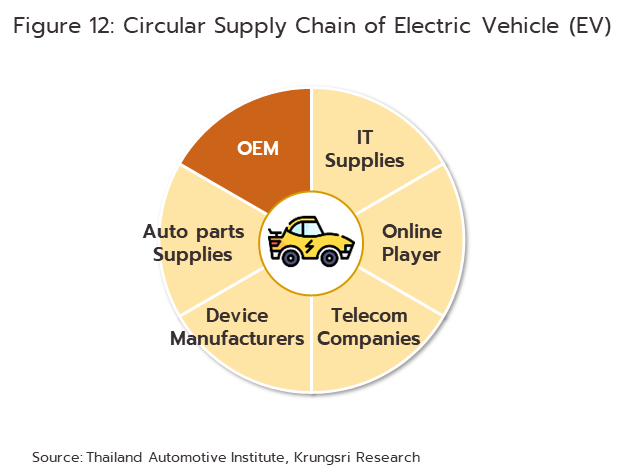
[1] The first period of development of the Thai automobile industry involved the import of ‘complete knock-down’ (CKD) units from foreign manufacturers or their subsidiaries. These were then assembled in-country as ‘complete built-up’ (CBU) vehicles
[2] The World Trade Organization (WTO) prohibits all member states (including Thailand) from specifying local content requirements and so the Thai authorities abandoned these on 1 January, 2000.
[3] Engines production is composed of over 2,000 different parts and components
[4] This is with regard to both assembling vehicles and manufacturing the key auto parts, including batteries for EVs, traction motors, electric-powered air conditioners and parts for these, battery management systems, driving control units, on-board chargers, charging lines (with sockets and plugs), DC/DC converters, inverters, portable electric vehicle chargers, electrical circuit breakers, front and rear axles for electric buses, and programs for developing EV smart charging systems.
[5] Companies that have applied for investment support for the production of EVs and EV components include the following:
•Hybrid electric vehicles (HEVs): Toyota, Honda, Mazda, Nissan, and Mitsubishi
•Plug-in hybrid electric vehicles (PHEVs): Mercedes-Benz, BMW, MG, Mitsubishi, Audi, Toyota, and Mazda
•Battery electric vehicles (BEVs): FOMM, Mercedes-Benz, MG, Audi, Mazda, Mine, Toyota, Honda, Mitsubishi, Nissan, Sky well, Takano Auto and Suplaor
•Batteries for EVs: Toyota, Honda, Mercedes-Benz, Nissan, Mitsubishi, BMW, MG, GWM, Energy Absolute, AMITA Technology Thailand, ARUN PLUS, NUOVO PLUS, BANPU Next, and Global Power Synergy
[6] From ‘Thailand’s Economic Integration with Neighboring Countries and Possible Connectivity with South Asia’, ADB Institute